The challenges of winter roofing
Roof assembly limitations
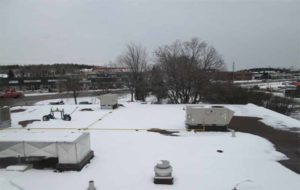
A roof assembly can consist of many different components, including but not limited to the vapour barrier, insulation, cover and overlay boards, membrane, and surfacing/ultraviolet (UV) protection. In order to achieve good results, all these components must be properly installed.
Assemblies can be put together using various methods and techniques. For example, vapour barriers can be installed loose-laid or by using hot asphalt, cold-applied adhesives, or self-adhering membranes. Similarly, the insulation can be installed using mechanical fasteners or glues or mopped in place with hot asphalt. Mechanical fastening is not inherently temperature sensitive, but the sealing of membrane terminations and laps may be difficult to complete. There are also situations in which electrical conduits are secured to the underside of the steel deck, where mechanical fastening may pose a risk of puncturing conduits.
Finally, the membranes can be glued over the coverboards or insulation, mopped with hot asphalt, mechanically fastened, or (assuming the appropriate noncombustible substrates exist) torched in place.
The designer/contractor and the owner need to understand the limitations of various assemblies—especially the materials comprising them—in the weather conditions anticipated during installation. For instance, chemical adhesives for insulation layers and some self-adhering membranes have strict limitations on installation temperature. The use of hot asphalt is generally considered one of the most versatile options available when it comes to the installation of a roofing assembly in cold conditions. However, like all systems, this has limitations. For one, hot asphalt roofing systems require available, clear ground area for kettle setup, as the kettle generally cannot be placed on the roof. Their use is further limited to the height the liquid asphalt can be pumped or shuttled to the roof. This can pose a challenge when working in a built-up environment (e.g. city core) or on very tall buildings.
Compounding these limitations is the asphalt’s rate of cooling as it is transferred from the kettle to the roof. Low temperatures cool asphalt rapidly and crews have to work very quickly to apply it before it drops below its required application temperatures. The contractor may try to overheat the asphalt at the kettle to combat this, but if the asphalt’s temperature is raised beyond the recommended level, the quality of the asphalt will be compromised (reducing the service life of the roof) and the risk of kettle fires will increase. Moreover, asphalt has a strong odour, which may be objected to by the building users.
Cold-applied adhesives have the benefits of requiring limited storage space, offering easy handling, and being relatively odour-free. However, some cold adhesives take longer to install and cure compared to hot systems. Also, cold systems have strict manufacturer limitations on allowable temperature range before performance and manufacturers’ warranties are threatened. Many adhesives have storage and application temperatures above 4 to 5 C (39 to 41 F). Although installation temperature requirements vary from one manufacturer to another, there are few adhesives that can be used for below-freezing conditions, which may require special equipment to facilitate installation. The manufacturer should always be consulted for installation requirements, particularly when using products in cold-weather applications.
Some projects may require more environmentally friendly options low in volatile organic compounds (VOCs). However, being water-based/moisture-cured, these adhesives typically have more stringent temperature limitations (above 5 C) for application and cure periods.
As with adhesives, self-adhering membranes have temperature limits with respect to storage and installation. While some are restricted to a minimum installation temperature of 5 to 10 C (41 to 50 F), winter-grade self-adhering membranes may be installed at temperatures as low as –5 C (23 F). In theory, this sounds great, but what happens when the daily high is –7 C (19 F)? Should the team push to install the cold-weather membrane anyway? If the membrane is installed at –7 C (19 F), what about when the temperatures drop to –9 C (16 F)?
Manufacturers have strict protocols pertaining to the storage and installation temperatures (substrate, product, and ambient air temperatures, during and after) for their respective products and may require adhesives and membranes to be stored indoors or within heated/insulated containers (typically located onsite).
Pushing beyond temperature installation limits will happen, particularly when one considers schedule (work must be completed by a given time), onset of weather (the push to install the before the cold and snow really sets in), and the tried and true (when the team has pushed to those temperature levels before).
Many membranes need to be laid out in advance to properly relax before installation, and when membranes are colder, they become stiffer. Smooth-surfaced membranes become dangerously slippery when wet or icy, a factor that must be considered for worker health and safety. Single-ply membranes may also be more prone to damage from shovelling snow.