The demand for recreational roof decks
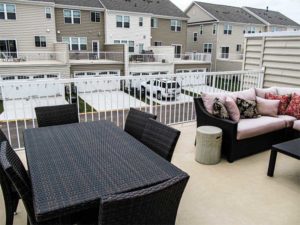
Whether embedded with fabric or fibreglass, centre-reinforced vinyl has some disadvantages because of their composition being divided by layers. Due to constant environmental exposure, vinyl membranes are manufactured with additives such as UV and mildew inhibitors to extend the material’s lifespan. These active properties are only built-in through the top layer. Vinyl options that are fabric reinforced at the back allow the UV and mildew inhibitors to run through the full thickness of the top layer, providing a little more longevity of those components compared to centre-reinforced vinyl, which does not allow those components to run through the full thickness of the material. The bottom layer of centre-reinforced vinyl is typically made up of ‘fillers’.
An additional benefit of fabric-backed vinyl is in the product’s ability to be formed around bends and 90-degree corners. This is a huge advantage at the installation stage to allow for waterproofing detailing where the membrane is integrated into the building envelope. In contrast, vinyl-backed membranes have difficulty accommodating those 90-degree turns and rely on the strength of adhesives to prevent tenting or lifting at corners.
Regardless of the type of vinyl selected, all can perform very well if installed by a qualified applicator. Each will have their particular nuances for adhesion and weldability, but a skilled applicator can work with them for successful waterproof performance.
Product evaluation and selection for roof deck membranes
Not all vinyl is created equal. A few key indicators must be reviewed to determine the performance reliability of a walkable PVC roofing membrane. They include quality of the product and its warranty, reliability of the manufacturer, suitability for the application, and the skills of the installing contractors.
One of the easiest ways to assess the manufacturing quality is to determine it is under a third-party quality control program. The product should have easily accessible and identifiable evaluations to show it meets building code requirements for its intended use as a roofing membrane and a pedestrian traffic surface. Be aware of common, easily disguised bait-and-switch tactic where some manufacturers will only evaluate product A, but then use the same assessment for products B, C, and D.
Take a look at the warranty terms. A glance at the years of coverage can sometimes be quite deceiving once you dive into the exclusions and actual protection afforded by those terms. Sometimes warranty coverage is for the product only and can be prorated by date of purchase, reducing protection for each year of use. Other warranties cover the material and labour, should the membrane warranty need to be applied. In either case, it can be convenient to use the same manufacturer and/or contractor for roof deck waterproofing and guardrails to specify a single source for warranty.
Also consider the longevity and history of the manufacturer. While many people first look at the length of the product warranty, it helps to be confident the company will be around to honour the terms. If the manufacturer has been around two or three times the length of its warranty terms, one can be more confident they will be there to honour their performance warranty.
PVC membranes are a reliable method of waterproofing, when installed correctly. The most common occurrences of failures in PVC membrane systems are related to workmanship. It is advisable to question the installation company about the waterproofing membrane being used. Some vinyl manufacturers insist on factory-trained applicators. Other vinyl membrane options are available from the local hardware store and are accessible to untrained contractors.
Specifying waterproofing membranes that are available only through trained installers helps to ensure proven waterproof detailing techniques are used. This can be the difference between a successful and failed waterproofing job at common points of vulnerability such as door thresholds and deck-to-wall transitions. Additionally, manufacturer-trained contractors typically use manufacturer-tested adhesives so the risks of compatibility issues are reduced. When it comes to membrane roof decking, it is relevant to ask if the contractor installing the waterproofing membrane is also fixing the railings. When using membrane waterproofing, it is preferable to have a railing installer who understands waterproofing and does not compromise the membrane.
Conclusion
Whether your projects would benefit more from non-exposed or exposed roof deck membrane systems, this method of roof deck waterproofing is advantageous to multi-residential projects.
Jennifer Ogilvie Brackett is general manager of Duradek. Brackett grew up in the vinyl membrane waterproofing business, as her father and uncle own Duradek. In her current role, Brackett leads day-to-day operations and addresses compliance to all changes to the industry and its regulations throughout North America. Brackett can be reached at jennifer@duradek.com.
Kim Smallwood is marketing co-ordinator for Duradek. After more than 20 years in marketing and copywriting, Smallwood joined Duradek in 2011. Since then, she has developed a knowledge base specific to flat roof deck waterproofing providing marketing collateral, articles, and continuing education material in the specialty niche of polyvinyl chloride (PVC) waterproof membranes. Smallwood can be reached at kim@duradek.com.