Tension fabric structures: setting a new standard for facility construction
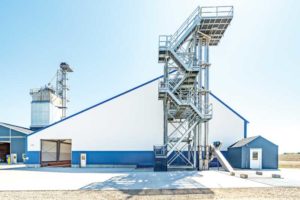
Fabric pays off
A prominent differentiator for fabric buildings compared to brick-and-mortar construction is the speed of installation. Long-term schedules with a conventional build can be shortened to a timeframe of just months with a tension fabric building, however, there are key differences within the
fabric realm.
Some suppliers require customers to hire subcontractors to erect the structure. Other companies have their own trained crews, to ensure proper horizontal and vertical tensioning of the fabric, among many other critical details.
The pace at which projects are completed is especially notable in today’s economic landscape. Those who are hesitant to move forward with building projects because of higher interest rates may find that fabric improves the financial picture, simply by allowing them to become fully operational in a building much faster; in turn, they can quickly start realizing their return on investment (ROI).
After considering the innovative design approaches and material upgrades that have occurred and seeing how widely accepted tension fabric structures have become across so many markets, one realizes it is not hyperbole to consider modern fabric buildings to be a revolutionary facility solution.
Authors
Ben Fox is the founder and president of Legacy Building Solutions. Along with two-plus decades of fabric building experience, he notably created the process for applying fabric cladding to rigid steel frames. He can be reached at bfox@legacybuildingsolutions.com.
Ellie Fox is the chief operating officer of Legacy Building Solutions. With 10 years of experience in the fabric building industry, she oversees operations throughout the company. She can be reached via email at
efox@legacybuildingsolutions.com.