The evolution of fluid-applied membranes
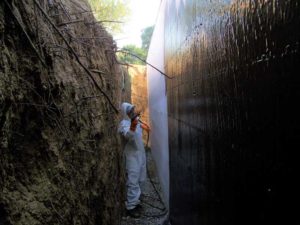
Bituminous membranes
In the early 1900s, cold fluid-applied membranes were developed primarily for maintaining roadways and for dust mitigation. Cold-applied membranes include cutbacks, cold-process, and emulsions, which each refer to slight variations in the chemistry.
An asphalt cutback is simply heavy-grade asphalt thinned with lighter grade petroleum solvent to provide a higher viscosity and easier workability. Solvent-based cutbacks are rarely used today, and the term cutback has essentially vanished from product literature. These products are still available but can be limited by code requirements due to their flammability, odour, and higher VOC content. These limitations often outweigh the benefits of cooler weather application and styrene butadiene styrene (SBS) membrane compatibility.
An asphalt emulsion replaces most of the solvent found in an asphalt cutback with water. Both cutbacks and emulsions contain asphalt cement, a finely ground or milled asphalt mixed with an appropriate solvent. Emulsions suspend the asphalt in the material through chemical emulsifiers and surfactants, and naturally contain very low VOC content. Standard asphalt emulsions remain viable for light-duty waterproofing in areas of low hydrostatic head pressure, commonly referred to as ‘dampproofing.’ Polymer or rubber-modified asphaltic emulsions provide improved waterproofing protection against hydrostatic head pressure. These products find use primarily due to their significantly lower cost when compared to higher performing membranes. Applications requiring greater flexibility, improved performance, or faster setting times might be better served by alternate product types.
Modern bituminous asphalt is distilled from crude oil, oil sands, and well sources. It was first synthesized with other polymers into useable rubberized asphalt in the early 1950s. This early ‘polymer-modified’ asphalt contained styrene butadiene rubber (SBR) and found immediate use in the production of rapidly growing roadway networks at that time. In the late 1960s, scientific development led to the invention of SBS-rubberized asphalt with markedly higher levels of durability. The SBS asphalt formulation ages better, provides elastomeric qualities and strength while significantly improving abrasion resistance compared to its SBR predecessor.
During the early 1960s, a tire manufacturer commercially marketed SBR and later SBS-rubberized asphalt. Approximately 10 years later, a sheet version of SBS asphalt was developed into modified asphalt roofing, or ‘mod-bit.’ This new chemistry includes all the benefits of hot fluid-applied SBS in a polyester or glass-reinforced, factory-controlled thickness sheet product.
Hot-applied SBS membranes are unrestricted by low temperature site conditions and set immediately as fully adhered, continuous membrane. In its nearly 60-year track record, hot-applied SBS membranes have one of the lowest installation costs for a waterproofing membrane. They provide robust protection for plaza decks, steam tunnels, vegetated roofing, and parking garage deck applications. Conversely, respirable emissions and unpleasant odours from the melted asphalt should be considered when working in or near densely populated areas. Additionally, the material is nearly 204 C (400 F) when installed. The high temperatures can be dangerous even to an experienced installer.
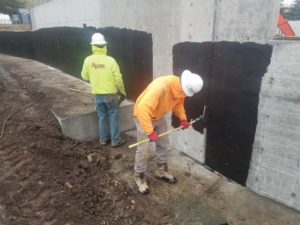
Polymeric materials
In the latter half of the 20th century, the industry expanded toward new material possibilities, including polyurethanes. Polyurethanes, however, represent a broad category. Specifying the correct polyurethane requires precise terminology and detailed information regarding the product’s physical property requirements. Subcategories include two-component, single-component, hybridized, unhybridized, modified, and unmodified. Advantages to polyurethane products in general include better elongation and flexibility. These products also adhere well to a wide variety of substrates. In restoration or maintenance applications, older surfaces may have unknown coatings or pre-existing adhesives. A polyurethane allows the contractor a greater chance of success despite any unknowns over other, more substrate-specific products. At a molecular level, urethanes form a spring-like structure, allowing for strength and flexibility. This molecular spring also recovers well, which creates high tensile strength, elongation, hardness, and flexibility even at extreme high and low temperatures.
Unfortunately, compatibility between polyurethanes and other waterproofing materials can be tricky. Polyurethanes are often modified with asphalt. The transfer of oils or plasticizers between adjacent asphaltic materials can negatively impact adhesion and create other compatibility challenges. Many injection grouting materials contain polyurethane technology. If builders use injection grouting to repair a failing waterproofing system, they must determine compatibility with the existing waterproofing system before installation. Likewise, they should always confirm compatibility with transitions, detailing membranes, and protection course prior to installation. Testing information is widely available for polyurethane waterproofing, but modified or partial terminology within the testing criteria can create confusion when comparing products. Due to the range of various chemistries within this larger group, it can be difficult to establish true ‘equals.’
Two-component polyurethane membranes were introduced in the early 1980s. These solvent-free products cure through a chemical or ‘crosslinking’ reaction. Two-components often have no added solvents, lower VOC levels than subsequent solvent-based, single-component products, less odour, and negligible flammability risk. While they provided a more consistent cure time than the air/moisture-cure single-components, the inconvenience of field mixing led to the development of single-component products later in the decade.