The need for energy performance targets
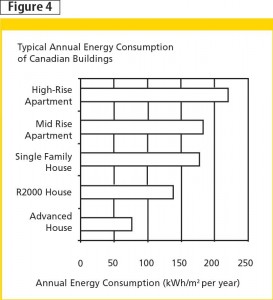
Image courtesy Canada Mortgage and Housing Corp.
It is time for a new standard for energy performance to be combined with the existing building commissioning standard to result in energy cost savings and better rankings. North American buildings also need airtightness and high-performance insulation—such as the aforementioned VIPs with R-values of up to R-60 per inch (Figure 5). Efficient envelopes and HVAC, combined with renewable energy-producing systems integrated into buildings, can raise Canadian performance levels to NZEB status, as in Europe.
According to a recent survey by the North American Insulation Manufacturers Association (NAIMA), 70 per cent support mandatory energy labelling of houses. (For more, see “Ontarians Support Home Energy Labelling” at www.constructioncanada.net/newsletters). In most of Europe, Energy Performance Certificates (EPCs) are required for all real-estate listings and rental units in order to provide transparency and consumer protection. Canadian experts are among those working on a similar ISO standard—Energy Performance of Buildings using Holistic Approach—that is based on British Standard (BS) EN 15217, Energy Performance of Buildings: Methods for Expressing Energy Performance and for Energy Certification of Buildings. It should be relatively easy to adapt for Canadian use upon its expected publication next year. For both new and existing buildings, this standard could be used to disclose energy use and enable homebuyers or renters to compare the energy consumption for different property listings. Consumers should be able to make better-informed choices once they know one home’s annual energy consumption is 335 kWh/m2 and another is between 50 and 0 kWh/m2 (F and A ratings, respectively, per Figure 6).
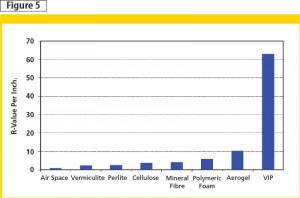
Image courtesy National Research Council
The Canadian Commission on Building and Fire Code (CCBFC) approved the task of setting specific EUIs for buildings, which will likely be based on building occupancies. The NRC-established Task Force on Energy Targets is intending to release proposed EUIs for new buildings in 2013 to be incorporated in the 2015 National Energy Code for Buildings (NECB).
Establishing EUIs takes the current prescriptive energy requirements and allows a more flexible code compliance path to translate them into a quantitative performance target (i.e. ekWh/m2/yr). For example, large offices in Toronto (Climate Zone 5 per American Society of Heating, Refrigerating, and Air-conditioning Engineers [ASHRAE]) will have a proposed EUI of about 205 ekWh/m2/yr.
Toward NZEB with employing innovative systems
The 2011 NECB, along with provincial codes (e.g. Ontario and B.C. Building Codes [OBC and BCBC]) and various city ordinances (e.g. Vancouver), have created an opportunity for manufacturers to come up with innovative solutions in building envelopes. The current National Energy Code for Buildings aims to achieve 25 per cent less energy use than code requirements set in 1997 and the European Union goal of nearly zero. This provides fresh impetus for the next generation of energy-efficient insulating materials such as VIPs (Figure 7).
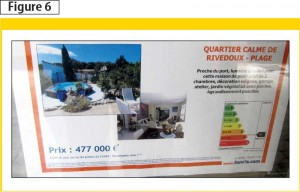
Photo courtesy Cedaridge Services Inc.
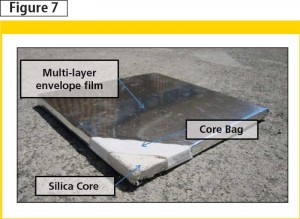
Photo courtesy Dow Corning Corp.
Fortunately, there are VIPs developed in North America that can provide a 15 to 20 per cent R-value improvement and an estimated 10.5 per cent lifecycle cost (LCC) reduction with VIPs and double-pane windows in comparison with mineral wool and double-pane curtain walls for large, archetypal Canadian office buildings (Figure 8).
In this author’s opinion, VIPs and double-pane windows are the best LCC solution in Climate Zone 5, and should be considered not only in Ontario (where the Ontario Building Code has, since the start of 2012, mandated a 25 per cent improvement in energy efficiency over 1997 Model National Energy Code for Buildings [MNECB] for buildings), but also anywhere in Canada due to the low-LCC basis.
By integrating VIPs (with an average 18 per cent energy improvement) and the standard four-phase holistic commissioning process (with an estimated energy savings of 15 per cent), a total savings of about 33 per cent
can be achieved, though the savings are not exactly cumulative. This is better than the 25 per cent improvement required by OBC.
The U.S. Lawrence Berkeley National Laboratory (LBNL) discovered enhanced commissioning had energy savings of 13 to 16 per cent, with paybacks of 1.1 to 4.2 years. To achieve these higher performance targets, it is critical to integrate improved insulation, more efficient HVAC, and renewable energy-producing systems into the building at the pre-design phase.
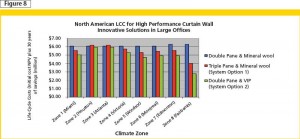
Image courtesy Cedaridge Services Inc.
VIPs and renewable energy
VIPs can improve the energy efficiency of the building envelope and reduce up to 70 per cent of the emissions and energy costs. Its discrete ‘interior’ application makes it suitable for existing building stock, and can assist in projects looking to retain the cultural heritage of older buildings. Energy-efficient slim construction can be achieved by applying vacuum insulation panels or sandwich elements due to their low thermal conductivity.
At the University of Birmingham in the United Kingdom, VIPs were installed (as shown on page 40), with thickness of the panels optimized to 18 mm (0.7 in.) to achieve a 0.239 U-value W/m²-K in the spandrels. As part of building commissioning in the construction phase, a thermographic survey (Figure 9) confirmed there are no apparent defective panels; the product type seems to be working well, given significantly reduced heat loss recorded through the spandrel dual sealed insulating glass (IG) units and seals. (The areas highlighted in yellow show areas of warmth. These are due to trickle vents and rubber seals around the glass.)