The effect of temperature on insulation performance
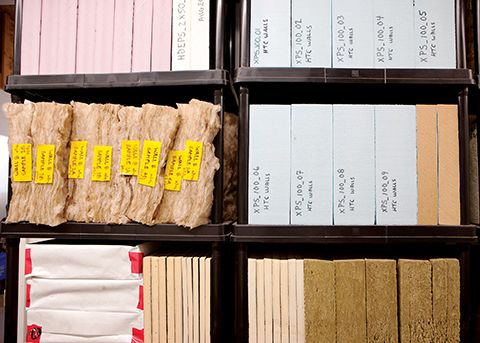
by Christopher Schumacher, M.A.Sc.
On the surface, R-value is a simple thing. In fact, it has become the standard metric of thermal performance precisely because it is easy to explain and understand. Most insulation materials have ‘label R-values’ stamped on their faces (or at least displayed in large print on the packaging), but these values do not tell the whole story of how insulation performs in service. Some complicating factors—such as thermal bridging—have become fairly well-known. However, in order to meet current needs for energy-efficient, durable, comfortable, and cost-effective buildings, it is critical to continuously improve the industry’s understanding and handling of insulated assemblies.
R-value is a measure of thermal resistance for materials. In other words, it denotes how much heat is prevented from flowing through a layer of material at a given thickness. In North America, R-value is most commonly given in imperial units, where one R = 1 (sf·F·hr)/Btu, and a 50-mm (2-in.) thick layer of insulation might be R-10. In Canada, RSI units are also used; one RSI = 1 (m2·K)/W and RSI = R / 5.678, meaning the 50-mm thick layer of insulation would be RSI-1.76. Regardless of the units used, the effectiveness of thermal resistance depends on a number of factors.
For example, temperature-dependent R-value is a phenomenon relatively unknown outside of the world of researchers and academics. Temperature dependency refers to changes in the R-value of insulation over a range of temperatures. For example, a 25-mm (1-in.) thick board of extruded polystyrene insulation (XPS) might have a label R-value of RSI-0.88 (R-5), but its actual performance may be closer to RSI-0.97 (R-5.5) under cold-climate winter conditions, or as low as RSI-0.72 (R-4.1) under hot-climate summer conditions. The label R-value is not incorrect; it refers to performance under a specific set of standard test conditions and does not necessarily reflect how a material performs on a building.
Temperature dependency matters because the insulation in real-world buildings often experiences temperatures differing significantly from standard test conditions. In fact, the standard test condition temperatures are almost never seen in a typical building. Research has characterized how R-values change with temperature by measuring materials at different mean temperatures and using various temperature ranges.
This article describes an ongoing research project at Building Science Laboratories (BSL) that has included a variety of insulation materials over several years. In most cases, the insulation performed a little better than expected when the mean temperature was lower (simulating cold outdoor conditions), and a little worse when it was higher (simulating warm outdoor conditions). Further, the relationship between R-value and temperature is nearly linear. Where this pattern occurs, R-values are predictable and temperature can be easily accounted for. However, some unusual patterns have also been found. Polyisocyanurate (polyiso) insulation provides a useful example of how unusual temperature dependency patterns can be identified and then accounted for in modelling and design.
Determining R-values
Before getting into the details of BSL’s research, it is important to understand the origins of the R-value and how it is typically measured. The R-value was proposed by Everett Shuman in the 1940s as an easy-to-compare, repeatable measure of insulation performance. Prior to that, thermal performance was expressed in terms of conductance or the ability for materials to conduct heat. Materials provide better performance when they have lower thermal conductance. Industry decision-makers felt consumers would be confused by the concept ‘smaller is better.’ When thermal performance is expressed in terms of R-value or thermal resistance, higher numbers represent better performance.
The R-value went on to become the de facto metric across North America, familiar to both consumers and professionals. It has helped many designers and consumers make more energy-efficient choices, but its importance in influencing purchase decisions has also led to some unscrupulous marketing claims. In the aftermath of the 1970s oil crisis in the United States, fraudulent R-value claims became so widespread the United States Congress passed a consumer-protection law in response, the “Federal R-Value Rule” (16 Code of Federal Regulations [CFR] Part 460, “Trade Regulation Rule Concerning the Labeling and Advertising of Home Insulation”).