Sustaining a KEE standard for roofing membranes
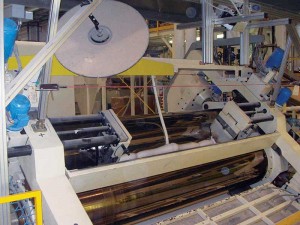
Realizing EIP coating technology used Elvaloy instead of PVC as the backbone for the polymer matrix, the title for the standard was changed to better reflect the chemistry. The standard’s title was subsequently changed to “Ethyl Vinyl Acetate Carbon Monoxide Terpolymer Sheet Roofing.” (Subjecting the roofing industry to EVACMT as a reference acronym would have been cruel.)
In 1997, the standard’s title was changed again as the subcommittee refined its understanding of the chemistry and technology associated with the manufacture and processing of Elvaloy. ‘KEE’ was eventually agreed on as the appropriate acronym to describe the polymer and chemical backbone of the compound. Hence, the proposed ASTM specification for a KEE sheet membrane was defined, but stood in contrast with the conventional definition and description for a PVC sheet membrane within ASTM D 4434-96:
3.3 Polymer Content: In this specification, polymer content shall be defined as polymeric materials which are in the solid state at room temperature, and are high (greater than 50,000) in molecular weight. Other ingredients, known to the art of polymer compounding, such as certain waxes, stabilizers, and other additives, while polymeric in nature are not considered to be part of the base polymer system.
4.1 The sheet shall be formulated from the appropriate polymers and other compounding ingredients. The KEE polymer shall be a minimum of 50% by weight of the polymer content of the sheet.
The proponents of KEE sheet membranes were about to shatter the ‘thicker is better’ ethos that evolved from ASTM D 4434. Since it takes consensus among committee members to move the process along, satisfying all the concerns raised took time.
There were two KEE issues that stood in stark contrast to the ASTM D 4434 PVC standard. Although KEE membranes exceed the majority of the physical property requirements of D 4434, they were significantly thinner than the 1.14-mm (0.045-in.) minimum and exhibited a higher water absorption characteristic when evaluated under the ‘high temperature’ exposure requirements within the D 4434 test methods.
Apart from the technical discussions on how to statistically analyze and display the data assembled, thickness and water absorption were the most significant objections toward adoption of the standard within the subcommittee. The KEE proponents were asked to prove that thickness and water absorption as historically defined within ASTM D 4434 were not appropriate mandates for performance.
How thick is thick enough?
Depending on the internal fabrics or reinforcements, initial impact resistance may be improved with the additional mass when testing new membranes. However, roofing membranes anchored to low-molecular-weight liquid polymeric technologies are known to be prone to loss of flexibility due to plasticizer migration. This has been, and will continue to be, a factor affecting in-situ performance of PVC roofing systems.
Today, the thickness paradigm is rampant and crosses all polymeric materials. Is the push for thicker membranes really necessary? When consideration is given to the roofing industry’s new obsessions with sustainability, the question is not just whether these thicker materials are relevant to performance, but also if they can be stewards of our limited natural resources.
By definition, a true KEE membrane does not have to be thick to exhibit very desirable membrane attributes or retard the loss of some migratory component. The material does not migrate, and a bonafide KEE membrane with a minimum thickness of 0.81 mm (0.03 in.) has demonstrated its ability to remain flexible and endure in harsh environments for more than 25 years. The membrane’s strength attributes come from the fabric, not its thickness. If the fabric is properly engineered, then the coating’s purpose is to protect the fabric’s inherent attributes. Of course, the coating does have to endure the effects of time—and with roofing, time is brutal.
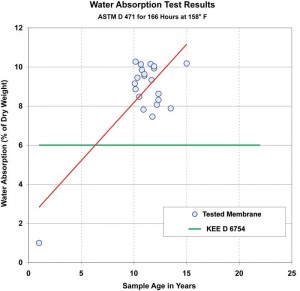
ASTM D 4434 prompted the adoption of a 1.14-mm (0.045-in.) standard within the industry, but the trend has been for many manufacturers to promote even thicker materials ranging from 1.27 to 2.29 mm (0.05 to 0.09 in.). Curiously, the increase in thickness rarely yields a corresponding increase in physical properties.
To a certain degree, some additional thickness is understandable in light of the ever-increasing expectations with regard to the tenure of commercial roofing warranties and their associated liabilities over the same period. To assume ‘two times the thickness’ equates to ‘two times the design service life’ may just be wishful thinking. The empirical data regarding the actual service life of these thick (and generally overweight) sheets is lacking.
As the roofing industry continues to grapple with sustainability, there needs to be brutally honest evaluations. The most recognized definition of a sustainable roof comes from the Proceedings of the Sustainable Low-Slope Roofing Workshop, held at Tennessee’s Oak Ridge National Laboratory (ORNL) in October 1996:
A roofing system that is designed, constructed, maintained, rehabilitated, and demolished with an emphasis throughout its life cycle on using natural resources efficiently and preserving the global environment.
Are the overweight single-ply roofing membranes truly using natural resources efficiently? The epitome of sustainability is getting more with less. Durability is at the centre of this paradox.
Water absorption
Water absorption was the second comparative issue between ASTM D 6754 and D 4434. The much thinner KEE membranes had the proven ability to endure and sustain their performance within a broad spectrum of the hostile rooftop environments. However, when immersed in a high-temperature water bath, they exhibit absorption characteristics higher than conventional PVC membranes defined within the context of D 4434.
In addition to variable fabric densities within the membranes, different polymers exhibit different affinities to water. Properly compounded KEE membranes, as defined within the context of ASTM D 6754, may appear to have increased high-temperature water absorption characteristics, but they are proven to excel as waterproofing membranes.
ASTM D 4434 allows for membranes to experience a three per cent weight gain or loss after the water absorption test. ASTM D 6754-02, on the other hand, did not allow for any weight loss. Since water is not chemically reactive or degrading to either PVC or Elvaloy, the increase in water take-up for KEE roofing membranes, when evaluated at high temperature, does not translate into a detrimental performance factor.
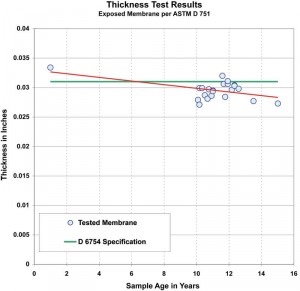
There are a few additional tests and property limits recognized within the KEE standard that should not only characterize minimum values for KEE membranes, but should also be considered essential to the overall performance of all roofing membranes. Adhesion of the coating to the reinforcement and resistance to hydrostatic pressure, fungi, and abrasion may all contribute to the ‘design service life’ of a membrane roofing system, but are conspicuously absent in ASTM D 4434.
KEE membranes are also characterized with having excellent chemical resistance. The rooftop environment is one of contamination. In addition to direct exhaust exposure, areas of ponding water can accumulate all forms of fallout. Even seemingly benign contaminants like oils, greases, and fats can accelerate the aging process for PVC membranes by accelerating plasticizer loss. Properly formulated KEE membranes begin with flexibility, creating a permanent phased-polymer, and they are not prone to having this flexibility extracted.
Durability discussions
All roofing systems have some hidden Achilles heel. KEE membranes can be vulnerable to low-molecular-weight liquid polymeric plasticizers. While formulations do not rely on liquid plasticizers for flexibility, some liquid plasticizers may be used during processing. High molecular weight KEE and PVC polymers have a natural affinity for lightweight plasticizers. Consequently, exposing KEE membranes to these low molecular weight polymerics can promote over-plasticization and softening of the membrane under warm exposure.
To address the committee’s concerns once and for all, a 10-year history of performance for KEE membranes was assembled and presented to the subcommittee. The history included a certified sampling of roof systems over a decade old in Florida, Ohio, Colorado, Wisconsin, and Texas. This sampling was supported by a 1997 study and evaluation of KEE roofing systems by Exterior Research & Design LLC.
Samples of the membranes were presented to the committee, evaluated against the proposed KEE standard for new materials, and subsequently found to be in excellent condition. They all retained more than 90 per cent of their original physical property requirements, including thickness. Many of the 10-year-old samples were exposed to additional accelerated weathering tests including QUV (i.e. accelerated weathering) and heat aging.
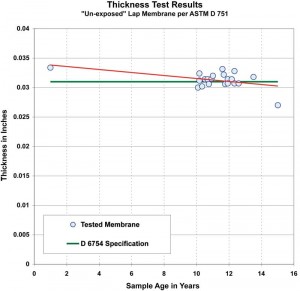
The committee eventually concluded the results from immersing a 25.4 x 50.8-mm (1 x 2-in.) sample of membrane in a 70-C (158-F) water bath for seven days (as described within ASTM D 4434), was not an acceptable test method for the characterization of a KEE membrane. One-side water absorption evaluation—similar to requirements for ethylene propylene diene monomer (EPDM)—was selected as a more appropriate test method.
Conclusion
Properly compounded and engineered 0.81-mm (0.03-in.) KEE membranes have a proven performance record. Physical property paradigms that had generated the greatest concern—specifically, thickness and water absorption according to conventional evaluation of PVC membranes—were determined to be of no consequence and non-persuasive. Those challenging the standard had offered no evidence supporting their archaic way of thinking and the supporters of the standard had all the evidence to the contrary.
ASTM D 6754-02 specified a minimum thickness of 0.81 mm. When the first KEE roofing membrane was commercialized in 1979, the model building codes at the time required a minimum 0.8 mm for most forms of sheet roofing. This new standard clearly recognizes a properly formulated and engineered KEE membrane can perform or provide a design service life at 70 per cent of the 1.14-mm (0.045-in.) norm for PVC membranes produced according to the criteria in D 4434.
The permanence of the phased polymer structure, the coatings’ adhesion to the base fabric, and superior resistance to UV, chemical, and micro-biological attack are all attributes that have contributed to the historical performance of KEE membranes, and what could arguably be the most sustainable roofing membrane available.
Jerry Beall has been in the roofing industry for almost four decades, stemming from a 10-year chapter as a journeyman with Roofers’ Local #88, and then developing into work in technical service, commercial roofing sales, estimating, and project and technical management. As national sales and technical manager for FiberTite Roofing Systems by Seaman Corporation, he guides a nationwide team of sales, technical, and manufacturing representatives. Beall regularly makes presentations to audiences including members of the American Institute of Architects (AIA) and RCI International, along with roofing contractors and building owners. He can be contacted via e-mail at jbeall@seamancorp.com.