The challenges of winter roofing
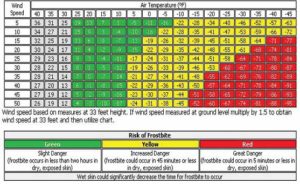
Image courtesy Environment Canada
The human factor
It is cold, wet, and slippery on the roof. During the cold months, light summer clothing is replaced with dreaded “winter weight.” For roofing crews, this means long underwear, heavy sweaters, winter jackets, double gloves, wool hats, heavy wool socks, and more. This can represent an additional 13.6 kg (30 lb) of clothing, significantly slowing movement around the roof.
Irrespective of how well the crew is dressed, the cold plays a significant role in roofing as workers may face the risk of frostbite to fingers, toes, noses, and earlobes, as well as hypothermia, when working in extreme temperatures. According to the Canadian Center for Occupational Health and Safety (CCOHS), the risk of moderate frostbite can occur between a wind chill of –10 and –27 C (14 and –16.6 F). Figure 1 illustrates the exposure risk as it relates to ambient temperature and wind.
In the preparation of the contract documents, consideration should be given to the question of whether the crews can use the owner’s facility for warm breaks and storage or whether the contractor has to provide onsite heated storage containers.
Working over the winter months will also have an impact on crews’ overall productivity and on the project schedule. In these authors’ experience, depending on the type of roof and rooftop equipment, production can decrease by 20 per cent or, in some instances, more. This can be attributed to the need for additional site/deck preparation, temporary heating, storage, and additional material handling, as well as the weather. Additionally, there is only so much daylight available in the winter. During the summer, crews can have up to six additional working hours while the sun is out (Figure 2). The winter days are shorter and depending on where the project is located, it may start to get dark as early as 4:00 p.m. This is especially true once the clocks are turned back to standard time.
Schedule (design/tender and construction)
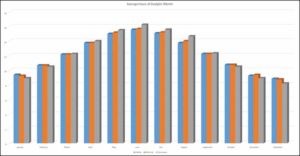
Image courtesy Timebie.com
Contractors typically cannot start a project right away, and a properly designed and detailed new roof system is of the utmost importance. A key underlying factor in the preparation of a reroofing project is the development of the tender and design documents. During this process, the designer works closely with the owner to determine the best roof design for the building while meeting the owner’s requirements and project budget. For example, owners may restrict use of asphalt-based products or mechanical fasteners due to conduits or services on the underside of the deck. They may also have personal biases against specific assemblies and manufacturers they do not wish to use. The design professional must navigate these factors in the preparation of the design. Depending on the client’s review and approval process, this phase of the project could take as long as eight to 10 weeks to complete.
Once the design is ready, the project must be tendered and awarded. The typical tender period varies based on the client’s process. For private clients, it can be as short as three to four weeks (two weeks to tender and one to two to award a contract). For others, it can take much longer. Public clients, for example, have regimented tendering and award processes, which can take up the full 60- to 90-day period of irrevocability (i.e. the amount of time the bids remain open) before the acceptance of the bid by purchasing, council, or similar. This is in addition to the two- to four-week tender period.
Once awarded, contractors must schedule this work within their production schedules. If a contract is awarded late in the construction season, it may take anywhere from four to six weeks for contractor mobilization to occur. As winter comes, contractors will also likely have other existing project commitments that are also weather dependent. Depending on available forces, this can further defer the start on a new site.
The speed of construction varies based on elements such as location, access, obstructions, services, and roof assembly type. For new construction, roofing crews can move relatively quickly, as they do not have any removals to contend with. However, on reroofing operations, crews are only able to remove as much of an area as they can make watertight. Again depending on the aforementioned factors, a crew of six may only be able to remove and replace an average of 15 squares a day where one square equals 9.3 m2 (100 sf). Therefore, from the time the request is made to design a new roof, it may take approximately 19 to 24 weeks from the start of the project (i.e. design) to completion.
In these authors’ experience, if the project does not need to be rushed, better pricing can be obtained by designing the work in the fall and early winter and tendering at the beginning of the year as contractors line up projects for the upcoming construction season. This is usually the right decision for quality, schedule, cost, and roof system flexibility.
Conclusion
The intent of this article is not to dissuade design/construction professionals from doing a roofing project over the winter. However, one must be aware of the additional challenges, schedule implications, and costs. It can be done, and these authors’ firm has been involved in many successful roofing projects carried out over the winter. Similarly, the team has also been in situations where, in consultation with the client and contractor, work has stopped until weather conditions improve to ensure the final product is not compromised. This is not an ideal situation, as it leaves the owner with a partially completed building. However, if the team, working together with the owner, determines the risks are too great, then the right decision may be to hold off on roofing until warmer weather arrives.
Ted Katsoris is a practice lead in the Building Science Group of Building Specialty Services at Morrison Hershfield’s Markham, Ont., office. Since joining Morrison Hershfield in 2004, Katsoris has overseen more than 800 projects. He brings more than 30 years of combined contracting and consulting experience to any project he undertakes. Katsoris also has extensive experience in the fields of building science and building envelope repair/rehabilitation, as well as contract administration. He can be reached via e-mail at tkatsoris@morrisonhershfield.com.
Derrick Moore is a principal and senior building science consultant for the Building Specialty Services Group at Morrison Hershfield. Moore project manages and is actively involved as a building science consultant on a wide variety of building envelope assessment and restoration projects. E-mail dmoore@morrisonhershfield.com for more.