The Best Laid Plans: Risk management in building envelope design and construction
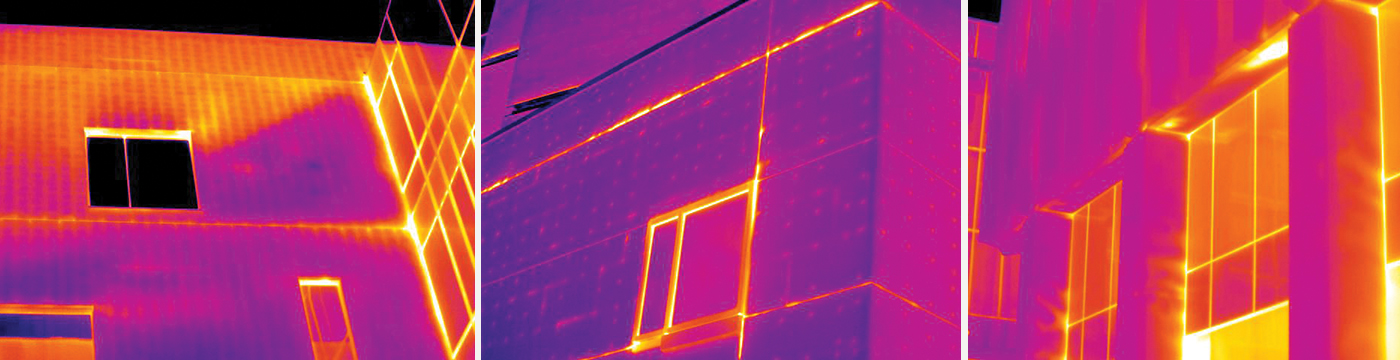
Complex and unusual designs
Designers often seek to create a distinctive identity for a building by including feature elements such as curved walls, twisting structures, inverted slopes, overhangs, and screens. Designers are also pushing the limits of what materials are able to do and what manufacturers are able to produce.
A good deal of thought is generally given to these complicated architectural features during construction. The same cannot be said for post-construction maintenance. For example, a building clad with a large decorative screen in front of a curtain wall may have had relatively straightforward construction, with the curtain wall installed prior to the screen. Careful thought may have been given to each component to ensure it could carry the screen’s weight and any ice and snow that may build up on the screen.
However, was equal consideration given to in-service maintenance? If a curtain wall glass unit requires replacement, does the screen need to be disassembled or can a new unit be installed with the screen in place? How will the area behind the screen be accessed? Is the proposed repair plan practical and/or costly? Is there a better, simpler way to replace the glass? These are the types of questions that should be considered and answered during the project design phase, long before the building is turned over to the owner/operator.
Prefabricated cladding panels
To speed up cladding installation and lower costs, designers and contractors are using more and more prefabricated cladding panels. These all-in-one panels are fabricated in a controlled environment where quality and consistency can be closely monitored. Typically, the air, vapour, and thermal control layers are built directly into the panels.
Using prefabricated panels typically means 90 per cent of the cladding can be installed in short order. However, completing the remaining 10 per cent—which includes the joints between panels, transitions with adjacent assembles, and enclosure pockets required around anchors—can account for the majority of the labour effort or time. This is because these components—especially joints, such as those between precast concrete panels—are often small and difficult to detail since access to them is limited once the panels are installed.
However, these joints and transitions are paramount to enclosure performance as they provide air, vapour, and thermal control layer continuity. Airtightness and resistance to water penetration are critical to a well-performing wall. Therefore, if time-consuming, costly repairs are later required due to inadequate onsite joint detailing, some benefits of prefabricated panels may be lost.
Managing unintended consequences
Designers, constructors, or owners cannot be expected to independently anticipate these issues. Rather, the best course of action is to maintain open lines of communication between the entire project team so everyone involved understands the design choices. In this way, concerns can be flagged, shared, and worked through. Activities that support open communication include:
- collaborative design reviews;
- using mockups;
- laboratory and field testing;
- establishing quality assurance (QA) and quality control (QC) procedures; and
- developing a sound maintenance plan.