Testing concrete mix to predict durability
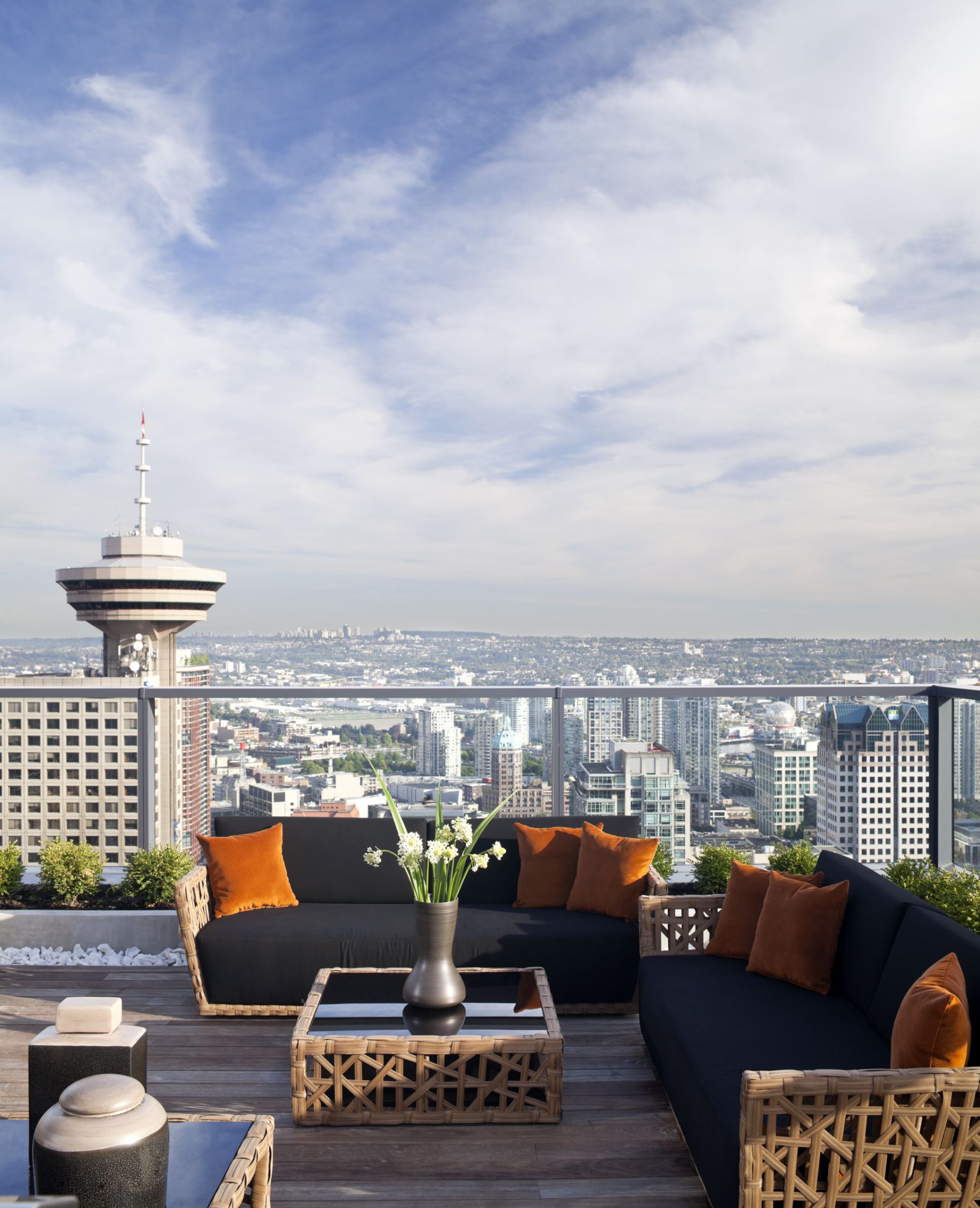
By Alireza Biparva, B.Sc., M.A.Sc.
With some predictions estimating the global population will reach as high as 11 billion by 2050, it is crucial the design community plans infrastructure with sustainable and innovative practices in mind. As concrete is the most commonly used building material in the world—employed more than all other building materials combined1—its ability to perform well has a direct impact on how sustainable the structure it supports is.
Durability is the key
Concrete’s durability is defined by its ability to resist weathering action and chemical attack, while maintaining the desired engineering properties. Due to the use of inappropriate materials, poor construction practices, insufficient curing, and/or improper mix designs, many structures show serious premature deterioration. This problem costs both the public and private sectors worldwide billions of dollars annually. About 2.35 billion tonnes of cement is produced globally every year,2 with the New Civil Engineer (NCE)/Institution of Civil Engineers (ICE) reporting approximately 40 per cent of construction work in the United Kingdom goes toward repair and maintenance work rather than creating new infrastructure.3 Optimizing the durability of concrete ultimately leads to fewer repairs or premature replacements of deteriorating structures.
Measuring the durability factor of concrete to determine its longevity, and ability to withstand local weathering and use, is difficult to predetermine. It is, however, an important factor in identifying how sustainable the structure will ultimately be.
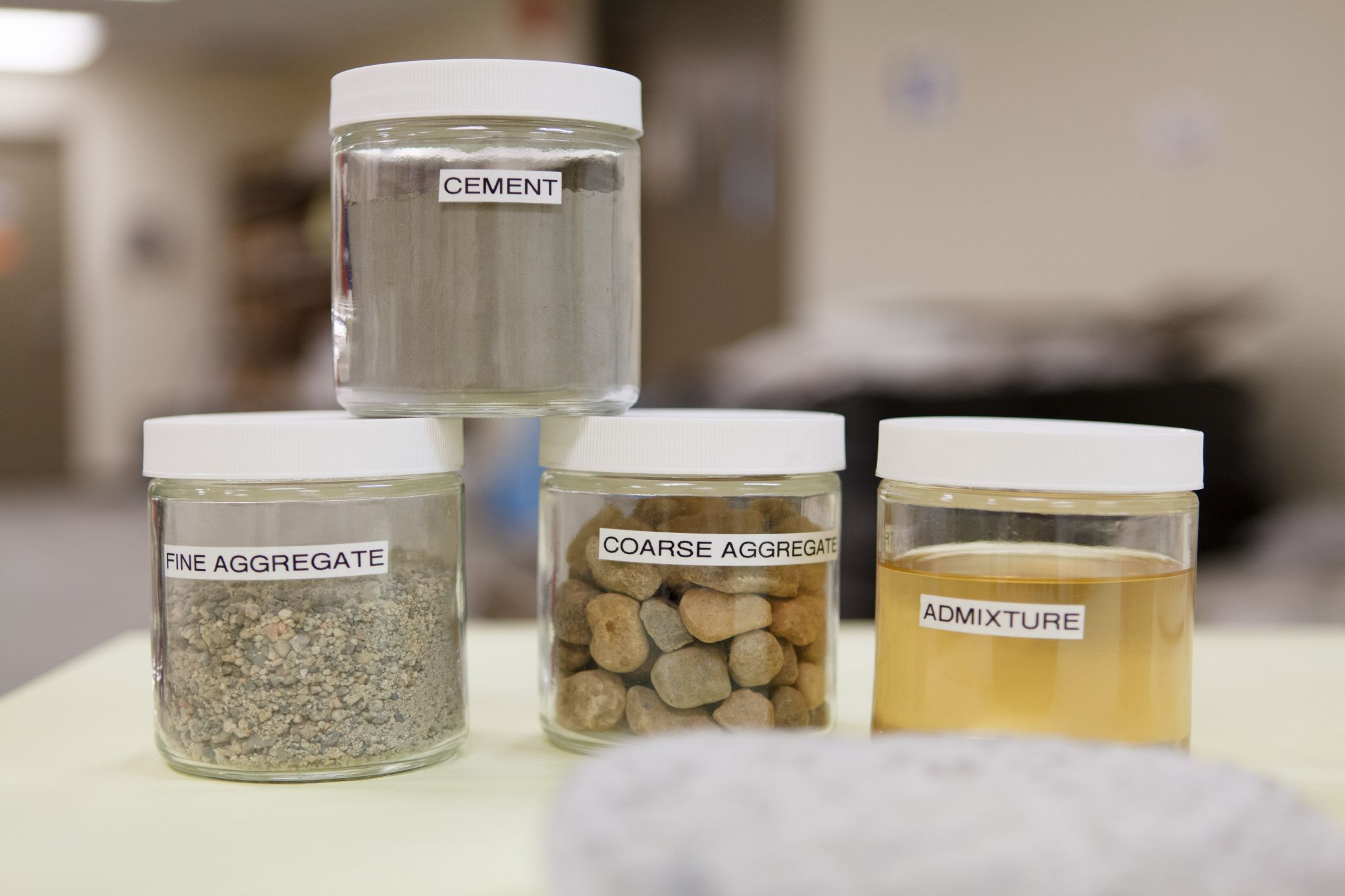
The durability of a concrete mix is contingent on numerous factors. The concrete mix design must be customized for the environment, and high-end materials do not necessarily make for a durable concrete. Further, a durable mix design in one location may not be durable in another. For example, in dry, desert-like environments, air entrainment is not necessary for concrete to be durable, whereas it is a critical factor in Canada due to freeze-thaw issues.
Another factor in defining durability depends on how long a building is actually designed to last. If a building is designed to last 50 years, and makes it to 60 before major repairs or replacements are necessary, then that building by definition is durable. If a building is designed to last a century but stands for 70 years, it cannot be considered a durable structure. Questions to consider when determining durability include:
- What is the project to be used for (current and future use)?
- What type of environment will this structure be exposed to?
- How many years must this structure remain?
Concrete not living up to predictions
Despite the complexity and many factors affecting concrete’s durability, the main one is moisture penetration. As a porous material, concrete can allow water to migrate through it, corroding steel reinforcement, bringing in harmful chemicals, or causing other short- or long-term issues requiring serious attention.
Most of the mechanisms attacking concrete structures need water. To have a durable structure, it is evident permeation of water through concrete must be reduced. This is why some sort of waterproofing protection is necessary to secure the durability, and resulting sustainability, of concrete structures.
Quantifying the durability of concrete mix designs can be difficult. When it comes to testing concrete for strength, the parameters are easily defined in any situation—50 MPa concrete means the same thing regardless of environmental factors. The project may be looking for different strength capacities for the concrete, but the numbers are easy to define. Testing for durability, on the other hand, is difficult to define by direct testing methods. However, using the close relationship between permeability and durability, the projected durability of a concrete mix may be deduced through testing the permeability of the mix.
Tests such as water absorption, surface absorption, water permeability, or chloride permeability are commonly specified. These tests should take into account the unique properties of the mix design when used to ultimately determine concrete’s durability.
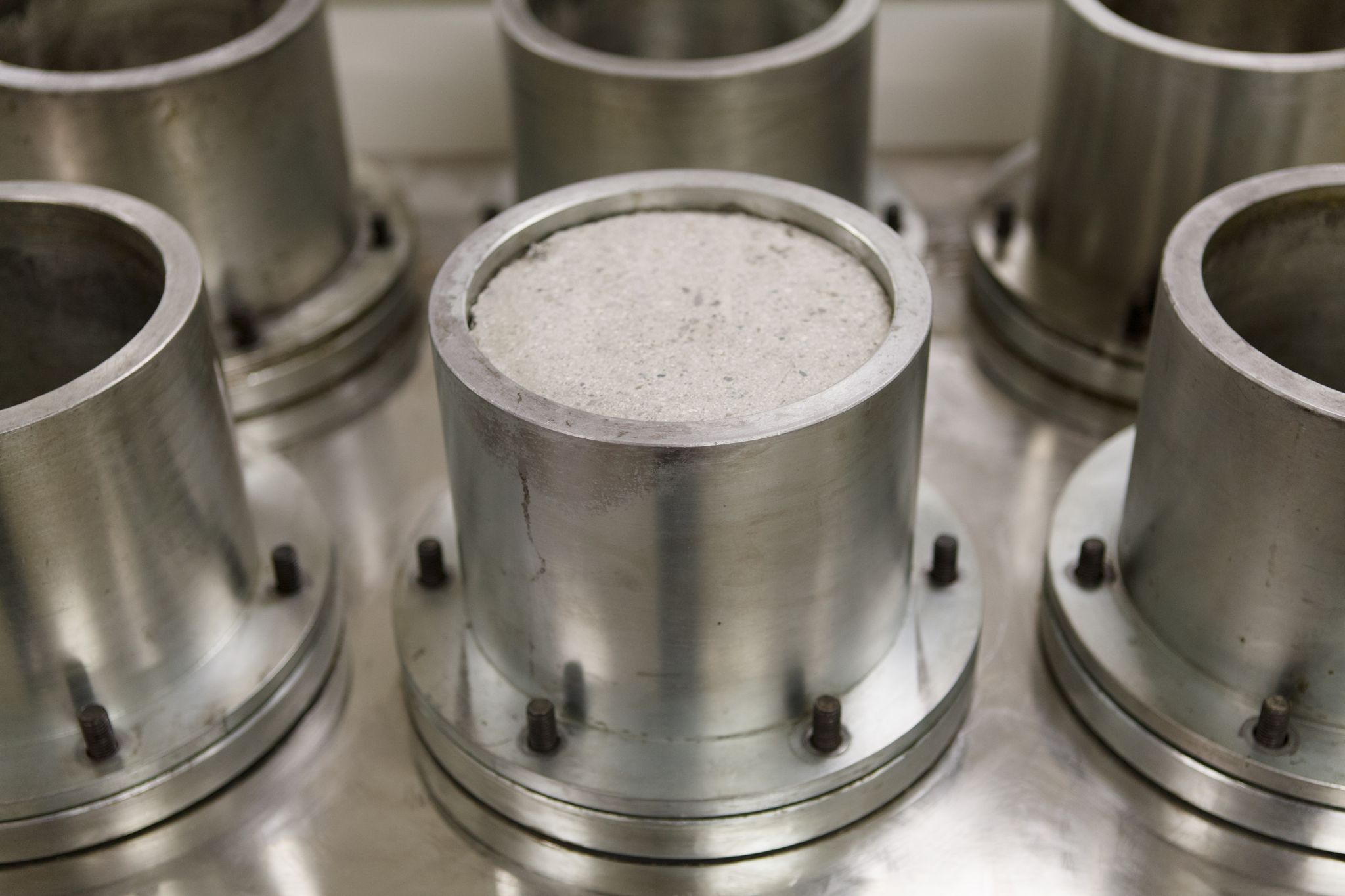
Absorption
Absorption testing is a popular method of determining the water-tightness. A water absorption test, such as BS 1881-122: 2011 Testing Concrete: Method for Determination of Water Absorption, measures the amount of water that penetrates into concrete samples when submersed. Low absorption is considered a positive result. However, this test has inherent limitations, including:
- short duration of submersion compared to potential long-term service conditions;
- no accounting for any type of reactive process that ties up water; and
- assumption all weight gain is water, rather than reactive processes.
Additionally, absorption testing can be misleading when it comes to the use of admixtures, such as hydrophilic crystalline waterproofing admixtures. Integral crystalline waterproofing involves the use of chemicals, which when combined with cement and water; react with the unhydrated cement particles to form millions of needle-like crystals. These crystals fill the naturally occurring capillary pores and microscopic voids within the concrete. Paths for harmful moisture and aggressive chemicals are blocked. Absorption testing measures the amount of water that penetrates into concrete samples when submersed, but fails to take into account the inherent use of water in the crystallization process, particularly in the early stages of curing (less than 28 days). The absorption test results will improve over time—as the concrete is saturated and crystals continue to grow. Therefore, in the case of crystalline admixtures, testing the absorption at later ages—such as 56 or 90 days—will give more realistic results.

water penetration is through a permeability test, like the one shown at right.
Rapid chloride permeability test
The Rapid Chloride Permeability (RCP) test is the standard test method for electrical indication of concrete’s ability to resist chloride ion penetration. Test methods—such as ASTM C1202, Standard Test Method for Electrical Indication of Concrete’s Ability to Resist Chloride Ion Penetration—consists of monitoring the amount of electrical current passed through cylindrical specimens for a duration of six hours. The total charge passed, in coulombs, relates directly to the resistance of the sample specimen to chloride ion penetration.
The RCP test has gained wide acceptance as a relatively easy and quick method for determining concrete permeability. What it achieves in timeliness, however, it lacks in accuracy.
Various drawbacks make this test unreliable, especially for the comparison of different mix designs or for evaluating concrete durability.
Some limitations are:
- allowance for premature measurements (before a steady state is achieved);
- applied high voltage leads to an increase in temperature to the sample, and can cause physical and chemical changes resulting in unrealistic values;
- there can be misleading results largely due to the chemical composition of the pore solution, rather than from the true permeability;
- concrete resistivity, rather than permeability, is measured—resistance is calculated as volts divided by current and it has been shown there is a fair correlation between concrete resistivity and concrete permeability, but it is not the intended use of the RCP test; and
- low inherent repeatability and reproducibility.
An additional limitation is the electric current that passes through the sample during the test, indicates the movement of not just chloride ions, but all ions in the pore solution (the sample’s electrical conductivity); therefore, this test may not represent the true permeability (or potential permeability) for concrete that contains supplementary cementitious materials (e.g. fly ash, silica fume, or ground granulated blast-furnace slag) or chemical admixtures (e.g. water reducers, superplasticizers, or corrosion inhibitors).
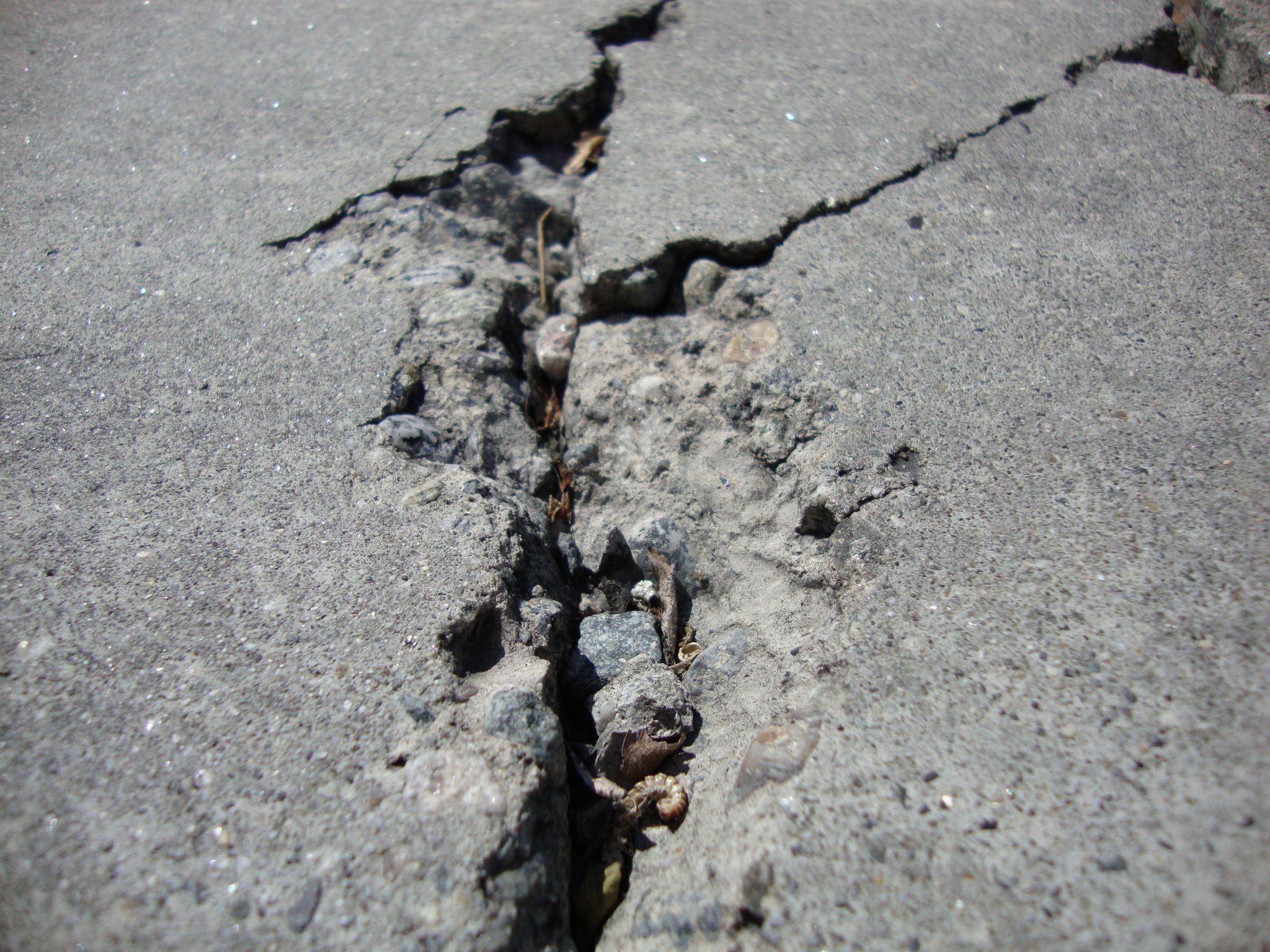
There has been a great deal of debate over this test method because of large variations in results on companion test specimens. The ASTM method shows the results of two properly conducted tests by the same operator on concrete samples from the same batch may differ as much as 42 per cent. On companion samples tested by different laboratories, this percentage is raised to 51 per cent. This large variability in test results indicates the relative inaccuracy of the test method, while maintaining that concrete samples lying within this large acceptable range are essentially equal in quality.
Overall, the ASTM test method is suitable for the evaluation of materials and material proportions for design purposes, and for research and development. However, it has incorrectly become one of the tests used to evaluate the durability of concrete. RCP can qualify a mix, but not necessarily disqualify it.
Despite these drawbacks and limitations, the RCP method is the only rapid, relatively simple, standard existing test to evaluate concrete’s ability to resist chloride ion penetration. Until other standard tests become available, or proper modifications are performed to correct or mitigate the limitations, this method may be used, but should be approached with a great deal of caution. The RCP test should not be employed to accurately determine the permeability of a concrete mix containing supplementary cementitious materials (SCMs) or chemical admixtures.
Water permeability test
These tests determine the true permeability of concrete by evaluating the resistance of concrete against the penetration of water under hydrostatic pressure. A permeability test should be considered the dominant test to evaluate the case whereby concrete is subjected to hydrostatic pressure.
BS EN 12390-8, Testing Hardened Concrete: Depth of Penetration of Water Under Pressure, and DIN 1048 Part 5, Testing Concrete: Testing of Hardened Concrete Water Permeability, are equivalent tests that measure the depth of water penetration into concrete samples subjected to 0.5 MPa (72.5 psi) of hydrostatic pressure over a period of three days. Concrete specimens are cast and cured for 28 days. After curing, samples are then placed in the testing device. The sample-holders are open at both ends, with one end subjected to hydrostatic pressure. After three days, the samples are removed from the testing apparatus and cracked in half vertically. The maximum depth of water penetration into the sample is then measured.
When analyzing the results, the smaller the depth of penetration results in a higher resistance to water under hydrostatic pressure. This test method is useful for structures such as basements, tunnels, and water reservoirs because it recreates the pressure conditions to which these structures are subjected in a realistic way.
In spite of many advantages, like other tests, this test method has some limitations, such as:
- for a dense and low-permeable mix, the depth of water penetration is low, making it difficult to compare the mixes that have low permeation (for these cases, the pressure or testing age can be modified); and
- evaluating cases in which the concrete is not under hydrostatic pressure, this test method should be considered as an auxiliary method—tests such as absorption should dominate.
The BS EN 12390-8 and DIN 1048 Part 5 tests should be considered as the predominate ways to evaluate the case in which concrete is subject to hydrostatic pressure. These tests measure the true permeability of a concrete mix, as they evaluate the resistance of concrete against the penetration of water under hydrostatic pressure. Products required to resist water under pressure must be evaluated using this testing method.

Concrete’s permeability is a good indicator of its quality and durability, but it is not all that is needed to determine an accurate conclusion regarding the durability of a concrete mix. It is not always enough for concrete to feature low permeability. Durable concrete is relatively impermeable as long as it remains un-cracked. The tendency of concrete to crack plays a significant role in the overall durability of the mix, but this property is often ignored. Cracks occur due to various factors including early age shrinkage and loading during its service life. These cracks create a direct pathway for moisture and harmful chemicals to enter the concrete, which may compromise the durability and structural performance. Cracks represent a significant risk for early corrosion and deterioration in concrete.
Therefore, in addition to the typical tests mentioned in this article, performing tests that demonstrate crack tendency such as a shrinkage test are vital in determining concrete durability.
Conclusion
The available tests for durability have some drawbacks, and it is necessary to understand and recognize these limitations. Environmentally specific mix designs are necessary for every unique condition, and service environment-appropriate test methods are necessary for each condition as well. Absorption tests are best suited for cases with little or no hydrostatic pressure with intermittent moisture such as repelling rain from building facades. In contrast, a permeability test should be considered the main test to evaluate where concrete is subjected to hydrostatic pressure such as basements, water reservoirs, and tunnels.
The focus of specifications for testing the durability of concrete should put the most weight on determining the concrete’s permeability, resistance to environmental factors, and tendency to crack.
Notes
1 For more, see World Business Council for Sustainable Development’s “Sustainability Benefits of Concrete” at www.wbcsdcement.org/index.php/about-cement/benefits-of-concrete. (back to top)
2 For more, see Denise Brehm’s article, “Nanoengineered Concrete Could Cut Carbon Dioxide Emissions” at newsoffice.mit.edu/2007/concrete. (back to top)
3 See “Sustainable Concrete for the 21st Century—Concept of Strength through Durability” at www.jsce.or.jp/committee/concrete/e/newsletter/newsletter13/Paper1.pdf. (back to top)
Alireza Biparva, B.Sc., M.A.Sc., LEED GA, is research and development manager/concrete specialist at Kryton International Inc. He has more than 20 years of experience in the field of concrete permeability. Biparva oversees several research projects focusing primarily on concrete permeability studies and the development of innovative products and testing methods for the concrete waterproofing and construction industries. He is an active member with the American Concrete Institute (ACI), and has given more than 300 presentations on concrete permeability, waterproofing, durability, and sustainability around the world. Biparva can be reached by e-mail at alireza@kryton.com.