Tension fabric structures: setting a new standard for facility construction
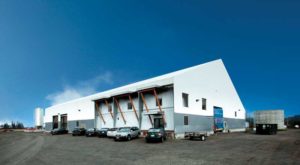
By Ben Fox and Ellie Fox
i-
In the case of tension fabric buildings, there exists the unique potential for miscommunication while even just considering whether a fabric structure is the right architectural choice in the first place. This breakdown is not so much about a failure to communicate, however, but more of terminology simply meaning different things to different people based on experiences.
For many, the term “fabric building” carries negative connotations of being a cheap or temporary option. For others, the exact same words are 100 per cent positive, as this group understands that with the right approach, fabric cladding brings a multitude of potential benefits to the table for water treatment facilities, recreational complexes, aircraft hangars, waste-to-energy plants, bulk salt/sand storage, and numerous other applications.
Revolutionary engineering
It is common with any product or service that has come a long way to describe that journey as its evolution. While evolution is a fair term to illustrate the past decade of the fabric building industry, what happened in the years before is perhaps better described as a revolution—a paradigm shift that fundamentally changed how fabric buildings were conceived and perceived.
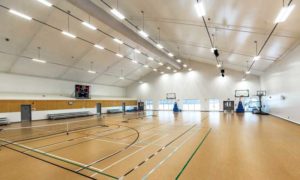
Prior to 2010, most fabric structures were erected with hollow-tube web truss frames, and users were limited to whatever pre-defined dimension offerings had been established by different manufacturers. This often forced customers into a dilemma: settle for a cramped space or purchase more building than necessary. Such a decision was never ideal, but in certain industries with only the most basic facility needs, it was considered satisfactory.
What happened next changed everything for fabric buildings. Leading manufacturers developed a method for applying fabric to a structural-steel rigid frame that used solid I-beams instead of web truss framing. This shift instantly advanced the credibility of fabric buildings within the engineering community. It was not merely a step along an evolutionary path; it was a revolution of such magnitude that it registered more like the creation of a wholly new product category. Rigid-frame design had opened a completely uncharted road for fabric structures.