The demand for recreational roof decks
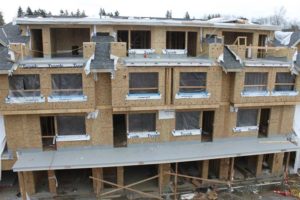
On a pedestrian roof deck, single-layer membrane roofing can be employed with an additional walking surface on top or as an exposed system if the membrane is also a walkable surface.
Dive into single-layer membrane roofs
Known technically as elastomeric or plastomeric roof membranes, single-layer membrane systems are often the roof of choice in commercial construction. As mentioned, there are various types of single-layer roof membranes such as:
- neoprene (polychloroprene);
- EPDM;
- PVC;
- chlorinated polyethylene and chlorosulfonated polyethylene sheets; and
- polymer-modified bitumens.
Membrane roofs can be partially loose laid and held down with river rock, fully adhered, or mechanically fastened. EPDM and neoprene roof seams are adhered with adhesive while PVC roof seams are heat or solvent welded. Heat-welding PVC roof seams is a more reliable method of joining the material to make a watertight seal, as, over time, adhesive and solvent seals will suffer degradation from ultraviolet (UV) exposure, and fail under expansion/contraction stress.
While EPDM and loose-laid systems are effective as a flat roof membrane, they are unsuitable as a pedestrian roof deck surface on their own. They require an additional traffic-bearing surface. However, some single-layer roof membranes can serve both purposes.
Characteristics of PVC membrane roofing
Membrane roof covering systems are tested to meet various performance criteria. Minimum requirements of product performance include wind resistance and physical properties such as accelerated weathering, breaking strength, impact resistance, seam strength, and fire rating.
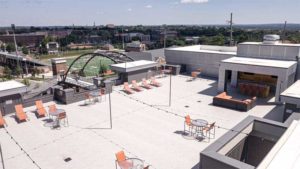
The degree of importance or relevance for each criterion can depend on the type of single-layer membrane roof. For example, in loose-laid systems, the breaking strength is more important than elongation, but with fully adhered systems the elongation or elasticity is more important to ensure the membrane can move with the substrate as it expands and contracts with changing temperature.
Unique needs of single-ply membranes for leisure roof decks
In addition to all of the roofing requirements mentioned above, a single-ply membrane used for a leisure roof deck intended to have foot traffic (beyond service use) has an additional set of requirements. These types of roof decks either must have an additional wear surface added on top of them (non-exposed roof deck system) or they must be evaluated as a deck membrane suitable for exposure to light pedestrian traffic (exposed or unprotected roof deck system), meaning they can handle traffic loads generated by residential occupancies.
Single-ply membranes must qualify as both a pedestrian deck and fire-rated roof covering, per Section 3.1.15.1, “Roof Covering Classification,” of the 2015 edition of the National Building Code (NBC) to be used as a deck over habitable spaces. Traffic membranes without a fire-rating classification do not qualify for roofing applications, and materials not meeting pedestrian traffic criteria like slip-resistance and other surface characters cannot be used as a traffic membrane.
PVC membranes for non-exposed vs. exposed roof deck systems
Two types of walkable roof decks—protected roof membrane assemblies and exposed roof membrane assemblies—utilize PVC membranes.
Non-exposed roof deck membrane assemblies
A non-exposed roof deck membrane assembly consists of a flat roof product (typically a single-ply membrane) with a separate pedestrian traffic surface applied overtop. Non-exposed roof membrane assemblies were first used in Russia in the 1950s and consisted of BUR membrane, a 100-mm (4-in.) layer of paraffin treated fly ash, 13-mm (½-in.) sand drainage layer, and concrete paving stones. Today’s PRM assemblies can include wood decking, concrete pavers, bonded tile, or a poured concrete topping.
While a non-exposed roof membrane assembly is suitable for heavy traffic and provides protection from mechanical damage, many of these assemblies pose a risk to the underlying structure or require significant upkeep. For example:
- wood decking on sleepers need a great deal of maintenance to keep up their appearance and could be a fire risk;
- bonded tile requires grout maintenance and has a high risk of surface cracking with moisture and temperature fluctuations; and
- a poured concrete topping is very heavy, requires additional structural considerations to support the weight, and is susceptible to environmental damage.