The detrimental effects of UV on barriers
How UV breakdown occurs
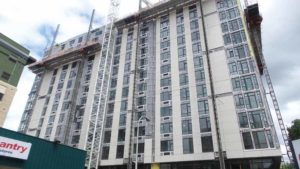
WRBs can get damaged; it is a fact of construction. Most physical damage happening to barriers prior to or during installation can be seen. Holes, cracks, and tears can have a significant impact on a WRB’s effectiveness. These are usually caught and repaired onsite because they are visible. Unfortunately, this is not the case with UV damage. This impact happens at the molecular level, leaving building professionals unaware of and unprepared to deal with the problem.
UV exposure occurs from the time of installation until the WRB is covered with the exterior insulation or cladding. During this period, UV radiation causes the WRB to oxidize, age, and deteriorate. The rate and amount of damage at a molecular level are determined by many factors, including additives such as:
- colour pigments;
- antioxidants;
- UV stabilizers; and
- flame retardants.
How the WRB is manufactured will also have an impact on the degree of breakdown. For instance, manufacturing processes including thermal or shear stresses can initiate early degradation of the WRB. The material experiences heat from the friction that is part of the production process. Higher temperatures cause the polymer molecular chain to break down and react with one another to change the properties of the polymer.
This became common knowledge in the science community as early as 1899 when a Swedish chemist performed experiments that correlated chemical reaction rate constants with temperature. From this research, the Arrhenius Equation theory indicates a 10 C (18 F) rise in temperature will reduce the lifespan by half. Oxidation also has a significant impact on the aging and breakdown of WRBs, which can occur as a result of exposure to heat, certain chemicals, or UV light.1 This means over-ambitious production methods leading to excessive heat and stress can kick off the degradation process well before the material lands on a jobsite. For polymers, more heat equals rapid aging. So, while a WRB may not physically break down during the allowed exposure time, it is important to understand what happens to the product once it is no longer visible.
Uncovering the unseen damage
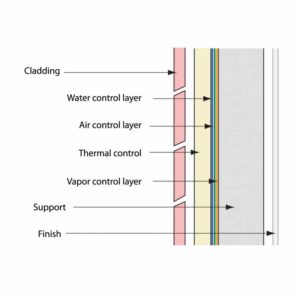
To better understand what happens behind closed walls, an Sageos (a division of the CTT Group) carried out a series of third-party, accelerated aging tests on vapour permeable, self-adhered WRBs.2 The research spanned eight months from April to November 2013.
Standard UV exposure tests (such as those required by the International Code Council [ICC] Acceptance Criteria [AC] 38, Water-resistive Barriers, or the Underwriters Laboratories of Canada [CAN/ULC] S741, Standard for Air Barrier Materials—Specifications) use the WRB product samples and expose them to light from UV sun lamps for 10 hours per day for a total of 21 days. In theory, these tests are designed to mimic the conditions naturally occurring in a construction site. These relatively short-term tests do not represent a typical exposure time for WRBs, as some are exposed for nearly 180 days.
As part of the research study, new samples were tested for strength, elongation, and water resistance before being exposed to the UV light to establish a baseline. Those specific tests were chosen to represent the two key, long-term performance criteria one would expect from a membrane in a wall system:
- resistance to water penetration (Hydrostatic Head Tester per the American Association of Textile Chemists and Colorists [AATC] 127-2008, Water Resistance: Hydrostatic Pressure Test); and
- durability (ASTM D5035-11, Standard Test Method for Breaking Force and Elongation of Textile Fabrics [Strip Method]).
The samples were retested after 500 hours of UV exposure and again after 1000 hours of UV exposure, using Cycle 3 of ASTM G155, Standard Practice for Operating Xenon Arc Light Apparatus for Exposure of Non-Metallic Materials.
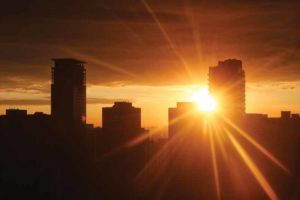
Photo © Getty Images
It is important to note natural UV exposure varies widely according to geographic location, site conditions, and weather. The 500- and 1000-hour intervals were chosen for all samples to provide consistent and equal exposure for accurate comparison.
Totally, five common self-adhering WRBs were tested, with the acceptable or ‘pass’ criteria set at a minimum of 75 per cent retention of original (‘as new’) test results. All saw a reduction in performance with respect to strength, elongation, and water resistance. The strength of some barriers declined by 80 per cent after being fully exposed for 1000 hours. Even at 500 hours, two of the five WRBs experienced a reduction in strength of 40 per cent or more.
Elongation results and measures of durability were also seen to decline for most products after the full 1000-hour exposure, with four of the five experiencing a reduction of more than 50 per cent. The most significant results, however, came from testing the water resistance of the WRBs. Two products saw a 90 per cent decline in water resistance after just 500 hours of exposure and continued to decline during the remaining exposure hours.
Overall, test results made it clear WRB damage does occur from extended UV exposure during installation periods and the effects can be severe. All WRBs would perform better with less exposure to UV radiation on the jobsite. The sooner the WRB is covered after installation, the less degradation and aging can be expected, and the better its long-term performance within the building envelope. With the right planning and approach, steps can be taken to get ahead of the problem and minimize the impact.