The importance of specifying a metering faucet
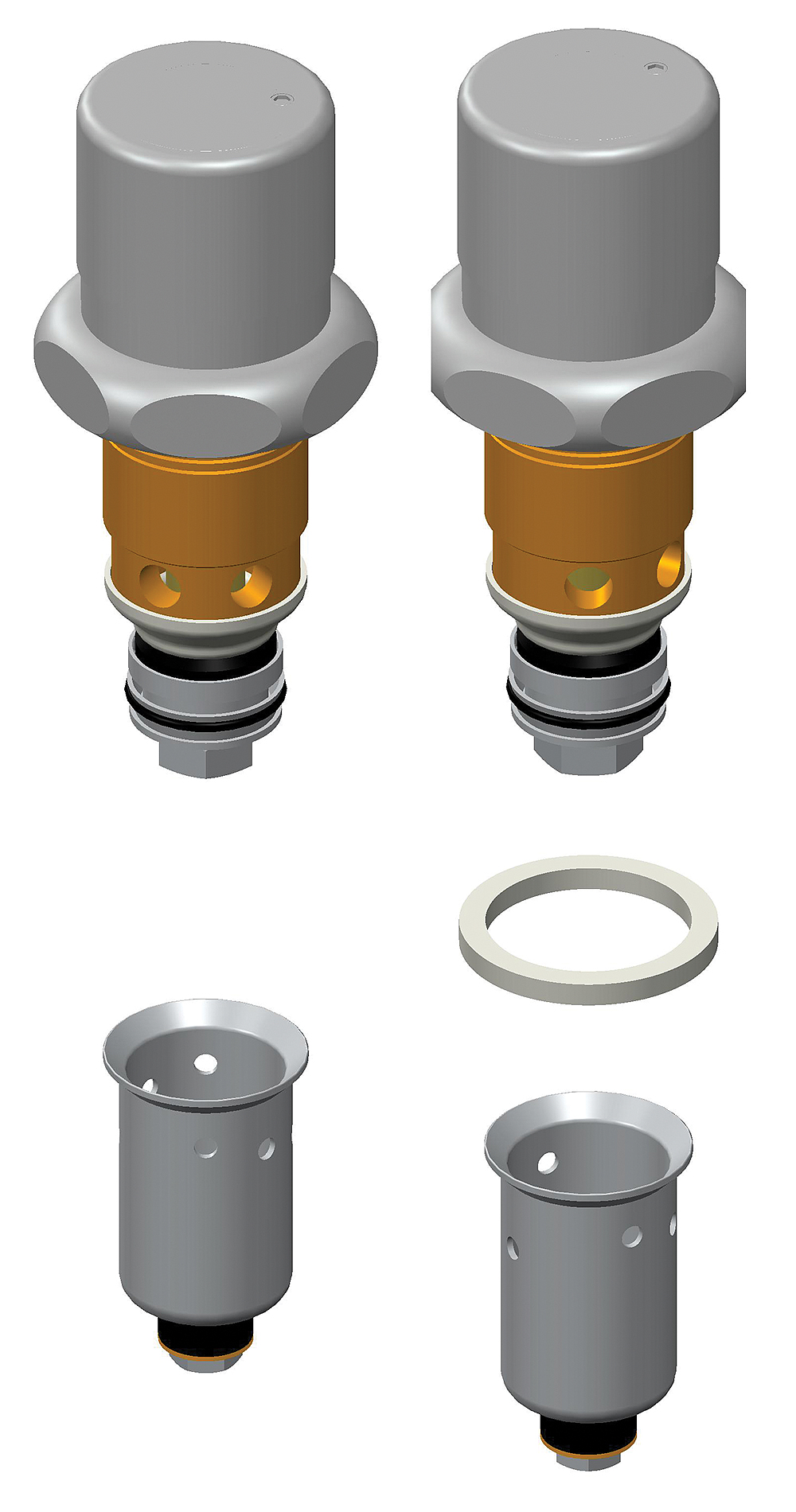
Metering up close
Metering faucets are an extraordinary piece of engineering, containing many features that have evolved to meet the considerations previously mentioned. Throughout this evolution, the improvements are not always obvious because they are within the faucet. A cartridge, for example, while the heart of any faucet, is especially innovative in metering fixtures. The cartridge regulates the flow of water (time), which the most important component affecting overall faucet performance. Unlike electronic models, or simple on/off handles, the metering faucet must be precise—cartridges had to be developed for maximizing performance, and also easy adjustments.
Metering faucets also can contain pre-installed, free-spinning supply hoses making installation easier. Many offer one-piece, chrome-plated, cast-spout bodies and vandal-proof components. Additionally, there are now many different types of cartridges used in metering faucets for specifiers to consider. Understanding their differences will help understand not only the metering itself, but also how the functionality has evolved to deliver proven performance.
Manual metering
The manual metering faucet is activated by pushing down on the top handle to begin the flow of water. The water will run for a set time, determined by the setting on the mechanical cartridge and the amount of water pressure present. Manual metering faucets are preset at the manufacturer, usually 12 seconds per cycle, and have the ability to be adjusted in the field.
The original manual metering device cycled water by changing the timing mechanism (or dashpot). The dashpot had a hole that allowed for precise control of the water that flowed through it. Adjusting it was a simple matter of regulating water flow through the porous washer’s compression over the hole. The cartridge had a spring
that is used to retract the valve, and water was thereby controlled through the washer’s compression. In other words, the more force compressed on the washer, the harder it was for the water to flow. Although the manufacturer sets the timing as a reference point, it can be changed, giving the metering faucet a layer of flexibility to meet various conditions.
Eventually, improvements were made using the same concept of moving water through a hole and a control pin where water bled through the orifice to control the tolerance. One change, for example, was the modular cartridge, which had a spring that made an actuator move up and down. Thus, placing a filter on the bottom of the cartridges protects the cartridge against line sediment, which increases life expectancy and reduces maintenance.
As the actuator moves up and down, control points allow water to bleed through, which in turn, is controlled by time adjustments. Depressing the handle, the cartridge closes on release or within a two- to 30-second cycle time.
Another change was an external timing nut for easy adjustment with no need for shutting off the water, or adding another filter screen to protect against contaminants.