The building envelope: A driver for energy retrofits
Constructability
For exterior insulation, standard attachment strategies such as continuous girts, or clip and rail systems, are usually the easiest to install. They do not require new training for contractors, and there is a perceived lower risk of failure. More modern attachment strategies, such as thermally broken clip systems or direct fastening, while gaining traction, may require additional structural analysis and contractor training. Other site considerations are also necessary such as proximity to other buildings, accessibility to the site from occupants (if applicable), and the potential for pedestrian disturbance and increased safety measured in more dense areas.
It is also important to note a rainscreen over-cladding system using stone wool insulation can use various substrates, providing versatility and design freedom for architects and designers. Depending on the cladding type and weight, the overall desired insulation performance, and thickness, they can be accommodated with either thermally broken intermittent clip and girt systems or directly fastened through the stone wool insulation. Likewise, over-cladding solutions using stone wool insulation provide versatility in design and cladding options along with additional fire resistance. Non-combustible stone wool insulation has a flame spread and smoke development index of zero. It does not trigger assembly testing, such as ULC S134, the Standard Method of Fire Test of Exterior Wall Assemblies, even near other buildings, such as in dense metropolitan markets.
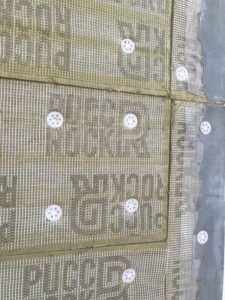
Interior wall insulation
Thermal efficiency
Interior insulation strategies can either include direct-fastening insulation, adding insulation between wood or steel studs, or a combination. However, interior insulation strategies do not mitigate large thermal bridges such as floor slabs, and often increases the thermal bridge and potential impacts. To account for these large thermal bridges, consider floor and roof insulation around the walls’ perimeter, although these are not as effective as an exterior insulation solution. When working on the enclosure’s interior side, ensuring continuity of the materials and their transitions becomes more complex due to the intersections with the interior floors, walls, etc.
Durability
Interior retrofits are often a solution for buildings with limited lot lines or where the exterior esthetic requires preservation for historical reasoning or client requests. However, an interior retrofit comes with additional performance and durability considerations due to the insulation’s location and the potential for interstitial condensation. In these cases, airtightness is crucial to reducing the transfer of moist air through the assembly. Even with an interior retrofit strategy, exterior work still may be required; for example, ensuring there are appropriate overhangs and drip edges to limit water exposure, fixing the existing cladding if applicable, or updating windows and doors.
Constructability
Typically, an interior retrofit can be considered a more straightforward installation than exterior retrofits. The additional insulation weight is carried by the internal floor structure and held in place with non-structural elements, prioritizing structural weight as a safety concern. However, interior retrofits will have a level of occupant disturbance. If residents live in the building, there may be associated costs to ensure their health and safety.
Considerations for masonry walls
Masonry walls present unique challenges. Existing masonry buildings are often a target for interior retrofits due to façade preservation requirements. Historically, masonry walls vary in thickness, consisting of multiple wythes (layers) of brick that range in quality—the exterior wythes will be of higher quality than the interior wythes. Masonry walls are heavy and porous, allowing them to store moisture. Since older masonry walls often do not have insulation, the wall’s energy transfer causes them to dry inefficiently. Therefore, adding interior insulation will change the wall assembly’s temperature gradient, which can be detrimental in winter conditions. For example, internal insulation layers will create a sizeable temperature drop, cooling the brick and potentially causing freeze-thaw damage. Also, masonry walls often do not have a dedicated air barrier system and can be very leaky. Therefore, airtightness is vital for the retrofit design, especially since interior air leakage can condense on the cold brick and cause potential moisture concerns and mould on the newly created interior finishes. Similar conditions apply to other mass-type walls such as pre-cast concrete, tilt-up, or concrete masonry unit where there is no existing insulation.
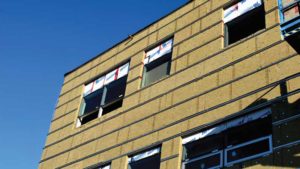
When retrofitting mass walls on the interior with stone wool insulation, it is recommended to be installed in combination with a capillary break between the masonry and insulation, in addition to an interior smart vapour retarder. For example, creating a capillary break using a vapour permeable, liquid-applied, air- and water-resistive barrier, or a gap up to 10 mm (0.38 in.) between the insulation and the substrate. For interior vapour control, a smart vapour retarder (a membrane that transitions in vapour permeability depending on the surrounding relative humidity) is best. In this case, it will assist with inward drying when necessary. For airtightness, the water-resistive barrier (WRB) and interior membrane, taped and sealed, can serve as the primary and secondary air barrier system critical to ensure airtightness requirements to limit moisture-related risks.
Challenges with the constructability of interior insulation systems on masonry walls are often design related. The enclosure is usually required to be thinner, to not take up more than necessary interior space. It may require the ability to be easily disassembled without damages to the existing substrate. In addition, the substrate may not always have an even surface in which using an insulation that allows for some compression such as stone wool insulation provides greater flexibility.