The air/vapour barrier must die
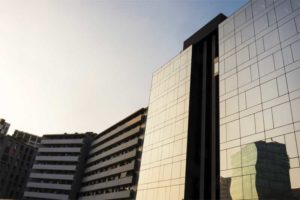
By Juste Fanou
The terms “air/vapour barriers” and “vapour retarder” are perhaps some of the most poorly understood concepts in the construction industry. Most building professionals know they are needed, but often struggle to locate them correctly within wall assemblies. Also, the consequences of installing these materials improperly can result in failures. This lack of understanding of the functions of these assemblies has resulted in simplistic rules-of-thumb prone to misapplication (e.g. the vapour barrier is always on the inside and the air barrier is always on the outside). As manufacturers introduce materials with new properties and attempt to push the boundaries of building envelope construction, it is crucial the industry agrees on terminology for communicating the specific functions and purpose of these materials to avoid confusion and costly errors. In this regard, the term “air/vapour barrier” is misleading and should be replaced with more appropriate terminology. This article briefly explores the origins of this term, the discrete functions of air barriers and vapour retarders in building envelopes, and the detrimental effects of incorrect terminology in construction documentation.
A brief history
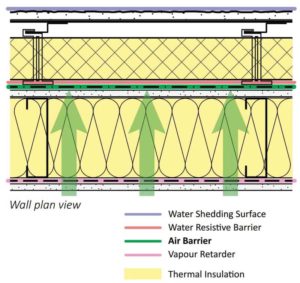
Images courtesy Juste Fanou
Initial attempts to increase the thermal comfort of occupants in modern North American wood-framed construction date back to the 1800s. The introduction of “building paper” in the form of asphalt-impregnated felt—also known as sheathing membranes or weather-resistive barriers (WRB)—represented an early effort to reduce wetting of wall assemblies and air leakage (Refer to the 2017 book Building Materials: Product Emission and Combustion Health Hazards by K. Hess-Kosa.). The industry made further advancements in the field of envelope performance in the 1930s with the rise of insulation in framing cavities and attics (For more information, read the article, “Heat, Air and Moisture Control in Walls of Canadian Houses: A Review of the Historic Basis for Current Practices,” by M. Koniorczyk and D. Gawin, published in the April 2008 issue of Journal of Building Physics.). However, the undesirable effects of moisture in insulated cavities soon surfaced. The traditionally painted wood façades began to suffer from peeling, blistering, and other coating failures. As is the norm in the building industry, a “blame game” quickly ensued with insulation manufacturers blaming the paint and vice-versa, while the building paper manufacturers were caught in the middle (Consult the paper, “The rise of the diffusion paradigm in the US,” by W.B. Rose, published in the 2003 book Research in Building Physics: Proceedings of the Second International Conference on Building Physics, edited by G. V. J. Carmeliet, H. Hens, and G. Vermeir.). It was not until the late 1930s scientists began investigating moisture movement in building assemblies. Their findings—considered controversial or even biased by some—concluded the transfer of water vapour by diffusion (a process explained later in this article) was responsible for the paint peeling off the siding (Many argue Frank Rowley’s theory of vapour diffusion, which led to the introduction of vapour barriers in wall cavities and ventilated attic spaces, was not grounded in sound science. This study is considered biased by many in the field, because it was funded by the insulation industry as a way to defend itself against claims insulation was responsible for condensation in cavity spaces and peeling paint.). These conclusions resulted in regulation mandating the use of low-vapour permeance membranes in construction projects in the early 1950s. It was the birth of the “vapour barrier,” and the industry celebrated its solution to the moisture problem by lining walls with polyethylene plastic. Ostensibly the issue of peeling paint was resolved, or at least it seemed so.
Nonetheless, moisture problems persisted. Further, research in the mid-1980s suggested uncontrolled air infiltration, and not vapour diffusion, was the largest contributor to moisture accumulation in cavity spaces (Consult R.L. Quirouette’s 1985 technical report, “The difference between a vapour barrier and an air barrier.”). However, by that time the popularity of the now ubiquitous “6 mil poly”—backed by the Canadian General Standards Board (CAN/CGSB) 51.34, Vapor Barrier, Polyethylene Sheet for Use in Building Construction—inspired methods to seal the already familiar vapour barrier. The purpose was to turn it into an effective air barrier.
These attempts to seal the vapour barrier may be characterized as the genesis of the “air/vapour barrier,” both as a concept and term. Conceptually, the “air/vapour barrier” was a material purported to address both air infiltration and vapour diffusion issues. Its proponents believed by sealing the joints of polyethylene sheets, a dual-purpose material could emerge ascribing the additional properties of air infiltration control to the already popular “6 mil poly.” This popularity was perhaps responsible for its great appeal and wide adoption in the industry. As time passed, however, the idea of “sealing polyethylene” was quickly abandoned, and construction practitioners explored other materials to provide airtightness. It was clear polyethylene was not a sufficiently durable material to resist the effects of wind gusts and pressures. Moreover, this lack of durability was further undermined by the intrinsic difficulties associated with installing polyethelene in a continuous fashion.
Even if the concept of the polyethylene “air/vapour barrier” slowly faded, the term endured. Coincidentally, as time passed it also appeared as if the general understanding of the functions of these air and moisture control elements was further clouded by this conflated term. These once-distinct materials slowly transformed into abstract dotted lines everyone knew were required on construction details, but no one fully understood where or why.
Differences
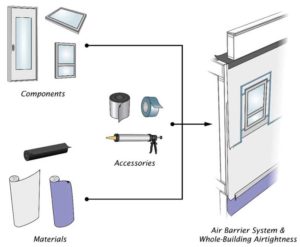
The building envelope performs important tasks. Its primary purpose is to protect conditioned spaces from the adverse effects of heat, air, water, and vapour. In other words, it keeps the outside out, and the inside in. This is achieved through a combination of carefully selected layers designed to stop and/or drain bulk water, insulate against heat loss, prevent or reduce air leakage, and slow down vapour migration. In building science settings, these are referred to as control layers (Read the 2010 article, “The Perfect Wall,” by J. Lstiburek.). Air barriers and vapour barriers form part of these control layers.
Air barriers, as their name implies, are intended to stop uncontrolled air from leaking into conditioned spaces. This infiltration is caused by the effects of wind, HVAC systems, and by air buoyancy forces also known as “the stack effect” (Refer to B.C. Housing’s 2017 Illustrated Guide – Achieving Airtight Buildings.). It is critical to stop uncontrolled air leakage, because air can act as a transport mechanism for several other undesirable particulates (e.g. smoke and odour). Additionally, air can also carry moisture. However, the maximum amount of moisture air can carry (its saturation point) is dependent on temperature and pressure. In general, cold air can carry less moisture than warm air.