Testing the Waters: Preventing moisture in concrete slabs
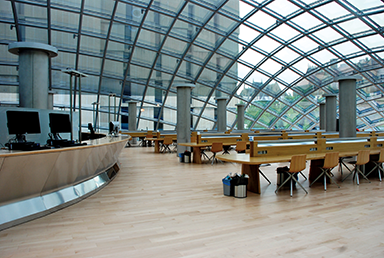
By Pete Robitaille
Moisture rising from concrete slabs can come from numerous sources, including concrete, drainage, burst pipes, condensation, aggregate above a membrane, and the ground itself. Although the problem appears in different forms, the outcome is always the same—the flooring will fail.
Moisture in concrete can result from a lack of protection of an efficient vapour retarder beneath a slab, as water moves up from the ground through capillary action or hydrostatic pressure. The concrete slab acts like a sponge, drawing up moisture from damp areas below to dry areas toward the surface until it reaches a natural balance. The problem may arise either soon after installation or during the structure’s lifetime due to changes in climate or the environment. For this reason, all concrete slabs—old or new—must be tested. It is critical to keep in mind that when a vapour retarder is not installed, tests are only valid for that moment, like a snapshot, since the situation can vary from one day to the next, from season to season, or from year to year.
In its second form, the problem is the result of capillary action in new concrete. Here, the slab has been laid in accordance with the applicable building code using a vapour retarder directly below or in a steel base. Moisture present within this type of installation is residual humidity, which should dissipate over time. This is dependent on climatic and environmental conditions both inside and out, the grade of concrete, the water content in the mix, or the curing compound. However, installing flooring onto the slab before dampness has had time to evaporate to an acceptable level will most likely result in its failure.
To prevent that from occurring, it is critical to perform moisture tests prior to installation. Several types of test equipment and methods are available on the market. The following two methods are most often used to test for moisture.
ASTM F1869
The calcium chloride vapour emission test performed in accordance with ASTM F1869, Standard Test Method for Measuring Moisture Vapour Emission Rate of Concrete Subfloor Using Anhydrous Calcium Chloride, consists of determining the amount of water vapour transmitted through a concrete slab. The test result is expressed in kg per m² (pounds per 1000 sf) over a 24-hour period.
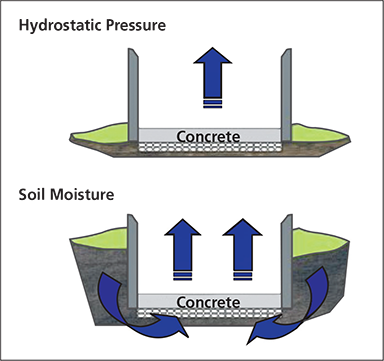
Briefly, the test consists of grinding and cleaning a 510 x 510-mm (20 x 20-in.) area of concrete and letting it acclimate for 24 hours. Next, a precisely weighed petri dish containing anhydrous calcium chloride granules is placed under a plastic dome covering 0.09 m2 (1 sf) and the dome is sealed to the concrete. (Anhydrous calcium chloride is hydroscopic—that is, it wants to absorb water.) This assembly is left in place for 60 to 72 hours, after which the petri dish is weighed once more. The difference in weight (i.e. the amount of moisture absorbed by the calcium chloride) is calculated to determine the moisture vapour emission rate (MVER) migrating through the slab.
This test is required to be performed when the building’s HVAC system is operating and the building has been acclimated. It is important to remember ASTM F1869 only captures the MVER at a specific point in time, and it can fluctuate due to environmental conditions outside the building envelope. Whatever the moisture flow is at the time, it will migrate until it hits something it cannot penetrate, such as non-porous finishing materials.
ASTM F2170
The second method most commonly used to test for moisture is ASTM F2170, Standard Test Method for Determining Relative Humidity in Concrete Floor Slabs Using In Situ Probes, which provides the slab’s relative humidity (RH) expressed as a percentage. In essence, the test consists of drilling a hole into the concrete to a determined depth. Next, a probe sleeve is inserted into the hole before it is sealed so ambient air from above cannot enter the chamber. Electronic probes are then inserted into the probe sleeve and allowed to acclimate. Lastly, measurements are taken to determine the relative humidity of the air space at the bottom of the probe sleeve, which is an indication of the moisture present in the concrete.
There are substantial differences in the two tests regarding what they measure. ASTM F1869 measures the potential moisture flow over time, while ASTM F2170 is a static measurement indicating the percentage of relative humidity in the slab at a given point in time. The majority of flooring and adhesive manufacturersrecommend the concrete should emit no more than 1.36 to 2.27 kg (3 to 5 lb) of moisture when measured using the calcium chloride test and a level of 75 to 80 per cent relative humidity usingthe RH test. Manufacturers have set these maximum moisture levels as the threshold values for a worry-free installation.
Both tests have their advantages and disadvantages. ASTM F1869 can indicate the MVER flow, but it cannot determine how much moisture is in the concrete slab when the test is performed. In contrast, ASTM F2170 measures how much moisture is in the concrete at the time of the test, however, it cannot be used to measure how fast it is flowing. Neither test can be used to determine whether moisture is entering the concrete from an outside source, such as a breach in the vapour barrier beneath the slab or from plumbing leaks within the concrete. This information could be vital to an installation’s performance.
Which one should a project team choose? Is it best to perform one or both tests? If both tests are conducted, which one should prevail when there is no correlation between them? In this case, one should consider opting for the least favourable result, as it is better to be safe than sorry.
For accuracy’s sake
The following conditions can affect test results and care should be taken to avoid them.
- Did any of the crystals in the calcium chloride test spill out of the petri dish, or were some lost during manipulation?
- Has the dome been properly sealed onto the concrete surface?
- Were tests conducted in the presence of a curing agent, sealant, patching compound, or other materials or compounds?
- Was an efficient vapour retarder present directly below the concrete slab?
- Does the depth of the hole for the RH test comply with manufacturer and ASTM recommendations?
- Did the RH probe have time to acclimate?
Additionally, it is critical to keep in mind both tests can be adversely affected when the HVAC is not operational and/or when the building has not been allowed sufficient time to acclimate to ‘in-service’ conditions. Although these testing procedures are clear on the building’s acclimation prior to testing, this aspect is often ignored. Manufacturers aware of the importance of operational HVAC and acclimation will not accept testing results when these conditions are not met.
Conclusion
To prevent the flow of moisture through concrete slabs, one must refer to ASTM standards and follow them diligently. That said, there are solutions to all the conditions mentioned in this article when the results are off from the manufacturer’s tolerances. These include 100 per cent epoxy vapour barriers that are easy to apply or acrylic polymer applications for fresh concrete. Lastly, it is highly advisable to have either test run by an independent company specializing in performing these ASTM methods.
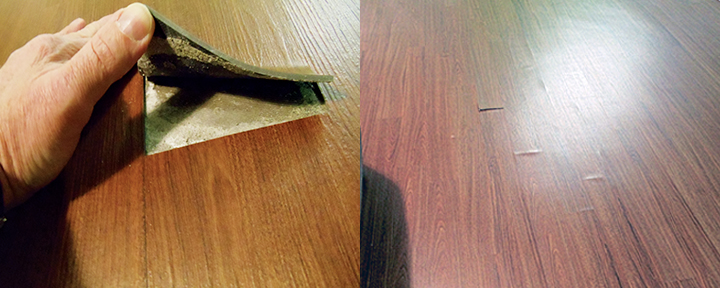
Pete Robitaille is an original equipment manufacturer (OEM) consultant specializing in floorcovering installation systems at Canada’s Mapei Inc. He has accrued several industry certifications and has extensive experience as an installer, sales representative, and retail store manager, as well as a residential, commercial, and institutional estimator. Robitaille can be reached via e-mail at probitaille@mapei.com.