The multiple purposes of air barriers
by Jay Saldana, PE
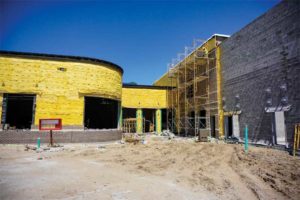
The need for energy-efficient buildings is the largest driving factor behind product innovation and building science advancements in air barrier materials. However, other equally important aspects of modern construction are sometimes overlooked by building professionals.
Manufacturers continue to improve their products to extend a building’s durability and lower the costs of construction. The developments in air barrier products over the years reflect a constant demand for airtight, mechanically ventilated buildings to meet ever-changing energy codes and expectations among builders and architects for higher performing facilities. There is also pressure to find ways to design a building that could function properly in any climate or environment. Therefore, understanding the progression of air barrier materials will help professionals at all levels of the building design process choose the best air barrier system for their project.
Evolution of air barrier materials
The importance and inclusion of an air barrier material is not questioned by today’s builders and architects, but not long ago, a structure’s air barrier did not comprise a single membrane. With painstaking detailing of joints and transitions, interior gypsum was largely employed to reduce air leakage, knowing it had the help of other materials in the exterior wall for slowing down leakage. Since then, the function, design, and construction of an air barrier, not to mention how it is specified, has been constantly changing. It is important to remember how far the products and systems have come to fully appreciate and better understand how to utilize them in present day construction.
Building wraps
Building wraps were among the early products to act as an exterior air barrier material and had the advantage of being vapour permeable. Even after the creation of the U.S. Department of Energy (DOE) in the late 1970s, there was still a lack of advanced science and consensus of where vapour retarders and insulation should go in an exterior wall.
A ‘breathable’ exterior wall (i.e. a wall with materials facilitating drying by air movement or vapour permeability) was thought to be the only way to prevent moisture damage. Building wraps could fit this design method by allowing vapour through the material but preventing the passage of liquid water and air.
Installation of the wraps was the biggest challenge. They had to be fastened frequently and attached with precision. It was not uncommon to see wraps flapping in the wind on a construction site simply because it was not taped at the joints or attached to the building correctly. The product itself worked, but the method in which it needed to be attached and the lack of high-quality workmanship in installation led to the next generation of air barrier materials.
Self-adhered membranes
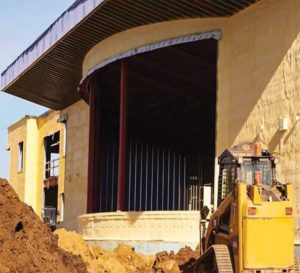
Photos courtesy Icynene-Lapolla
When self-adhered membranes came into the market, they were instantly thought to be superior to wraps as they adhered to walls without the need of a fastening pattern. Some contained self-healing qualities and sealed screw penetrations or small slices made to the membrane during construction. While these products proved more reliable, the installation process was long and depended on temperature-sensitive adhesives. When these products were first introduced, there was a period of trial and error by manufacturers with adhesives—some work better in the heat, some in the cold, and very few work well in both. Dirty and dusty substrates also contribute to adhesive failure. The self-adhering membranes sometimes required a termination bar that had to be fastened down over the membrane edge as it was common for certain edges of the membranes to peel.
Originally, peel-and-stick membranes were vapour impermeable, but as the breathable exterior wall concept spread, manufacturers developed vapour permeable versions. This transformation required years of research and new technology to allow vapour through the adhesive and the facing of the membrane.
Fluid-applied barriers
Fluid/liquid-applied barriers were another jump in the air barrier product industry. The first versions could be spread by trowel and adhered in place on the wall, thereby becoming both the air and water barrier. Spray and roll-on versions were created as thinner applications but both thicknesses accomplished the same goal of being the air and water barrier. While self-adhering membranes evolved over time, the manufacturers of fluid-applied barriers learned from their predecessors, and soon had both vapour permeable and impermeable versions. Fluid-applied barriers are thought to have even less possibility for error in installation than self-adhered membranes. They can cover corners and angles better than self-adhered membranes, which take some skill to accomplish the tricky bends and folds. While this was a huge advancement and reduced the time of installation, in the author’s experience, the higher cost of these products often resulted in them being ‘value engineered’ out of the project.
A further advantage of fluid-applied barriers over self-adhered membranes is the lack of the membrane itself. Often, compatibility with various caulks and sealants must be tested not only with the adhesive, but also the membrane. Fluid-applied barriers are more often compatible with such construction materials and capable of being applied to them. A self-adhered membrane would have a very hard time transitioning and adhering to an irregular surface such as the face of closed-cell spray foam. Conversely, a fluid-applied product can fit into the irregularities of the surface and achieve a solid bond. In constantly wet climates, such as British Columbia, caution must be taken with self-adhered membranes as their adhesive is typically sensitive to wet surfaces. Many fluid-applied barriers advertise their applicability while actively raining so work may continue.