The diversity of stone wool insulation
Ryan Martin
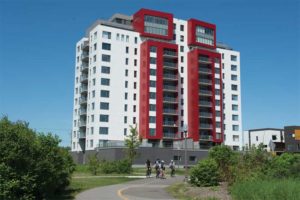
Achieving greater energy efficiency has become the order of the day for designers and builders across North America, due, in part, to changing building codes and fueled by a growing contingent of forward-thinking builders, architects, and energy consultants. Education and awareness have moved the needle for higher performance building envelopes, prompting greater consideration of insulation levels, R-value, airtightness, vapour diffusion, condensation control, and more. As a result, greater thought is now invested in material selection and whole system performance.
One solution that stands out in today’s energy-conscious environment is stone wool rigid insulation board. The material has emerged as an advantageous multitasking solution that is gaining traction among architects, designers, builders, and contractors.
The reasoning for the specification of stone wool rigid insulation boards is as multifaceted as the range of applications for their use. These insulation boards contribute to key project goals from energy efficiency to moisture management, fire protection, and sound control, as well as building resilience and sustainability, among others. As such, stone wool rigid insulation boards have been integrated into forward-thinking commercial and residential projects for a number of years, with proven performance.
Continuous exterior insulation
Stone wool rigid board is a popular choice for continuous exterior insulation, given its stable R-value per inch and its contribution to a building’s safety, comfort, and durability. Many contractors also prefer the product for this application given its ease of handling and installation, whether installations occur onsite or in controlled environments, such as in prefabricated panels. The high density of the material allows it to be easily cut without tearing. This allows for tight installation around obstructions in walls.
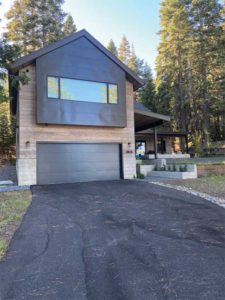
Energy codes are starting to require continuous exterior insulation on all commercial buildings, and it makes sense, since buildings account for approximately 40 per cent of all energy consumption. Continuous insulation is required by the National Building Code of Canada (NBC), the National Energy Code for Buildings (NECB), and is an effective solution for compliance with the National Residential Code (NRC). It is a smart practice for builders who aim to construct beyond code, helping to reduce heat transfer and thermal bridging and creating a more comfortable indoor environment for occupants.
Such was the case with the continuous stone wool rigid board insulation incorporated into the exterior envelope of the Origine Tall Wood condominium tower on the banks of the Saint-Charles river in Québec City, Qué.—a location known for extremely cold winters, and, thanks to its riverfront location, moist, heavy air. Origine is a 13-storey, 92-unit residential tower built by Québec-based Nordic Structures and is one of the tallest wood buildings in North America.
Built on a concrete podium, it boasts 12 storeys of solid wood construction, predominantly glue-laminated timber (posts and columns) and cross-laminated timber (CLT). Given that the structure comprises wood, the rigid insulation boards offered critical fire protection. Stone wool insulation can resist fire up to 1177 C (2150 F), without the need for chemical flame retardants. In addition to fire protection and energy efficiency, stone wool was specified based on the vapour permeance, dimensional stability, acoustical properties, and ultraviolet (UV) resistance of the insulating material. In open joint cladding or even while installing, materials are exposed to UV. They do not go from the protective covering to immediately behind cladding, so there needs to be a level of UV resistance to maintain the product while exposed. Foam plastics and other polymer-based materials are not inherently UV resistant. Therefore, foam-face polyisocyanurate (ISO) is available in the market—the foil blocks the UV. However, the exposed edges of the material could still be damaged. With its riverfront location and Québec’s harsh climate, the drainage capabilities and water-resistant properties of stone wool proved advantageous. The insulation also complemented Origine’s sustainability profile since the insulation products are made of sustainable raw materials and recycled content. The Origine project has achieved Leadership in Energy and Environmental Design-New Construction (LEED)-NC Silver certification.
The use of stone wool rigid insulation board for continuous exterior insulation in residential home construction is also on the rise. One recent build in Austin, Tex., is a perfect case in point.
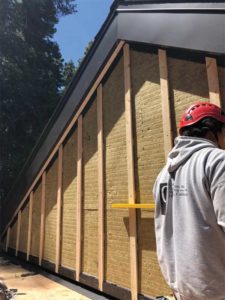
Custom home builder and building science proponent, Matt Risinger, is known for going above and beyond building code requirements with his projects, focusing on the craftsmanship of each build, and adhering to construction and design best practices. While the Austin house falls into Zone 2 on the climate map, the methods used in this build would be sufficient up to Climate Zone 5—covering all but the far north. Despite being more than 270 km (170 mi) from the Gulf Coast, this home was built to withstand a coastal environment, including extreme weather events like hurricanes and tropical storms, as well as the heightened humidity levels that come with building in the hot/humid southern United States.
The house was framed using laminated veneer lumber (LVL) 2×6 studs—an engineered wood stud that is typically only used in headers and beams. This method provided double the strength of traditional 2×6 framing. The prevalence of wood in the structure meant that there was an even greater need to control moisture. Risinger and his team used a vapour-permeable, airtight peel and stick house wrap, and stone wool insulation boards to provide continuous insulation on the exterior. This rigid insulation board is a vapour-open insulating solution, ensuring the house will dry to the outside. The team used 50-mm (2-in.) stone wool insulation boards to achieve an effective R-value of R8 (RSI Value 25.4 mm @ 24 C – 0.72 m2K/W).
Using the Home Energy Rating System (HERS) index—the North American industry standard for measuring a home’s efficiency—this house achieved a score of 48; roughly 50 per cent more efficient than the standard code-built home. It is also the nationally recognized system for inspecting and calculating a home’s energy performance. The lower the score, the more energy efficient the home is deemed to be.
Regarding his choice to use stone wool insulation for the continuous exterior insulation, Risinger noted, “the exterior insulation will lead to a lifetime of energy savings, better durability for the structure—since we do not have to risk any negative impacts inside the house caused by condensation—and we are providing the added benefit of fire resistance. While this project in particular was not built in a location at a high risk of fire, it still boasts stone wool insulation that will protect against flame spread and minimize the effects of smoke—both important safety features in the event of a fire.”
Basement wall applications
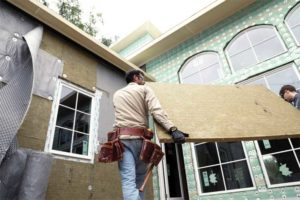
Builders aiming for better performance are looking to newer, more innovative building techniques and solutions and, from an insulation standpoint, are increasingly choosing products that can meet energy requirements, while also contributing to other performance objectives, such as moisture management and/or fire resilience. The building envelope is a primary focus, and not just above grade. Better below-grade solutions are also being implemented, and again, it is an area where stone wool rigid insulation boards stand out. Basements have long been a weak spot in building envelope performance due to moisture issues, and the problem is the foundation wall system, specifically in cold climates that require an interior vapour retarder. Many new-builds experience moisture condensation on the polyethylene (poly) vapour barrier, causing water to pool on the basement floor and creating conditions that are favourable to mould growth. This is because the wall cannot not dry to the outside in below-grade applications due to damp-proofing or to the inside due to the poly.
Homebuilder, Empire Communities, sought to apply a more advanced and improved basement wall system to its Riverland Community Empire Discovery Home pilot project in Breslau, Ont. The pilot project was not only an exercise in sustainability and better construction techniques, but also an experiment in research and development that will have a large impact on how Empire will build homes in the future.
To build a better basement wall system, a great deal of research and field testing was conducted to learn more about the challenges of controlling vapour diffusion in a basement wall assembly. The goal of the study was to illustrate a solution to the moisture-related basement wall problems using standard construction materials and practices. The solution consisted of a hybrid insulation (interior insulation) wall system incorporating extruded polystyrene (XPS) installed against the concrete foundation wall, covered by rigid stone wool insulation boards (and poly) acting as both a thermal insulation and a thermal barrier. The stone wool rigid boards were chosen for their moisture repellency and fire performance characteristics, as well as their high drying potential and ability to resist mould and mildew, while contributing to thermal performance.
Data has been collected from one hybrid home to document the construction methods and technology incorporated into the homes. Temperature, moisture content, and relative humidity sensors were installed in the wall system above and below grade to measure performance and analyze the moisture-related risks. The results indicate the hybrid insulation solution reduces potential for condensation at the poly layer, as well as provides superior thermal performance in comparison to typical basement wall blanket insulation installation.
The Empire Discovery Homes in Breslau were given a HERS score of 38, awarding Empire with the Canadian Production Builder lowest score in the RESNET and CRESNET Cross-border Challenge, a competition between U.S. and Canadian builders.
What these projects all have in common is performance, and that is the top reason for the continued and increasing use of stone wool rigid boards in projects across the United States and Canada. Building industry professionals have come to trust these boards to contribute positively to project goals.
Certifications and listings
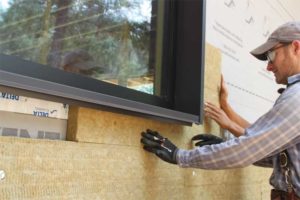
Building professionals should look for stone wool rigid boards that have earned CCMC certification for thermal insulation in buildings based on testing in accordance with the Underwriters Laboratories (CAN/ULC) S702, Standard for Mineral Fibre Thermal Insulation in Buildings.
WUI zone fire protection
Wildland urban interface (WUI) codes in North America set out the specific requirements for certain parts of a home/structure and property to ensure it is WUI compliant, in an effort to mitigate wildfire risk. Building products used to achieve compliance or as part of a compliant assembly must be listed as approved products in the WUI Building Materials Listing Program or have undergone testing to demonstrate the product/assembly meets WUI requirements. Components covered by WUI code include exterior components, such as roofs, walls and siding, decks, windows, doors, soffits and vents, and other details considered to be vulnerable ignition points.
In California, the State Fire Marshall’s Building Materials Listing (BML) Program certifies products based on an evaluation of test results that include an analysis of required product performance and reliability features. All testing is completed with a State Fire Marshall (SFM) accredited laboratory. The SFM listing service provides building authorities, architectural and engineering communities, contractors, and the fire service with a reliable and readily available source of information on building products for fire-first applications.
The Sagan Design Group wanted to break from a status quo WUI solution to meet requirements for the exterior wall assembly in one of its custom-built, high-performance homes. Generally, those who do not wish to use a rated assembly must instead use 16 mm (5/8 in.) Type X gypsum sheathing under the exterior cladding to act as an ignition-resistant barrier in order to achieve WUI code compliance or have an alternative assembly/solution tested. The Sagan Design Group sought to use a continuous layer of exterior stone wool semi-rigid board insulation instead of Type X gypsum. Its team was met with the challenge of achieving the 2016 California Energy Code Standards, approximately 20 to 30 per cent more stringent than the 2013 edition, while also meeting R-value targets and satisfying WUI requirements.

In making its case to local code officials, Sagan Design Group and the insulation manufacturer demonstrated the continuous exterior stone wool sheathing board provided the noncombustible, ignition-resistant performance benefits equivalent to Type X gypsum, while also delivering a wall system that reaches necessary thermal resistance and contributes to the strict U-value rating. The stone wool continuous insulation proved further advantageous, allowing for a wide variety of cladding options, a benefit that would sit well with homeowners who often insist on specific materials to achieve a certain esthetic. Stone wool insulation boards are not limited to a certain type of cladding materials and using fasteners to install it can help handle the weight of most cladding options. The stone wool boards were also favoured due to their vapour permeability and high drying potential, contributing to a ‘breathable’ wall assembly with good moisture management.
In the end, local officials approved what might end up being a trailblazing solution. The stone wool rigid board insulation became the first and only insulation of its kind to receive certification in California with the State Fire Marshall’s BML Program, which includes its use as continuous exterior insulation in commercial and residential building applications throughout WUI areas.
Given the direction of energy codes and the need to satisfy both energy and code requirements in wildlife urban interface areas, it seems inevitable the residential built environment may be on the cusp of change, driven largely by code compliance. It is undeniable that how we build is, in fact, changing. What that means is designers and builders will need to look to building products that do more. They will need to use their experience to continue to do what has always driven the built community forward: thinking beyond the status quo. Better solutions should pay off for homeowners as well, with more durable, resilient buildings that require less energy and less maintenance and/or remediation down the road.
Conclusion
As a versatile solution, stone wool rigid boards are available in a variety of densities and thicknesses. They offer a diverse range of performance benefits. Their use continues to climb, in tandem with tightening code requirements and the overall move by the building community toward more efficient, sustainable, safe, and resilient solutions that improve occupant comfort, provide savings, and contribute to more durable buildings with smaller environmental footprints.
Ryan Martin is the product manager for exterior wall, roofing, and core solutions, Rockwool. He is passionate about developing new and innovative solutions for stone wool insulation and supporting his clients.