Sustainable paint index: A shift in architectural coatings
By Tony Margani
What happens when a new standard is introduced? Interested parties reassess what they are currently doing, compare models, and finally determine to stay the course and risk being left behind or resolve to stay current and realize the benefits. This process is almost reactionary because what is considered best practices may no longer be. This is the behavioural connection at which developers, builders, and painters (stakeholders) are crafting the green built environment.
Focusing on consumption profiles, dematerialization, and product optimization as it affects paint in the new construction and maintenance markets, this article delves into topics that do not come from the industry’s customary marketing perspective (e.g. reviewing the hottest colours and the emotions they evoke). It will come from a position of tangible, unprecedented environmental, social, and governance (ESG) through sustainable property technology developed and deployed from Toronto that is changing the way the world thinks about paint’s relationship to the environment.
What is the Sustainable Paint Index (SPI)?
A SPI is a paint system of balanced incentives in both economy and environment, inherently and quantifiably linked to its use.
Anybody keeping current on business news knows since 2008 Walmart, the world’s largest retailer, has publicly committed to develop and implement what they call “The Sustainability Insight System” or THESIS. What this means is Walmart will optimize the life cycle of each product they sell towards zero waste and ensure the suppliers of these items will be held to the utmost “green” standard as measured by The Sustainability Consortium (TSC), a group funded in part by Walmart. This will then allow the consumer instant access to data at point of purchase on how well a particular item performs.
By this, all consumer types are empowered at point of sale and being eco-friendly becomes profitable as the manufacturer transfers the burden of the associated costs into its purview and ties it to an economic incentive that drives the purchasing process. Consumers do not want to nor should they pay more for eco-friendly products; therefore sustainable paint must completely adapt to their habits. This tiny little expression of self-interest by all stakeholders will recalibrate the consumption patterns of the world’s resources through the paint industry’s supply value chain and come to characterize the SPI for its largest customer—construction.
It is only when all stakeholders financially benefit, the green built environment will skyrocket. It is the way of the future.
Paint is not thought of except when the chore of having to do it presents itself, but this business has been quietly coating the world’s walls and surfaces for generations with comparatively little innovation since the introduction of water-based/latex paints in the 1950s. Paint is not popular compared to consumer electronics, electric cars, or the current resurgence in space travel and artificial intelligence (AI), and yet there is almost nothing that is not coated one way or another—including the SpaceX rocket. It is a sleeping giant of an industry. In some ways, it is also stuck in the environmental dark ages as one of the most underregulated and dirtiest in the world with estimates from the American Coatings Association (ACA) of upwards 16 per cent waste generation from all virgin production as standard practice.
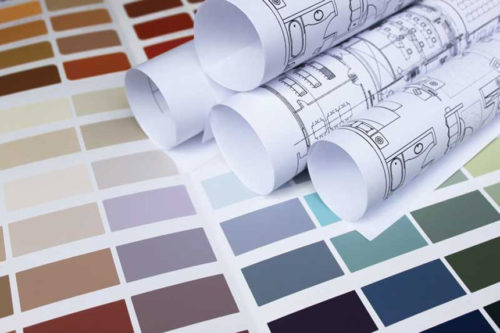
Through the desire to decorate, the need to protect and maintain newly built and older surfaces, plus the capacity to service a broad range of market sectors, the global coatings conglomerates have become exceedingly wealthy. Their most consumptive customer is new construction and maintenance, particularly commercial/industrial real estate followed by residential communities in both high and low rise.
Purchasers today choose developments that raise their profile and developers/builders know it is smart and profitable to be at the forefront of introducing effective technology that reduces deficiencies and improves standards. This commitment speaks well for quality and long-term value and helps potential commercial and residential owners prefer developments that meet their economic and environmental objectives. Unfortunately, when it comes to paint, all stakeholders are unknowingly part of the problem.
Waste is the original pollution
The annual North American paint waste system quietly generates upwards of 860 million L (227 million gal) annually, excluding containers which are never used or recycled; they just get dumped into the water table. Not to mention all other supply chain excesses just to produce this waste. Current efforts to handle the reuse and recycling infrastructure are costly and reactionary and only recapture 0.3 per cent annually. Further consider the out-of-control eco-footprint that generates the systemic hyper-problem in CO2, and it becomes clear that even today’s best methods to manage the image of consumer paint waste do not provide a reprieve from the flow.
Stopping habitual waste means preventing it at its source. Properly innovated paint products must reduce material, time, and labour costs to their absolute minimum—simultaneously preventing waste while maintaining sufficient consumption that yields desired results. This allows for a transparent, optimized response for paint in the new construction phase and continuously through the maintenance/remodelling lifespan. The most environmentally friendly paint must always be the one used the least.
With this in mind, proposing something radically fundamental is needed: A fully optimized, sustainable and quantifiable paint system which never requires a primer or second coat to achieve a finished result over any surface. This delivers labour, time, and material cost savings of at least 66 per cent to the developer/builder and painter, plus prevents 66 per cent of life-cycle wastes and excesses in raw material extraction, CO2, transport, energy, and production. This system satisfies five UN Sustainability Development Goals (9, 11, 12, 13, 14)1 right now and not in 2030 or later. This rewards all stakeholders with an effortless, tangible, built-in eco-incentive that is good for the wallet and is in balance with nature.
If the construction industry is to break its casual obligation to paint sustainability, it must lead the market. By reassessing what they are currently doing, there will be an understanding, then a choice toward self-interest, profitability, and a movement away from wasteful outdated standards that dictate how paint is consumed. Painting will become about incentive and measurable benefits that align with today’s environmental objectives. This is where consumer loyalties are moving, so this is where the SPI must exist.
Over the course of the last generation, construction industry experts in partnership with all levels of government have continued to move toward a green built environment. Understanding the challenges and opportunities in sustainable prop-tech, these key players sanction models of innovation. Current advancements clarify the need to better manage best practices, optimizing building materials with particular control over the cost, consumption and waste impact for every commercial/industrial unit, home, and condominium built.
As the developer/builder and painter seek to meet market requirements with minimum investment in material, time, and labour, an adoption of these advancements is slow as all known products, systems, and techniques are complex—significantly adding to costs. This has led to an instilled reliability on government incentives, subsidies, and green financing structures to even consider deployment.
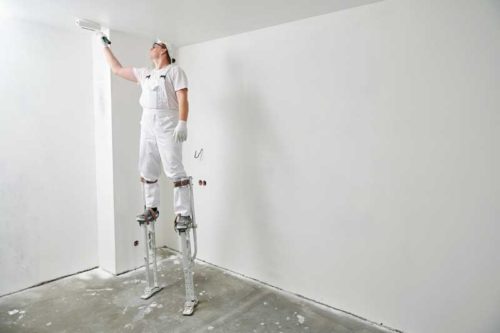
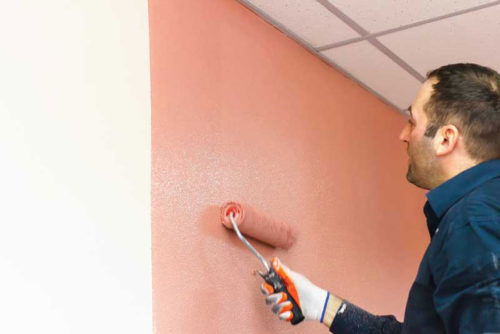
Thinking through the chronology of improvements in new construction through the notion of incentive, the industry has had to put up with a lot over the last 70 years (oil to latex, block brush to roller, roller to spray gun, plaster to drywall). However, through all the convoluted messaging with zero incentive from the paint industry today, there is something good that has come of it, namely that the public has been conditioned to understand that fewer coats make sense, even if they cannot buy products that achieve it.
Unlike green construction technologies which are costly to manufacture and complex to position into building processes, paint is inexpensive to produce by nature of its purpose and is adaptable. Since incentive and reduction are built into this novel technology system, the value proposition is significant as it streamlines processes and acts as a path of least resistance. Through the SPI, developers/builders and painters support a system that prevents maximum life-cycle wastes in raw material extraction and containers used for production; the most energy and CO2 friendly supply chain; and an unprecedented reduction in material, time, and labour required for equal square footage. There is no other green construction technology that makes such a commitment to the environment.
With some experts placing 80 per cent of the eco-footprint of paint coming from raw material extraction, most notably titanium dioxide (TiO2), and coupling that with the accepted notion that buildings have a big impact on the resources upon which they depend, the construction industry comes to consume more than one-third of all primary energy, two thirds of electricity, one-third of all raw materials along with a growing percentage of our freshwater. Making this sector the ideal candidate for resource conservation, dematerialization, and life-cycle waste prevention through the SPI.
As such, several key players within construction are making a commitment to sustainability, re-enforcing it as the way of the future. They recognize even higher initial costs are justified with an appropriate payback through reduced operating expenditures, increased building value and image. Realistically, however, they demand sustainable prop-tech that saves money while streamlining best practices. “Going green” must shift from being a cliche vague buzz phrase and become measurable.
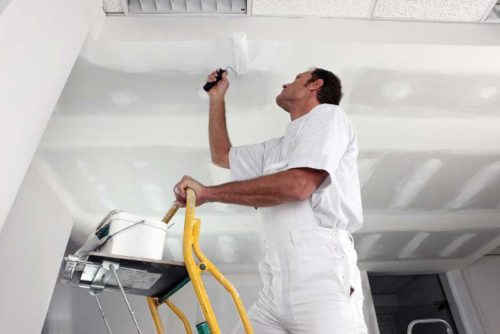
The popular environmental adage “Reduce, Reuse, Recycle” was meant to prohibit waste generation, but its catchy rhyme and good intention has not achieved much, at least in the world of paint. It is of no coincidence the first “R” is reduce and the last is recycle. It is obvious, if it is not bought, it does not get used; and if it does not get used then it cannot be wasted. However, the truth is, construction must buy and it habitually wastes; but this industry is not fully responsible because it needs to consume an excessive amount of paint to get the job done from all traditional misleading paint marketing strategies (e.g. paint and primer, one-coat colour collections, self-priming) and the massive wastes they quietly generate.
An effectively operating recovery and recycling model relies on access to and control over waste. However, the infrastructure has proven to be costly, complex, and tenuous. Since this model itself is reactionary and functions within the paradoxical rule of waste creation to be successful, it cannot prevent waste at its source while maintaining the required consumption.
It is an ever-increasing challenge and nobody is talking about it. Mainstream sustainability articles on paint usually have a brief vague mention of volatile organic compound (VOC), but this is benign of real purpose and substance.
This sense of duty in being responsible for the wastes generated is not new. Governments have what is called the Extended Producers Responsibility System (EPRS); but it is only a recommendation and not strictly followed by manufacturers. They are more concerned with trying to manage wastes from their products at point of purchase by leveraging every transaction across North America. Consumers might not know it, but they are subsidizing a system that creates paint waste.
Manufacturers have quietly established a consumer financed initiative and strategy1 with a built-in pricing structure that accommodates their costs and image of running the fledgling recapture and recycling systems that attempt to reclaim the wastes they generate. What is more, this does not include any fees when having to drive waste to the dump. Those are a lot of “Rs” but unfortunately, they are missing the only one that counts: reduce.
Paint waste is the last frontier in the green built environment conversation because it is tangible, visual, abundant, and out of control through too many inconsistent and questionable efficacies. Innovation through the SPI is the tactic to taming this leading edge. Construction in Canada must take back control of how it consumes paint and challenge all stakeholders towards this model within their own tier.
What is the business case for sustainability?
It is imperative the lead car at the advanced green arrow move like lightning, because it is only going to last so long, any sluggishness might make it or break it for the vehicles in behind. There are drivers that feel the same and there are drivers that feel the arrow is just for them.
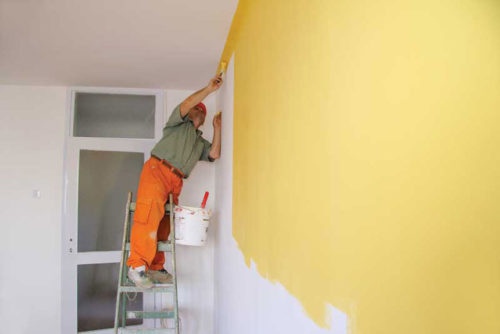
This article has made the case of a new standard for the developer/builder and painter by employing the concepts of incentive, self-interest, and sustainability as a single mutually beneficial economic system. This is expressed by the scenario above, where doing what’s best for the lead car and for the group behind is the only way forward. Stakeholders who selfishly soak in all the advantages and conveniences of the arrow, by habit or intentionally to maximize their own benefits, will only do it for so long before they start to realize that to succeed in the new sustainable economy, they need all the cars (stakeholders) lined up to make the turn with them; shift toward the environmental direction needed.
Achieving any real measure of success for sustainability in the new construction and maintenance markets depends on broad acceptance using practical incentives; and the only way to accomplish this is through radical technology innovation. Advancing the green built environment must become more than a few construction leaders quickly maneuvering to accommodate everybody else, it must become an orchestrated affair where each vehicle in the turning lane thinks, feels, and acts like it is the lead car.
Everybody must want to be the lead car and with incentive through the SPI, all stakeholders can redefine how they consume paints and coatings and prevent the waste they generate with real measurable benefits.
When this concept is fully digested, there is no going back to traditional paint systems as the incentives are too great for everybody involved. It remains accurate that only when all stakeholders financially benefit the green built environment will skyrocket.
The global conversation on the health and ESG of every industry sector has a specific dialogue, being refined by how best to achieve their respective sustainability metrics. The paint industry and its largest client, the new construction and maintenance markets, must reach theirs.
Conclusion
The SPI volunteers a reduction of 66 per cent in production output, simplifying resource consumption and teasing out the excesses through the entire value chain. It also adapts to everything stakeholders have ever known about paint without any new education or compromise to the desired result. Finally, it endows them control to get beyond the reality of supporting traditional outdated systems that generate uncontrollable waste and then make them pay for it.
The relentless incentives in the SPI will continue to welcome more stakeholders into the conversation on how to be smarter about resources as it affects paint consumption patterns. Striking a new balance by shifting the incentive from the pockets of the manufacturers to its customers, recalibrating paint’s relationship with new construction in Canada, and aligning it with today’s standard for the environment through its purchasers.
The idea of paint must adapt to manage consumption. It is imperative the construction industry lead in this initiative, instigating a fundamental shift in architectural coatings.
Notes
1 Product Care, the recycling programs in Canada, was started by and financed by all paint and coatings manufacturers in the country. To learn more, visit www.productcare.org/about/. Fees are built into the products manufacturers sell, thereby passing on their responsibility to the consumer to finance. Review the “eco fees” section to learn more, www.productcare.org/about/#about-epr-program-funding-and-eco-fees.
The Sustainable Paint Index (SPI) is a paint system of balanced incentives in both economy and environment, inherently and quantifiably linked to its use.
Over the course of the last generation, construction industry experts in partnership with all levels of government have continued to move toward a green built environment. Understanding the challenges and opportunities in sustainable prop-tech, these key players sanction models of innovation.
Consumers do not want to nor should they pay more for eco-friendly products; therefore sustainable paint must completely adapt to their habits.
The paint business has been quietly coating the world’s walls and surfaces for generations with comparatively little innovation since the introduction of water-based/latex paints in the 1950s.
Paint waste represents a critical issue in discussions about sustainable building environments due to its tangible, visible, prevalent nature and the lack of consistent and effective management strategies.