The passive path to zero energy
By Katrin Klingenberg
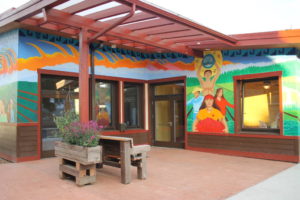
Images courtesy GreenHammer Design
Buildings are getting tighter from both the regulatory and consumer-demand sides. As energy codes get steeper and consumers desire more sustainable options, builders, contractors, and architects face new challenges for meeting these standards and expectations without opening the door to unintended consequences. Indeed, there have been many building failures since contractors began to place insulation inside walls in the 1930s.
The good news is a lot can be learned from those errors. Scientific research, best-practice guidelines, and certification systems can help design/construction professionals sidestep building failures while delivering high-performance buildings. When inexpensive solar panels are added to the mix, buildings that produce as much energy as they use are actually within reach.
Steps on the path to net-zero
Gone are the days of steel stud walls with batt insulation. Thicker walls are the new normal, and with them come nonstandard details for constructing buildings. The path to a zero-energy building begins with where it is located. The climate zone is the critical first step, because it defines what the project is up against.
Next, one should look to the 2015 National Energy Code of Canada for Buildings (NECB), because the construction phase is the most economical time to make a building energy efficient. For higher energy targets than the code, it is best to seek Leadership in Energy and Environmental Design (LEED) certification or join Natural Resources Canada’s (NRCan’s) National High-performance Building Challenge.
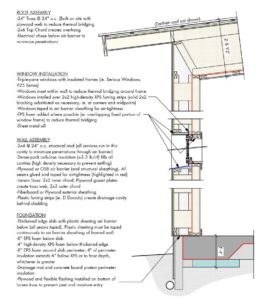
The smoothest path to net zero, however, is through passive building certification, because a passive building is a complete system with quality assurance built into the system, rather than a collection of discrete programs. The most common passive building certification in North America is PHIUS+, administered by the Passive House Institute U.S. (PHIUS), because it aligns with both NECB and International Energy Conservation Code (IECC).
Passive building principles
Fast-forwarding past the in-depth physics of passive building, the five building science principles of the method boil down to the following points.
Continuous insulation interrupts thermal bridges between inside and out.
By completely wrapping a building with insulation, heat can no longer sneak out through framing, which has a lower R-value than the insulation between the studs. Masonry chimneys that connect inside and out are another example of an often-overlooked thermal bridge.
Airtight construction stops heat and moisture.
While thick continuous insulation (ci) can stop a significant amount of heat loss, plugging air leaks can also slow heat flow, because air that moves through buildings usually carries a lot of heat. Further, warm air can hold more moisture than cold air, so when warm air leaks into exterior wall cavities, it dumps moisture into the wall cavity when it hits the cold wall sheathing or drywall, depending on the season.
Optimized windows let in heat when (and only when) you want them to.
Double glazing with argon gas is typical of Energy Star windows. Passive buildings usually have triple glazing. Low-emissivity (low-e) coatings applied to the surface of the glass can be fine-tuned to the desired amount of heat gain. Windows with high solar heat gain co-efficients (SHGCs) should be used on sides of the house where winter sun is wanted (generally on the east and south sides). Low-SHGC windows should be used where summer sun will do the most harm (generally west-facing windows).
Balanced ventilation ensures fresh air and controls moisture.
All the aforementioned air tightening means dirty, moist air is not leaking into the living space, so air changes must be controlled with some sort of high-tech fan. One option is an energy recovery ventilator (ERV), which pulls new air in and pushes old air out while transferring heat and moisture in the process.
Minimal mechanical is all a super-tight building needs.
As the building is super-tight, super-insulated, and has ‘super windows,’ super-sized heating and cooling systems are unnecessary. This is where the upfront investment begins to pay off. Some of the money spent on insulation and windows can be recouped with much smaller mechanical systems.
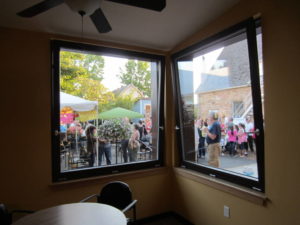
When these five principles are applied to buildings, the result is predictable performance, unmatched comfort, superb indoor air quality (IAQ), and resiliency in the face of power outages due to winter storms or summer blackouts. Best of all, because passive buildings consume so little energy, zero energy is easily within reach. Just adding a small renewable energy system, such as a photovoltaic (PV) assembly, can place design/construction professionals at the end of the path to zero.
Some of the techniques discussed in this article will be explored in greater depth at the 12th annual North American Passive House Conference in Seattle, running September 27 to October 10. For more information, visit the event’s website.
Katrin Klingenberg is executive director of the Passive House Institute U.S. (PHIUS), an organization committed to making high-performance passive building the mainstream market standard. Klingenberg holds a degree in architecture from Ball State University, and is a registered architect in Germany. In 2015, she won the Women in Sustainability Leadership Award (WSLA). Klingenberg can be reached via e-mail at info@passivehouse.us.