Tension fabric structures: setting a new standard for facility construction
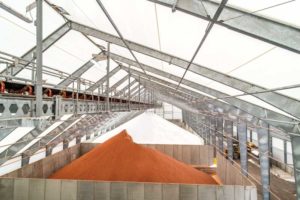
With I-beam frame engineering, all buildings get a clean sheet design from the beginning. Using finite element analysis software, engineers could now customize the building to meet individual user requirements. In other words, fabric structure suppliers had begun employing conventional construction methods, while still being able to offer the benefits of a fabric membrane solution, which can include natural daylighting, cost-effectiveness, and energy efficiency.
Constant innovation
Supported by proven engineering, structural frame designs empower users with the flexibility to implement wide clear spans or taller height clearances. I-beams can also be individually optimized in the design process to account for suspended loads on the structure, such as mezzanines, conveyors, light fixtures, HVAC, and fire suppression systems.
Customized designs and larger dimensions were only the beginning. Engineers continued their push to innovate fabric building beyond what most had considered possible. With I-beam design in play, fabric buildings could be fitted up with other construction materials.
Suppliers began to work with project subcontractors to place fabric building framing members alongside metal or steel stud and gypsum board partition build-outs. Materials such as brick and stone are commonly implemented for facades along fabric exterior walls. I-beam tension fabric structures can also accommodate overhead and roll-up doors, personnel doors, and even windows.
With greater capabilities came increasing opportunities to tackle more complex jobs. In many cases, the primary structure itself is not the most intricate aspect of the project. Fabric building manufacturers have taken on a variety of new challenges. In many cases, the main structure may not be the most complex part of the job. Notable projects have seen manufacturers install a fabric structure over existing wastewater plant equipment, provide a new fabric-cladded addition to a conventional brick-and-mortar building, and supply multiple buildings at varying elevations that needed to be properly terrain-matched to accommodate an accessibility ramp and elevator in a connecting foyer.
Optimization has become paramount to fabric building design. The days of fabric structures coming in pre-engineered, off-the-shelf size offerings share little resemblance to today’s quality-driven approach of providing the optimal solution to the client.