The nuts and anchor rods of lighting poles
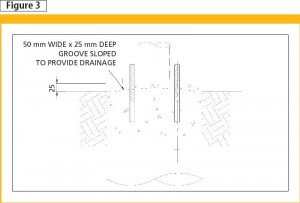
Increase concrete cover
Adequate concrete cover over steel is essential for footings exposed to the elements. As seen in Ontario Provincial Standard Drawings (OPSD) 2200.01, “Concrete Footing for Base Mounted Lighting and Signal Poles” (Figure 3), the concrete footing’s upper section is exposed to weather, while the lower portion is exposed to earth. In this case, earth is used as formwork to hold the concrete. A 75-mm (3-in.) concrete cover over steel reinforcement bars specified in concrete codes such as CSA A23.1–04, Concrete Materials and Methods of Concrete Construction and National Building Code of Canada (NBC) should be applied.
Protection of anchor bolts
Anchor bolts are the most commonly used method to secure poles to concrete footings. Normally, anchor bolts are hot-dip galvanized steel. Although galvanized, the threads of anchor bolts and nuts are the easiest parts to corrode due to excessive surface area, acute shape, and severe exposure.
As rust has a much higher volume than the originating mass of steel, its buildup can cause failure by forcing adjacent components apart—a phenomenon sometimes known as ‘rust smacking.’ Reinforced concrete is also vulnerable to rust damage. Internal pressure caused by expanding corrosion of concrete-covered steel can cause the concrete to spall, leading to bond breakage between the steel and the concrete.
As part of the footing’s design, its top part is dome-shaped or grooved. This allows the rapid drainage of surface water. It is also recommended the top of the footing is specified to be at least 75 mm (3 in.) above the finished grade.
Understanding OPSD
The design of a lighting pole and its concrete footing have been standardized in Ontario for many years. OPSD specifies concrete footing with parameters as follows:
- burial depth;
- size and length of reinforcement bars;
- 75-mm (3-in.) minimum concrete cover; and
- the footing’s height above the finished grade line.
In OPSD 2200.01, the footing’s height above the finished grade line is specified as 25 mm (1 in.). Four 25 x 50-mm (1 x 2-in.) deep grooves sloped on the concrete footing are required to provide drainage. These elements are used to prevent the corrosion of steel anchor bolts and nuts.
In practice, the 25 mm specified in OPSD is too small to prevent anchor bolts from corrosion. Commonly, the concrete footing of lighting poles installed several years ago have been buried in earth. This would cause the anchor bolts and nuts to rust due to exposure to excess moisture over a prolonged period.
Further, for esthetic reasons, at the pole’s bottom, a set of aluminum flash collars are used to mask the anchor bolts and nuts, which also tend to hide the problem of rusting anchor bolts. It is often surprising to see what is below the covers when they are removed.
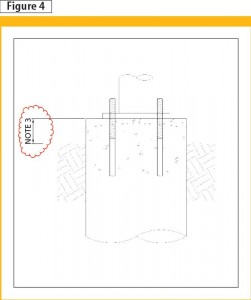
The revised OPSD 2200.01 (Figure 4) was updated in 2005; it includes the increase:
top of footing shall be installed at 40 mm ± 15 mm [1.6 m ± 0.6 in.]above finished grade in paved or concrete areas and 75 mm ± 25 mm above [2.9 in. ± 1 in.] finished grade in earth or granular areas.
This is a great measure to prevent anchor bolts from corrosion.
OPSD 2200.01 does not have notes specifying the concrete mix design such as the strength and durability. It is recommended everything is put into one document (i.e. drawing or specification), including:
- concrete strength after 28 days shall be 25 MPa (3500 psi);
- concrete shall be mixed in w/c ratio equalling 0.4; and
- air-entrained concrete with five to seven per cent air content should be used.
Repair of rusted anchor bolts and nuts
The lighting poles installed in the 1970s and 1980s have been standing for 30 to 40 years. After this amount of time, these anchor systems should be field-inspected and measures taken to attend to any corrosion problems.
In the early stage of anchor bolt corrosion, where embedded bolts are still secured in the concrete, only the threaded parts and nuts may be completely corroded and unable to further secure the pole. The steel base plate and concrete footing are sometimes still in good condition. It is good to re-tap the rusted anchor bolts again and put in new nuts to secure the pole. Rustproofing materials to cover the bolts and nuts should also be applied when the job is done. Black asphalt undercoating can be used.
If the anchor bolts are completely deteriorated, and the top concrete cover is also loose due to the expanding corrosion of anchors, more invasive ‘surgery’ has to be considered. The necessary repair of the concrete footing and anchors is a costly job. It roughly follows these steps:
- disconnect the electrical wires;
- remove the steel lighting pole;
- cut off the existing concrete until the fresh anchor bolt shows up;
- saw-cut the rusted bolts off;
- connect the new galvanized threaded rod extensions with hex coupling nuts;
- set-up fibre tubing formwork;
- roughen the concrete surface and apply bonding agent;
- fill concrete and raise the top of footing to 100 mm (4 in.) above grade;
- cure concrete for a minimum of seven days; and
- re-install the lighting pole and re-connect electrical wires.