The importance of flashing components
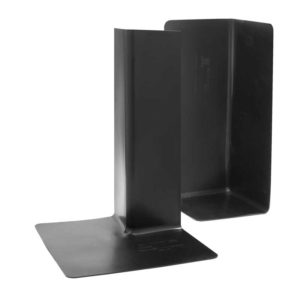
Materials
End dams typically are made out of synthetic rubber or stainless steel. The stainless steel ones are formed and soldered, and are a bit more difficult to trim. A pair of shears would be necessary to make the cut. Carborundum blades are not recommended for cutting stainless steel because they can leave residue, which could tarnish exposed brick or stonework post-installation due to the passage of moisture. Synthetic rubber end dams are injection-formed and require simple trimming with a knife to pre-fit the required dimensions. Depending on the membrane chosen for the project, bonding the end dam to the flashing can create additional issues. Many polymer-modified flashings require sealants or adhesives that bond to materials with a higher surface energy. An example of conflicting surface energy is when the marker ink does not stick to plastic—an incompatible sealant has similar adhesion problems with polymer-modified membranes.
A question asked sometimes is, “If you have run out of material and I think I used an incompatible sealant to bond my laps, what can be done?”
First, know exactly where to start and stop using the specified materials if a change needs to be made. This will help determine the location of a future problem and the repairs that would have to be undertaken. Second, let someone know what the daily high and low temperatures are along with the membrane being used on the project as well as if the substrate is clean and dry or cold and wet. All of this information gives the manufacturer a chance to help masons continue working until the specified materials can be delivered to the site. In most cases, the project will be better off if the contractor simply covers the work area with a tarp and keeps it clean and dry while working on another location until the required materials arrive.
If polyurethane or silicone is used under the drip edge and behind the term bar, a good bond on a dry substrate is likely. However, if it is wet, then one needs to wait. If a polyether sealant is employed in the same application, then it will work on the wet and dry substrate and behind the term bar, and there is a good chance to seal the laps if the sealant is matched to the flashing. Butyl sealant can help with these issues. It is compatible with ethylene propylene diene monomer (EPDM), polypropylene, polyurethane, polyvinyl chloride (PVC), thermoplastic polyolefin (TPO), and metal flashings, which covers the spectrum of available flashings. Many of the mastics used in the late 1990s and early 2000s will not be compatible with the polymer-modified flashing membranes available today. Compatibility should be investigated before use by contacting the technical department of the manufacturer.
Corner boots fall into the same economic considerations as end dams. As a contractor, the evaluation of cost is made by the time it takes to make them against the purchase cost and reliability of the product. Installation of the corners also make fitting the flashing membrane easier as it allows for terminations to be sealed on top of the corner boots, which, in turn, can save on the risk and the dollars.
Conclusion
It is important to understand changes typically come with uncertainties and a perceived increase in material cost. However, it is not the case always. As mentioned earlier, prefabricated components cost the same as pulling or folding flashings. It is not risky to try something new.
Prefabricated components enable installers with less training to flash a building like more experienced masons.
Flashing components are as important as the membrane is to the whole system when it comes to keeping the building dry.
Steven Fechino is the engineering and construction manager for Mortar Net Solutions. He provides engineering support services and product training. Fechino has a bachelor’s degree in civil engineering technology and two associate degrees in civil engineering and drafting and design specializing in building construction. He can be reached at sfechino@mortarnet.com.