Sustainable cladding choice equates to high-performance building envelopes
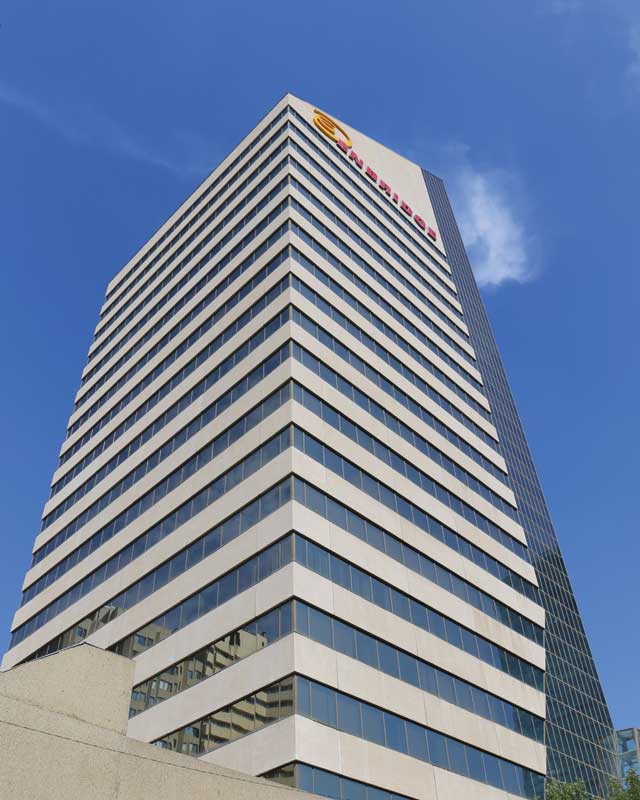
By Amanda Sinnige and Kevin Day
Exterior insulation and finish systems (EIFS) are in an ideal position to respond to the requirements of many of the sustainability programs becoming more prevalent in society. Indeed, there are specific features of these cladding assemblies that add to the value proposition in terms of sustainable construction. (This article’s co-author also explored EIFS’ long-term sustainability in the January 2015 issue of Construction Canada. “Exploring EIFS’ Long-term Sustainability,” by Kevin Day and Daniel Schlegel, can be read online here. The feature outlined the history of these assemblies, their adoption of drainage and secondary moisture control, and the small ecological footprint compared to many other cladding materials).
Sustainable aspects
To expand on the features of EIFS being a part of sustainable construction, one should consider the numerous variables related to the building lifecycle.
Long-term durability
The longer a cladding can last, the fewer resources are necessary to maintain the building’s service life. EIFS have a life expectancy of 50 years or more. (“Exterior Insulation Finish Systems: Designing EIFS (Clad Walls) for a Predictable Service Life,” by co-author Day (while at Morrison Hershfield) was part of the Proceeding of the Eighth Conference on Building Science and Technology, February 2001). Not only does the cladding have inherent long-term durability, but the continuous insulation (ci) also results in a reduction of potential condensation problems, as can happen with the thermal bridging intrinsic of other cladding systems. This also reduces the likelihood of maintenance or repair required to rectify condensation problems.
Energy efficiency
The building performance for space heating and cooling significantly improves with the use of EIFS as the cladding choice. In new construction, the most recent building and energy codes are becoming more demanding in terms of thermal performance. EIFS offer an easy solution to meet these requirements. In terms of retrofits, the assembly provides solutions to improve the energy performance of uninsulated or under-insulated buildings. The ci inherent in EIFS virtually eliminates thermal bridging, increasing the energy-related performance of the building.
Additionally, the thickness of insulation can be adjusted according to specified requirements, including where more aggressive energy efficiency is required (such as may be the case for a Leadership in Energy and Environmental Design [LEED] Platinum building). This adjustment can significantly reduce the need for heating and cooling, therefore, minimizing energy use.
Reuse
EIFS can be used to rehabilitate existing buildings clad with other materials without having to remove and dispose of the original cladding (i.e. no waste, no recycling, and no landfill usage).
When necessary, components of the system can be recycled. For example, the expanded polystyrene (EPS) insulation can be separated and ground down to become filler in recycled content EPS, or filler in soil to promote stabilization. Lamina and mesh coatings can be separated and ground down to promote stabilization in soil, or used as filler in geotechnical applications.
EIFS components are chemically inert and will not harm the environment when they are disposed.
Resource conservation
Due to their lightweight nature compared to other cladding systems, such as brick or tilt-up concrete, EIFS do not impose a significant dead load on the building structure, allowing for significant savings in structural materials.
Considering the “value proposition”
Renowned building scientist Ted Kesik’s white paper, “The Value Proposition of EIFS,” outlines all the performance characteristics of a wall, and evaluates EIFS’ performance in each of the categories. (“The Value Proposition of EIFS” was published by the University of Toronto in April 2012). It is interesting to note EIFS, as a cladding, can achieve all these requirements (provided there is a structurally sound substrate). Kesik rated the performance of EIFS strongly in all 11 categories except for fire resistance, durability, and questionably esthetics. However, EIFS perform well when designed as part of a high-performance building envelope.
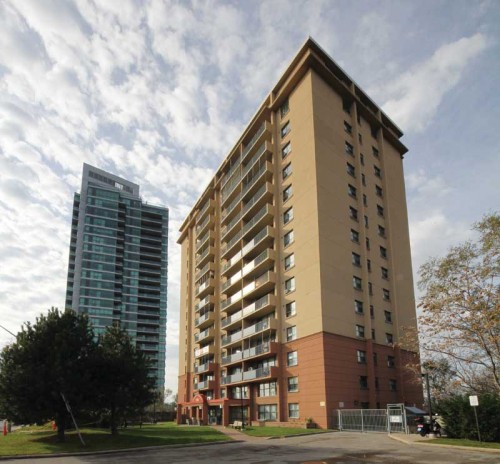
1. A system that will meet the requirements of Canadian Construction Materials Centre (CCMC) and/or CAN ULC S716.1, Standard for Exterior Insulation Finish Systems (EIFS)–Materials and Systems, should be specified. This standard deals with the full breadth of exposure parameters, such as:
- sunlight/ultraviolet (UV);
- salt (maritime);
- high humidity (mildew resistance);
- rain;
- tensile bond;
- moisture management; and
- hygrothermal durability.
2. Fire resistance can be validated by meeting the applicable building code requirements for protection of foam plastics. On lot lines where unprotected openings are limited to 10 per cent or less, non-combustible insulation is likely required (i.e. semi-rigid mineral fibre).
3. Impact resistance can be augmented with the proper design, supply, and quality control of the reinforcing mesh, to minimize nuisance impact damage.
4. The assembly’s esthetics can be maintained by eliminating impact damage, keeping lightly reinforced systems away from pedestrian and maintenance contact, and increasing reinforcement. The placement of finish coats can also affect the ‘look’ of the systems. It is important the placement of finish coats respect exposure conditions by selecting appropriate colours for the climate conditions (e.g. hot pink in a maritime climate is not recommended), ensuring all rainwater is designed to deflect away from the wall, at parapets, roof/wall intersections, balconies, and window heads and sills, and avoiding placement of finishes at soft grading, landscaping, and garden planters (or else select colours/textures not affected by these conditions).