The kitimat modernization project
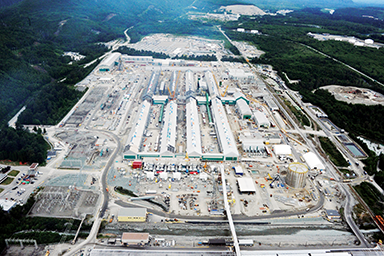
By Jan Vrana, P.Eng.
In 2009, Montréal-based international corporation Rio Tinto Alcan began the process of modernizing its aluminium smelter located in Kitimat, B.C. To provide space for the new smelter, several existing facilities were dismantled and the area was cleared. Additionally, two lodging camps for workers were built.
Bechtel Canada was contracted to become the engineering procurement contract manager (EPCM) for the Kitimat Modernization Project (KMP). The plant required new grading, and deciding on the final levels for each building was one of the project’s challenges.
The entire site covers approximately 600 x 1000 m (1968 x 3280 ft) in the main area, plus a smaller additional portion. To appreciate the challenge, the geological and geotechnical conditions of the site must be understood. Design teams had to rely on a geotechnical report by Klohn Krippen Berger Limited (KCBL) that outlined Kitimat’s geological history.
Kitimat history
In the pre-glacial era, the site was hundreds of metres higher than sea level; Kitimat River cut deep into the valley, as evidenced by different rock types on each side. During the glacial period, ice further moulded the valley. Today, the area just south of the plant is a fjord with steep mountains on each side and a flat bottom. Glacial ice depressed the area and there is evidence that at one point the sea reached further up the valley than today. Rivers from melting glaciers deposited sediments into the valley with finer soils deeper into the fjord.
As the land gradually rose, the sea moved out of the valley to the edge of the town of Kitimat and the plant location. Large amounts of sediment deposits resulted in thick layers of silt over a deep bedrock or glacial till, with some sand and gravel deposited over the silt by smaller streams coming from the sides of the mountains. In some areas, thinner organic layers can be found, likely from top soil slides in the tidal zones.
Bedrock depth in the area varies from several metres on the west side to 120 m (393 ft) on the eastside. Consequently, the silt layer thickness varies correspondingly and reaches over 60 m (196 ft) from the bedrock, closer to the finish grade. The silt layers are highly compressible, but top level varies significantly, complicating settlement predictions.
Prior to the original construction, plant owners had the area levelled by removing parts of the elevated soils in the north-east and raising large parts of the rest by up to several metres high with locally found granular material. In the late 1940s, geotechnical engineers anticipated significant settlements resulting from the addition of backfill over areas with thick silt layers and, therefore, allowed the soil to settle. However, their calculations were overly optimistic up to a factor of four.
Site considerations
As a result of backfill loading adding to the weight of the actual facility, the site area depressed significantly over the life of the plant. The south part of the plant, which is the oldest part, settled from
0.6 m (2 ft) along its western edge and up to 2 m
(6.5 ft) further east, with most of the settlement taking place before the mid-1980s. Besides deforming the buildings, settlements caused repeated misalignment of crane runways and also affected connections between various pieces of equipment. The plant continued operating, while constantly
re-aligning rails, adjusting equipment, and raising roofs.
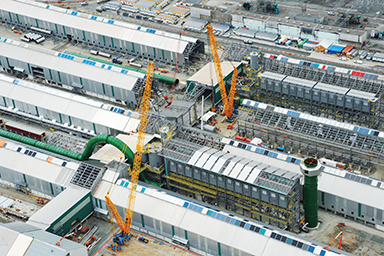
New site
Located between two streams at the north end of the plant, the site for the new plant was previously less affected by the settlements. To this day, the largest recorded settlements were up to about 0.45 m (1.5 ft). On the other hand, parts of the area were never developed.
Around 2009, when the last study was nearing completion, geotechnical engineers concluded most of the settlements had already taken place and building a new plant—with advanced equipment far more sensitive to settlements—was viable as long as major loads were not added over the compressible silts. As a result, structural engineers had to deal with both immediate settlements in the top granular layer and primary long-term plus secondary settlements in the silts.
Geotechnical engineers were mandated to provide full services for the project’s final stage and together with structural engineers, decided to solve the challenge in a way that would turn the highly load-sensitive situation into almost a normal site typically suitable for building.
One of the major hurdles to overcome was the near impossibility to use piles. In most areas, end-bearing piles could not reach the bedrock, which was too deep. Friction piles could only reach the compressible silts, causing the piles to settle together with the silts. Along with that challenge, any major backfilling was inconceivable as such overburden would add too much load and cause the thick silts to settle over long periods of time.
Another issue was the relatively high groundwater level, not far from the surface, with a sloping gradient through the relatively permeable upper granular layer. Therefore, the engineers were literally squeezed between potentially high settlements and the ground water level. With a couple of minor exceptions, area pre-loading was also discarded due to schedule limits, and the fact the existing operating plant could not have been pre-loaded before demolition. Pre-loading adjacent undeveloped areas was also impossible, since deep silt settlement would have dragged down existing operating buildings. One of the ways to mitigate settlements could have been lowering of the new buildings to compensate for the new loads by excavating and removing soil. However, in most cases, the high water table put an end to that possibility.
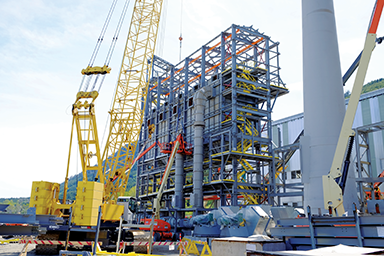
Building at the optimal level
As a result of these challenges, the engineering team decided the only way to build the plant was to do it differently from typical aluminum smelters. Rather than building the plant on one or two primary levels, every building would be built at an optimal level to minimize potential settlements while not compromising the process. This ensured connections between the buildings did not exceed the maximum slopes in the plant roads, and helped manage storm and surface drainage. The task was complicated by the fact the existing grade levels varied, mainly in the undeveloped area just outside the original smaller plant, and therefore could not be changed much.
The potline was placed at an optimal level with great difficulties and a limited margin of error. Additionally, the north third of the potline is located where it was possible to remove some soil, the central third is where the old potline was perpendicularly located, and the southern third is almost exactly where the original ground level was. Just south of the potline some looser soil was found; short-term preloading mitigated potential settlements under the row of future heavy rectifiers.
The building, with particularly sensitive equipment, was meant to be placed in the areas where piles could reach the bedrock. It turned out even there, many piles would have to go to depths of around 40 m (131 ft) and be rock-socketed due to many steep slopes in the rock and potential limited soil liquefaction during a major earthquake. In the end, the building was moved as much as possible into a thick layer of granular material not far from the northern stream.
One of the facilities had to be placed lower by about 2 m (6.5 ft) in a zone with a lower water table and due to a highly compressible layer of silt under the building. Unfortunately, a Franki piling system (i.e. pressure-injected footing) could not have been used under the paste plant at the south end after finding, during preliminary tests, dissolved methane gas in the ground water and some hard debris from an old sanitary fill, encountered a few metres down. The paste plant was finally placed on steel piles. The hard-tipped H-piles had to be driven up to 60 m (196 ft) deep to reach the bedrock.
Optimizing structures
While elevations were being optimized, another group of engineers worked on enhancing steel and concrete structures.
Kitimat is located in a moderate seismic zone at a sufficient distance from the severe zone around the Haida Gwaii (also known as the Queen Charlotte Islands). With the region’s high snow loads—typical roof design snow load is 5.2 kPa (108 psf)—higher than normal quantities of steel were estimated. Following several optimization attempts, it was decided typical roof slopes on the main potlines and some service buildings should be increased to a 30-degree angle, where important reduction of snow loads on slippery roofs could be used, and the required steel quantity ended up as the smallest.
Several taller operating buildings coming from overseas manufacturers were assembled in their shops or shipyards and shipped in complete modules to the plant’s terminal. Modules were then transported from the terminal to the site, lifted with cranes on previously poured foundations, stacked up, and installed.
Designing and assembling a large duct that would cross over the central passage with a single curve, represented a challenge since it could not be supported vertically by the building below. To solve the problem, a determinate structure was created by introducing three hinges—one on top, and one near each base. To eliminate thermal stresses and reduce the steel plate thickness, lateral support in transverse direction was provided near the top of the building below.
Conclusion
Maximizing concrete prefabrication helped the project team keep up with the predetermined schedule. With smaller pieces included, thousands of prefabricated elements will be installed once the plant is completed. Typically, precast elements in the potline and anode baking furnace (ABF) are installed with high precision—often within millimetres—to allow precise installation of equipment. Since serious differential settlements are not expected, installed equipment is less sensitive to future total potential settlement. This is mainly due to the fact the silts’ top is much deeper below the thick granular layer in this location, smoothening out the settlements like a raft.
With a multitude of unique challenges, brownfield construction can be difficult to say the least, especially in remote geographies such as in the case of the KMP project. For this project, the pour of the first hot metal is planned in the first half of 2015.
Jan Vrana, P.Eng., is a structural engineer at Bechtel Canada. He has extensive experience in design engineering and has provided engineering leadership and supervision to projects for aluminium smelter and associated facilities, along with residential and commercial construction, institutional, and infrastructure buildings. Prior to Vrana’s present position as a lead resident engineer on the Kitimat Smelter, he spent five years as a regional chief structural engineer and technical specialist for Bechtel’s Mining & Metals Montréal office. For more than 20 years, he was a part-time adjunct professor in the department of civil engineering at McGill University in Montréal. Vrana can be contacted at jvrana@bechtel.com.