The Best Laid Plans: Risk management in building envelope design and construction
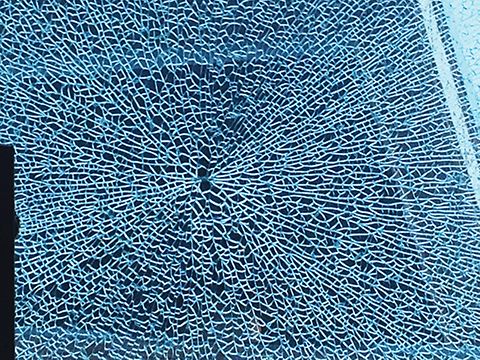
Collaborative design review
Collaborative design reviews or design charettes between project team consultants can be extremely beneficial through the planning process. Charrettes provide designers with a direct forum for quick idea sharing and feedback regarding the design of individual components and how they may affect other components or the design as a whole. What one team may see as a benefit could be a complication to another. Charettes allow designers to leverage expertise from various subject matter experts so a cohesive building envelope design can be developed.
Mockups, laboratory testing, and field testing
Similar to collaborative design reviews, using mockups and system testing is also essential to good design and execution. These are both valuable to ‘test-drive’ the design before it is fully implemented, and they provide an opportunity to catch problems earlier in the design and construction process while changes and revisions, if required, are less costly to make.
Field testing allows the design and construction team to gauge whether the fabricated product meets the original specifications. In other words, confirming building owners are actually ‘getting what they paid for’ is a good starting point to avoid unintended outcomes down the line.
QA/QC
Execution is as important as design. QA/QC procedures and plans are put in place to help constructors control and minimize missed steps between design and construction. These procedures can include asking for appropriate production submittals, documentation, and drawings early in the construction process, and reviewing them against the original design documents. QA/QC can also mean reviewing construction in the field and performing field testing to confirm the designs and products laid out on paper have actually been installed and executed correctly onsite.
Although QA/QC and testing are additional project costs, they should be considered valuable insurance to ensure money is not being wasted and the original design intents are being met. For example, building owners often pay a premium for window thermal upgrades such as argon fill and low-e coatings in insulated glazed (IG) units, but during field testing these authors have found the argon or low-e coating is installed incorrectly or missing altogether.
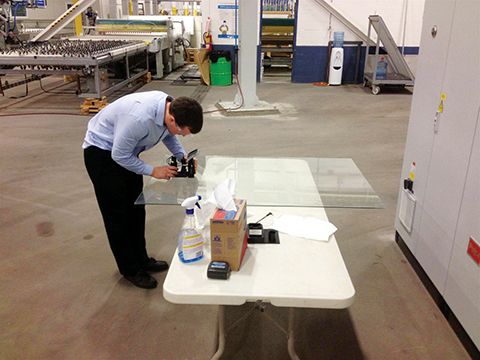
While usually unintentional, mistakes such as these can happen. Identifying and correcting the problems early can usually prevent them from escalating and becoming even larger, more costly issues in the future.
Maintenance plans
Turning over a building to the owner may symbolize the end of design construction, but the maintenance plan should not be an afterthought. Maintenance plans should be considered at the start of the design process because the design’s complexity and type of materials selected affect how a building will need to be maintained and the cost to operate it. This is also a principle outlined in CSA S478, Guideline on Durability in Buildings.
Conclusion
Despite their best intentions, design/construction teams occasionally develop buildings with performance issues when they do not give careful consideration to enclosure design, material choice, execution, and future maintenance. Strategies to manage these risks, including collaborative design reviews, mockups, testing, QA/QC, and upfront maintenance design can be costly. However, owners, developers, and constructors should recognize the cost of dealing with unintended consequences, and the resultant need to re-work and ‘design on the fly’ is potentially much higher. Generally, the earlier in the design process a problem can be caught, the less costly it will be down the road.
Andrea Yee, B.Sc.E., is a project manager with Halsall Associates, and has eight years of experience with building enclosure and repair/renewal projects. She can be reached via e-mail at ayee@halsall.com.
Nastassja Pearson, M.A.Sc., P.Eng, is a project manager with Halsall Associates, and has 10 years of experience with building enclosure and repair/renewal projects. She can be reached at npearson@halsall.com.