The flexibility of fabric walls
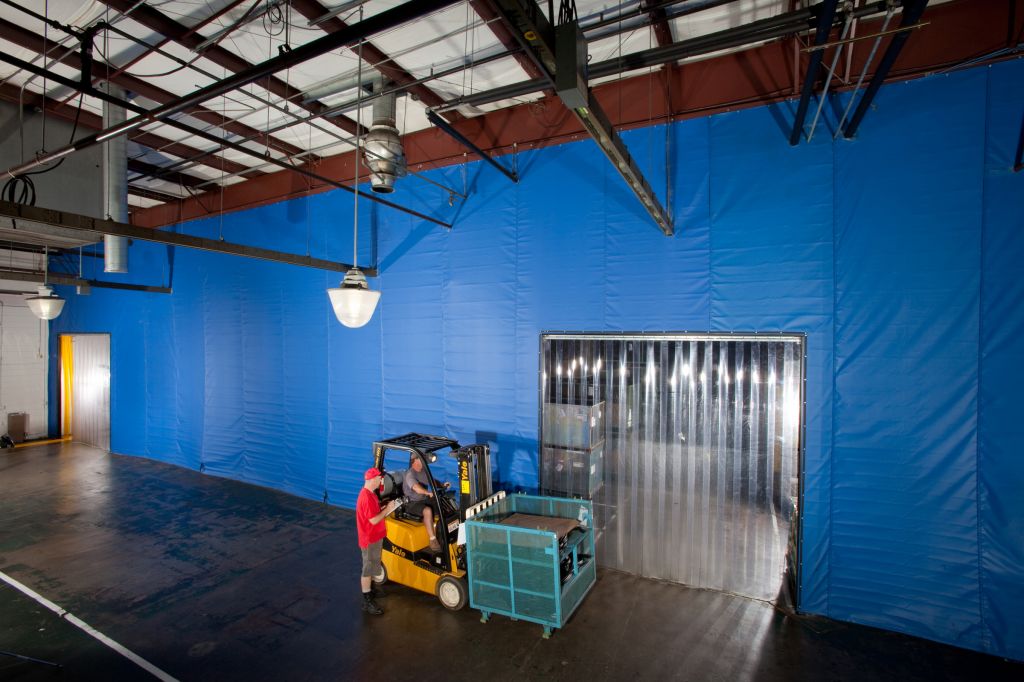
By Kyle Justice
Flexible fabric curtain walls are becoming increasingly popular for industrial projects and plant operations because they are omni-functional. These products can help manage physical space, improve productivity, save energy, recapture needed floor space, and control environmental conditions, such as temperature, odour, dust, or sound.
Yet another major reason why more and more plants in a wide range of industries are using reconfigurable fabric walls is because they can be installed relatively quickly and easily, making them an affordable alternative to permanent walls and insulated metal panel (IMP) systems. Further, these assemblies can be reconfigured if needed down the road.
Fabric curtain walls are built around the concept of simplicity. While each situation is different, the components of a basic stationary wall system are essentially the same on most projects. They include:
- industrial-grade fabric;
- steel mounting angles;
- poly-nailing flaps; and
- standard fasteners and hardware.
A basic wall can stretch from floor to ceiling, from one end of a permanent wall to another, or virtually any other configuration. When full height to the roof deck is not desired, threaded rod and angle or cable can be used to place the top of the wall at the desired elevation. Typically, the top of the fabric curtain wall is attached to ceiling joists. The weight of the curtains, while minimal to the roof structure, holds the bottom in place in most applications. Due to the light weight of these materials, engineering calculations typically are not needed, but can be provided on a case-by-case basis.
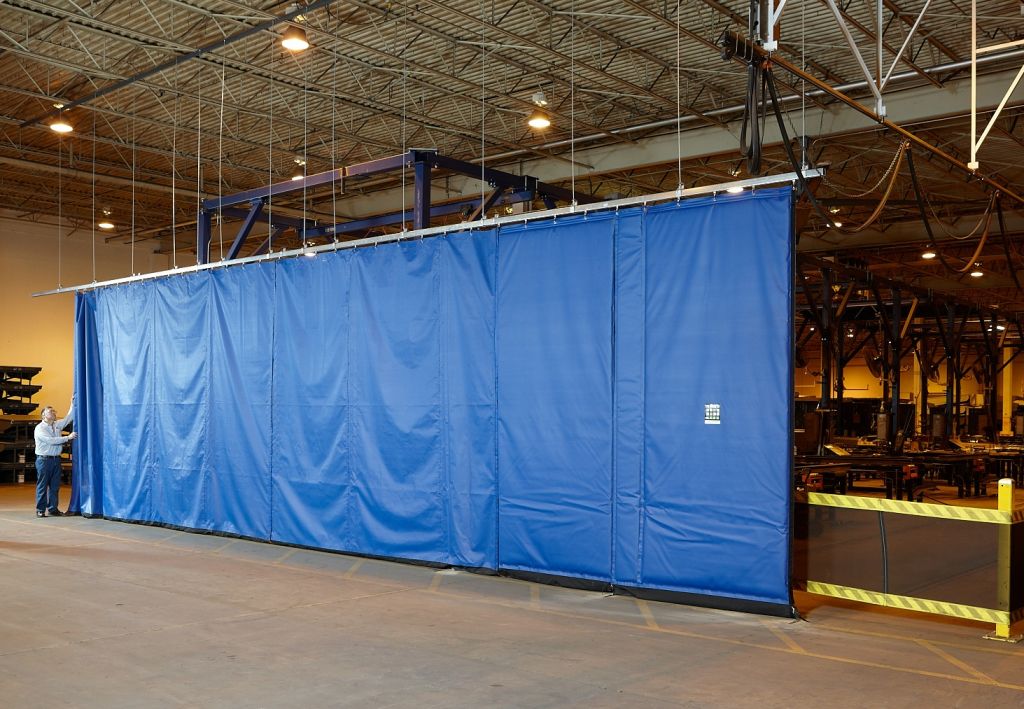
These engineered industrial fabric curtains can be insulated or non-insulated, and sliding or stationary, depending on the application. A typical wall is made of 1.5-m (5-ft) wide fabric panels interconnected with Velcro to span the width of a given space. Non-insulated walls are generally 1.6 mm (1/16 in.), while insulated systems are often 19 or 38 mm (3/4 or 1 ½ in.) thick, though 76-mm (3-in.) models are available. The standard fabric is 510-g (18-oz) flame-retardant vinyl, but heavier-weight fabrics can be specified for certain applications. These curtains are not limited by height and can be extended to the desired length.
The fabric is also designed to fit snugly around pipes or conduit, since the goal is often to control temperature, dust, or any number of other environmental conditions. Industrial doors of various types can be incorporated into walls with the proper framework.
The walls can be installed to temporarily zone or partition space, or be employed indefinitely to address long-term needs. They cannot be used as load-bearing walls, and should not to be confused with traditional-built walls (e.g. studs and drywall), IMP systems, or welding curtains. Additionally, the fabric coatings are fully cured and stabilized, eliminating any concerns with volatile organic compound (VOC) emissions or off-gassing once they have been installed.
Industrial ‘curtain wall’ applications
Fabric curtain walls can address situations when there is a need to put physical space to better use, or to make the facility footprint work better in terms of operational efficiencies or energy savings. They are also suitable for surrounding interior and open loading docks. Each application is unique to the specific building and floor plan and requires knowledge about the type of materials and systems that will achieve the desired goals.
Temperature separation
Fabric curtain walls can be used to divide cooler/freezer space, keep employees warm or cool in specified plant areas, and protect temperature-sensitive items or processes. Insulated curtain walls can provide a temperature delta of 8, 15, or 22 C (15, 35, or 40 F), with respective R-values of 3, 6, and 10. They are not used to construct the cold storage cooler or freezer box, but can be specified to subdivide them.
Heat/humidity control
Industrial fabric curtain walls can isolate heat-generating production processes for employee comfort, as well as effectively control humidity levels within a facility. Although they are not true vapour barriers, a quality installation can approach that level. (The Velcro connections are not airtight, but still slow the air-to-air exchange for temperature control.)
Flame-retardant curtains are available as Class A-rated for ASTM E84, Standard Test Method for Surface Burning Characteristics of Building Materials. (These kinds of curtains are not smoke curtains.)
Sound attenuation
Curtain walls are specified for reducing excessive noise levels, enclosing or isolating noisy equipment or operations, and partitioning areas for sound control. Typical noise reduction is between 22 and 27 decibels.1
Dust/odour/fume containment
Fabric curtain walls can keep dust off products and packaging, and out of machinery and production equipment. They can also be used to protect employee health and comfort, or prevent absorption of food or chemical odours into other products.
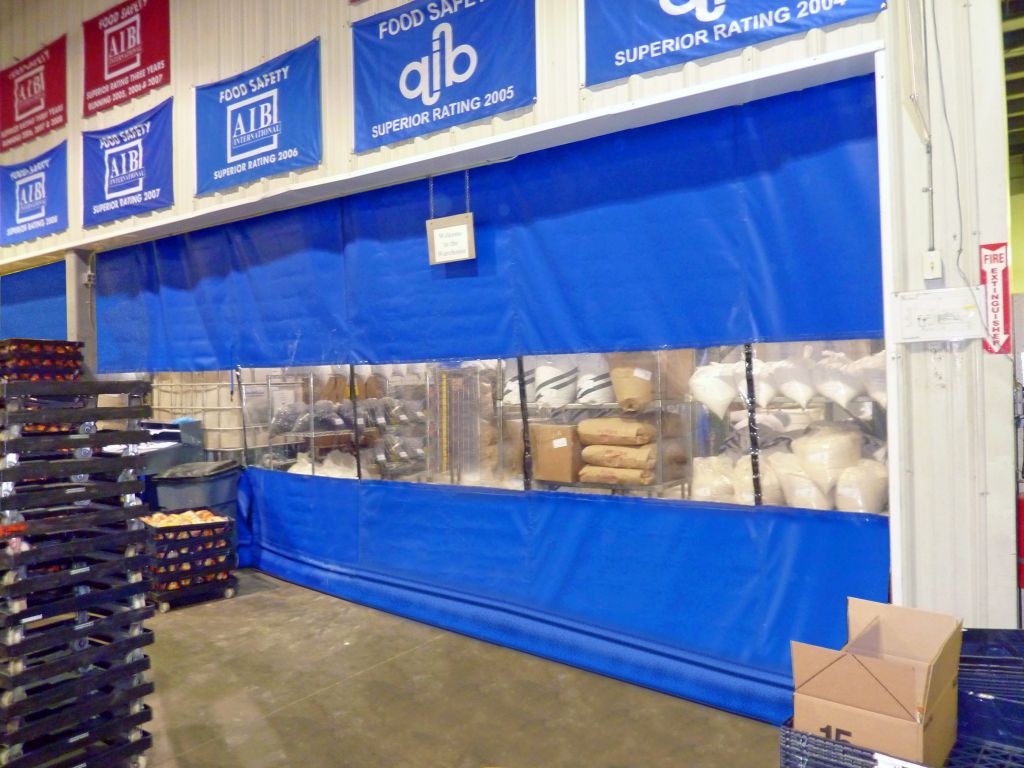
worker productivity by blocking out potential health hazards
like dust and fumes.
Wash-down
Fabric walls can isolate production lines for cleaning while continuing to operate other lines at peak capacity, enclose areas to minimize overspray when cleaning, and reduce drying times. They can also help lower potential for cross-contamination during routine production processes.
Installation methods
A plant maintenance crew, or anyone who is mechanically inclined, can install a basic wall system with relative ease. The method used to attach the fabric wall to ceiling joists varies based on the wall’s position relative to the joists.
When the joists run perpendicular to the fabric wall, a mounting angle is tack-welded or clamped to the bottom flange of the ceiling joists along the linear run of the fabric curtain wall to be installed. The top of the wall curtain is attached to the mounting angle using tech screws and fender washers approximately every 380 mm (15 in.).
A second mounting angle is also clamped or tack-welded to the top flange of the joist (at the roof deck) along the linear run of the flexible curtain wall. A smaller valance curtain is then screwed with washers into the mounting angle so it overlaps the top of the larger bottom curtain. The finished result is a full-height wall from floor to ceiling.
The installation is handled differently when the joists run parallel to the fabric wall. In this situation, a mounting angle is tack-welded or clamped along the top flange of the joists (at the roof deck) along the linear run of the curtain wall. The full curtain is then fastened with tech screws and fender washers approximately every 380 mm.
Whether the fabric wall runs perpendicular or parallel to the joists, the curtain easily attaches where it meets an existing building wall. A fabric-nailing flap or steel-mounting angle is used depending on the type of building wall. Tech screws or anchors are used to secure the polyester nailing flap to the permanent wall. The opposite end of the flap uses Velcro to attach to the curtain panel. Velcro corner connectors are also employed to form corner joints.
A fabric sweep is added to the bottom of the curtain to form a bottom seal. The sweep, which attaches to the curtain with Velcro, can be easily replaced if it is damaged or worn. The sweep typically includes additional height so it can be cut to shape, eliminating gaps due to any voids in the floor slab.
Wall installation 201
Installations involving doorways or obstructions are not difficult to manage. With doorways, some manufacturers provide a freestanding framework, which is mounted to the floor. The fabric curtain is attached to the framework of the doorway using plastic nailing strips.
Fitting the fabric wall around obstructions involves simple field cuts, which are then resealed with a special tape designed for the vinyl material. A common example is cutting around conduit pipes. To do so, a cut is made from the top or side of the curtain to the point where the obstruction travels through the fabric wall. There, a series of cuts are also made to form a star. The fabric is fitted around the obstruction and the cut is resealed with the specially designed tape, and then fastened to the mounting angle.
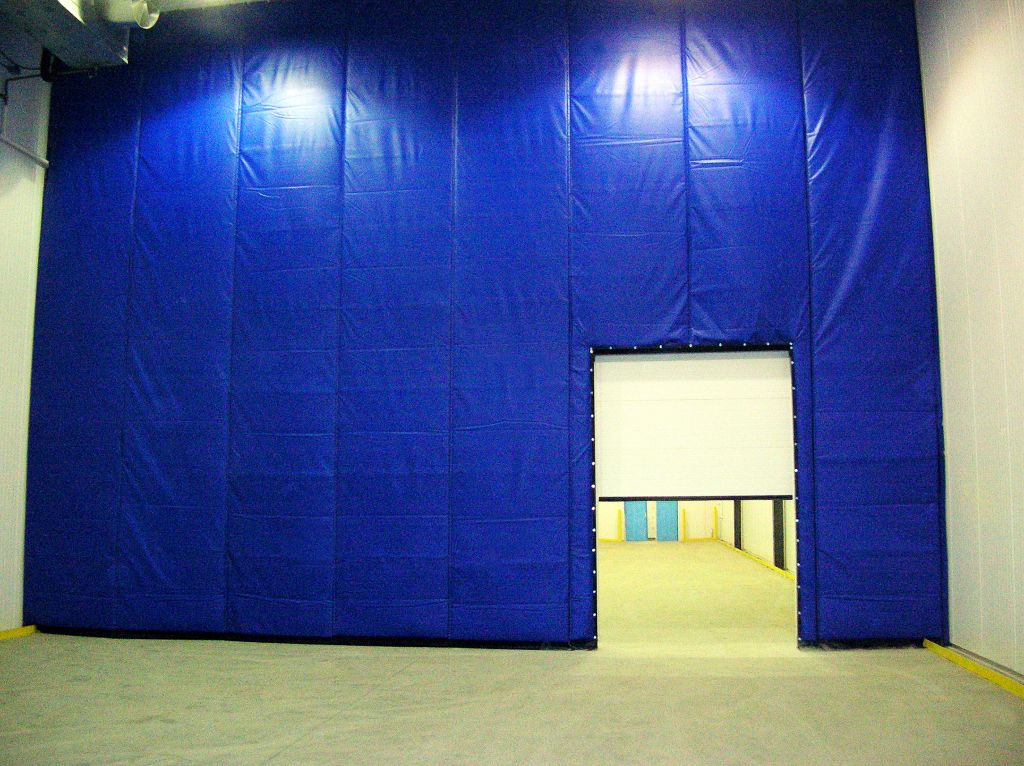
Fabric curtains can be easily adapted to accommodate high wind loads, including facilities with substantial negative or positive air pressure by using steel framing, stretchable wind retention cords, or by installing steel angle on the floor and attaching the bottom seal of the curtain to the angle.2 (High-wind-load situations may require framing or additional support.)
The walls can also be designed to fit virtually any existing space, which is where design expertise is often recommended. This is especially helpful for sliding walls, dock enclosures, and temperature-sensitive or refrigerated spaces. Regardless, the installation is essentially the same as a basic wall.
Material advantages with fabric walls
Fabric curtain walls offer numerous advantages over permanent walls and interior IMP systems. Knowing the advantages is important if it means the go-ahead for a project that ultimately contributes to the operation’s bottom line.
Easier to install
Fabric walls do not require concrete curbing or a steel guardrail to protect the base of the wall, simplifying installation. Additionally, there are no studs involved. Installers can work around racking and/or products, which means there is no need to remove and reinstall racking and/or products to complete the installation. Typically, fabric walls also do not require a permit, making the process even less complicated. (It is a good practice to always check first with regard to permits, however.)
Less costly
The savings can be considerable when it comes to specifying fabric assemblies instead of traditional walls or interior IMPs. There are fewer steps, no need to involve a carpentry crew; and no hard costs for concrete curbs, protective railings, studs, and metal framework on a basic wall.
If a fabric wall is damaged, repair costs are low because the wall can be easily patched or replaced with minimal lead-time. (Again, there is no need to replace or fix studs, drywall, or metal framework.) Lower costs are also a major factor when a wall needs to be removed, reconfigured, or moved to another location. It can be done without demolition-related expenses.
Time-savers
Simplification results in faster installation. Additionally, lead-times are reduced because there are fewer people in the loop and permitting is not necessarily a requirement. Delays are minimized because some walls can be installed with off-the-shelf hardware. The simplicity involved in repair and/or replacement also saves time. The same is true when the wall needs to be taken down, repositioned in the same general area, or used elsewhere.
Conclusion
Adaptability, flexibility, and ease of installation, as well as time and cost savings make flexible fabric curtain walls an excellent alternative to traditional non-load bearing wall construction methods. The only caveat is fabric curtain walls are an investment like anything else—good practice involves working with a reputable manufacturer of fabric walls, so their design and applications expertise can help the project team get it right from the beginning.
Notes
1 For more on acoustical implications of these products, see the article, “Another Kind of Curtain Wall: Controlling Facility Noise with Industrial Fabrics,” by Chuck Ashelin in the March 2013 issue of The Construction Specifier. (back to top)
2 Typical wind velocity (positive or negative air pressures) within buildings have not been an issue for Velcro connections or fabric. For exterior or perimeter applications, manufacturers can add suitable steel structure within the curtain system or mount the curtains to the steel structure if warranted. (back to top)
Kyle Justice is the vice-president of sales for Zoneworks. He has been in the warehousing and manufacturing industries for more than 15 years, and has extensive knowledge of product flow, storage, and manufacturing processes across a broad spectrum of industry. Justice can be contacted at kjustice@zoneworks.com.