The evolution of glazing in Vancouver
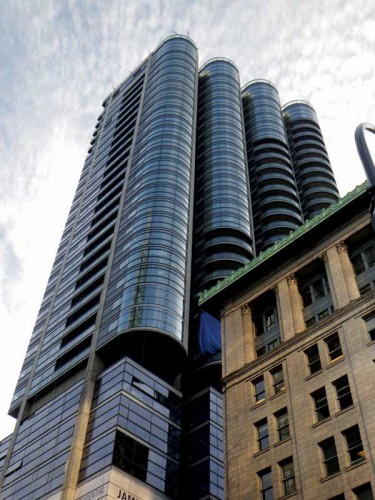
By Catherine Lemieux, P.Eng., LEED AP
When looking at its skyline, it is no wonder why Vancouver is known as the “City of Glass.” Glass high-rise buildings, each one taller than the next, have been the architectural vision developed over many years (Figure 1). In fact, the relationship between West Coast architecture and glazing systems is symbiotic; their evolution would not have been possible without one another. This article discusses the last 20 years of glazing progression in the Lower Mainland market. (The author would like to thank Mark Lawton and Sophie Mercier for their insight and experience relating to the evolution of glazing across Canada).
Punch windows
Back in the 1980s, punch windows were the traditional glazing choice for buildings across Canada. The units were rebate-mounted into the rough openings, meaning fasteners were driven through the sides of the frame into the wall structure. Effort was required to ensure the windows were level and plumb.
The Vancouver area was facing a growth in the construction sector, leading to a bigger, but less experienced, workforce. This was driving the need to develop an easier means for installing the windows within the rough openings. It was then the nailing flange started to be incorporated into window frame manufacturing. The idea was the installer would simply place the frame into the rough opening until the nailing flange stopped it from going in further, and then fasteners were driven through the face of the flange into the wall (Figure 2). This practice became somewhat unique to Canada’s West Coast. In fact, the standards of the time––such as the 1990 edition of Canadian Standards Association (CSA) A440-M90, Windows––did not even recognize flange-mounted windows.
With the evolution of aluminum glazing systems, the nailing flange has gradually disappeared. Many of today’s vinyl windows, however, can still be found with flanges––some are still monolithic to the vinyl extrusion while others add the flanges in a chase afterward. The latter style cannot rely on the flange as being a means for structural attachment––it is purely an installation guide.
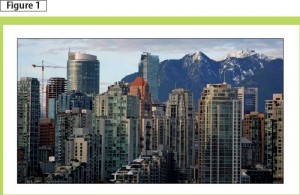
Photo © Dan Gronross. Photo courtesy Morrison Hershfield
The leaky condo crisis
With residential construction still on the rise in the 1990s, the design trend favoured larger vision areas in the walls. The typical aluminum window frame consisted of the same extrusion used at the head, sill, and jambs, joined together at mitre corners. In terms of water shedding, the extrusions themselves were not sloped to the outside. Limited means for drainage was provided within the frame.
At the inside face of the sill, an interior track was incorporated into the frame to collect condensation, which could be drained back to the outside through weep holes. During wind-driven rain, the differential pressure across the system would often result in the height of the water within the track to be more than a shallow track could handle, leading to water spilling over to the inside. The insulated glass (IG) units were glazed from the outside with glazing stops having no provision for weatherseals, thus inviting more water into the system than desired. The combination of these features meant this window style was at high risk of suffering from water leakage.
While the window construction was an issue in itself, another critical factor was there was no real effort placed on waterproofing of the rough openings. Leakage through the window frame often resulted in water getting into the wall cavity below and, consequently, deterioration of the finishes and structural elements.
From a thermal performance perspective, there was a false sense that, given Vancouver’s milder climate, installing non-thermally broken windows was an acceptable practice. The 1990 edition of CSA A440-M90, Section 8.1 states:
except for storm windows, all metal windows covered by this Standard shall incorporate a thermal break to prevent through-metal conductivity.
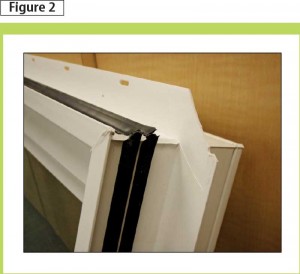
Images courtesy Morrison Hershfield
While other governing bodies across Canada were mandating windows follow this standard, Section 9.7.2.2 of the 1992 British Columbia Building Code (BCBC) clearly stated “windows need not incorporate a thermal break.” Since installing windows with poor thermal performance was allowed by this clause, condensation became a common issue in many buildings of this era.
Aside from condensation, the earlier thermal breaks were prone to shrinkage over time, such that they opened up at the corners of the frames. This additional source of water infiltration, combined with inadequate waterproofing of the rough openings, compounded the problem. In fact, non-thermally broken frames performed better from a watertightness perspective at the mitre corners compared to the first versions of the thermally broken windows (Figure 3).
Punch windows became larger and slimmer in profile until they were installed from slab to slab. The framing elements were quite slim compared to today’s systems. It has been debated by some that the aluminum systems of the early 1990s may have been used in configurations beyond their structural capacities. The windows were designed with limited engineering and, as such, the systems were bridging increasingly larger spans and were becoming much more flexible. In turn, the windows’ primary seals were being challenged as the flexible frames moved beyond today’s tolerances with wind loading, building settlement, and thermal expansion and contraction.
Failures of the seals and the misalignment of mitre joints within the framing––especially when looking at aluminum frames with no second line of defence against moisture (particularly subsill flashings) or in adequate water management capabilities––were a characteristic source of water penetration into the buildings.
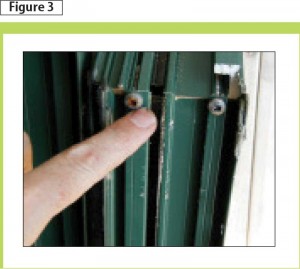
All these factors contributed in part to the West Coast’s ‘leaky condo crisis,’ and the severity of the repercussions can still be felt today as building envelope rehabilitations of structures from that era are still a reality. However, the crisis did lead to significant improvements to glazing systems. Local window manufacturing companies became more prominent in the market and started including features such as sills sloped to drain and stops with weatherseals. Joinery at the mitre corners remained a weak point in the aluminum windows, which meant vinyl windows with welded corners became a more popular choice for low-rise residential buildings. Engineers and installers developed the technique of installing subsill flashings at the rough openings to help manage moisture, even if the mitre corners leaked. The 1998 BCBC also evolved and started mandating thermal breaks within aluminum frames to minimize the risk of condensation.
Window-wall systems
Window walls came to the West Coast from Eastern Canada, and consisted of thermally broken aluminum frames that included a slab bypass section. This was essentially the same frame configuration as the vision area, but with the framing inboard of the thermal break simply cut off so it fit in front of the slab edge. This technology became very popular for residential towers, and local manufacturers started copying the idea.
Earlier versions of the system did see their fair share of failures, but over time they were refined. This is especially true when considering the move to moisture management design started as a face-sealed style, meaning the window’s outer surface was intended as the primary moisture barrier and did not include any provision to deal with moisture getting past the outer surface. The face-sealed design moved toward a hybrid approach that included a poor means of drainage, to finally the rainscreen approach the industry now knows. The rainscreen design incorporated redundancy by having two separate lines of defence against moisture and efficient drainage.