Streamlining construction with in-situ mock-ups
By Ibrahim El-Hajj
Common construction pitfalls include: critical time loss due to deficiencies or non-complying work; disputes between trades or project team as a result of communication shortfalls; conflicts between different building systems or cost overruns; and auditor claims or warranty issues.
If any of this resonates or brings back uncomfortable memories, it might be wise to reassess the strategy and consider the use of in-situ mock-ups.
Today, technology is advancing rapidly, and future buildings are expected to be even more sophisticated, presenting more challenges for designers and contractors alike. Factory manufactured, assembled components, and intricate infrastructure systems are overtaking traditional ones. Updated building codes, new composite materials/cladding systems, net-zero-energy green systems (by 2030), complex geometrical building configurations and heights are among the many new and ongoing challenges that need to be considered.
The best way to address these challenges is to ensure the contract documents of any project include:
- A project manual or specifications specifically created for the project.
- Convey the goals of design intent and how it is executed.
- Spell out the requirements for compliance in detail, to ensure the desired quality of construction is achieved.
Attention to detail, high level of quality, and precise execution are likely to be among the skill sets required to take on the journey to a successful project. The quality bar has been raised and so have the standards, codes, and expectations.
Project pyramid
The word quality can have multiple interpretations. Quality is often used to denote the degree of excellence of something and, as such, quality has different levels and grades. In fact, the term “quality” has a relative meaning. For example, what was fine and acceptable three years ago may not be satisfactory today under current standards, norms, or regulations.
A successful project establishes rapport with quality through the implementation of the requirements in the project manual/specifications. They define the term “quality” and prescribe how it is to be achieved by describing the role of quality control (QC) and quality assurance (QA) and in-situ mock-ups.
Quality control
By definition, in-situ mock-ups are typically full-size representations of proposed construction, often erected in place on the building by the same trade who will be doing the same work throughout the project. They may be later removed or incorporated as part of the final building.
Generally, these in-situ mock-ups are meant to demonstrate and identify irregularities, abnormalities, inconsistency, variation, unpredictability, conflict, deviation, dissimilarity, discrepancy, contradiction, changeability, distinction, variant, difference, struggle, aberration, and/or interface issues prior to full scale construction. They are meant to expose, and thereby avoid (or at least minimize) conflict during construction.
In other words, an in-situ mock-up is a way to discover potential errors, flaws and possible obstacles, unforeseen conditions, or concealed problems. Even a slightly minor error can have a devastating impact on the project schedule and outcome.
In-situ mock-ups, unlike the ones erected at the manufacturing facilities or third-party accredited laboratories, bear the distinctive signature of specific site conditions which is a unique characteristic that adds value to their purpose and objective.
In-situ mock-ups are needed to visualize how adjacent assemblies and systems will integrate—both functionally and esthetically. From this point of view, some mock-ups should be carefully selected to address the associated risk area where multiple trades come together to complete or accomplish the whole design as one integrated concept.
In-situ mock-ups can be applied to many building elements or components such as:
- Below-grade waterproofing systems
- Below-grade drainage systems
- Expansion joints, traffic topping
- Masonry, brick, exterior insulation and finish systems (EIFS), precast and metal cladding
- Sealants and other cladding
- Window and curtain wall systems
- Railing and guard systems
- Fire-rated wall, ceiling, roofing assemblies: shaft, chute, refuse chute, and plenums
- Firestopping assemblies, intumescent coatings, spray-applied fire resistive material, and critical junction details
- Some mechanical, electrical, and life safety systems
- Interior finishes, and many other building components
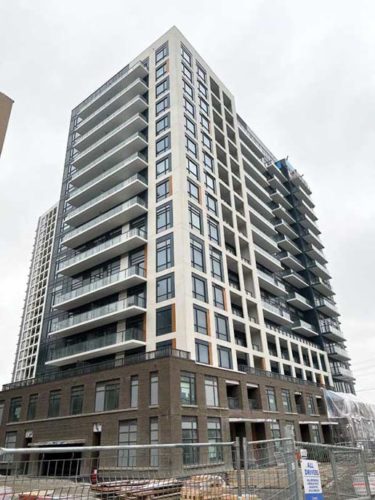
In-situ mock-up participants:
- Architect
- Project/construction manager
- Ownership representative
- Investor group/stakeholders’ representative
- QA consultant
- Field review consultant
- General contractor
- Sub-contractors
- Manufacturer
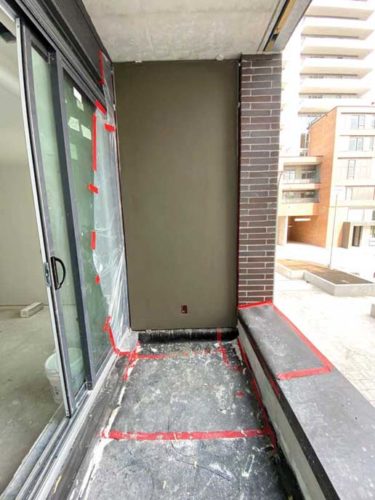
What project would an in-situ mock-up be useful in?
The need for in-situ mock-ups is driven by quality requirements and by the intent to “do it right” the first time and every time, on every level, suite or typical location.
In-situ mock-up is useful to clarify communication amongst all members of the project team by establishing the sequence of activities, critical path of various trade contractors, overlaps, and task dependencies.
They can be helpful for the architects to tweak their design, if necessary, or to address aspects that were not apparent during the early stage of design development, allowing changes which may better suit the project and site characteristics. These documents bring the construction and consultant teams together at every stage of the project to discuss the challenges facing the project and or opportunities for improvement.
An interactive platform
The in-situ mock-up is an opportunity to share thoughts, raise concerns, and express agreement; it provides a prospect to assess and define accuracy of interpretation and correctness of understanding of a given building element, system, or cladding.
It is also a platform for reviewing with all concerned parties, allowing for feedback and circulation, assessing, and analyzing, making the necessary modifications or adjustments seeking for approval, proceeding according to a clear and precise plan, before undertaking the full-scale installation.
In other words, it is an endorsement of the specifications, which call for an in-situ mock-up to be erected for most applications.
When in-situ mock-up procedures is adopted as part of the routine and logged into the project activities, project teams are ensuring the specified level of quality by following good architectural, engineering, and industry practices.
Limitations
In-situ mock-ups do however have certain limitations, but it varies on the type of the project and the delivery method being used. In certain projects, they may not be considered due to the nature of the project, such as civil engineering work, fast track delivery method, or design build.
Each mock-up will have its unique set of issues or challenges resulting from the specific site conditions and may not necessarily be applied on similar project applications due to numerous configurations and variables.
A lack of enforcement from the architect or the belief that in-situ mock-ups are an unnecessary exercise may cause some construction managers to doubt the value of in-situ mock-ups. Enforcing mock-up requirements in the specifications heavily depends on the architect, ownership, and project management’s vision and objective.
Benefits
The purpose for the mock-ups is to not disassemble or destroy the section of the work all relevant parties have agreed to, but rather to keep it as part of the accomplished work. This is, where possible, results in a saving of time and effort can be demonstrated. Evidence suggests keeping in-situ mock-ups as part of the building construction is a practical and useful strategy. One of the most substantial benefits of doing in-situ mock-ups is the comfort of following the project specifications.
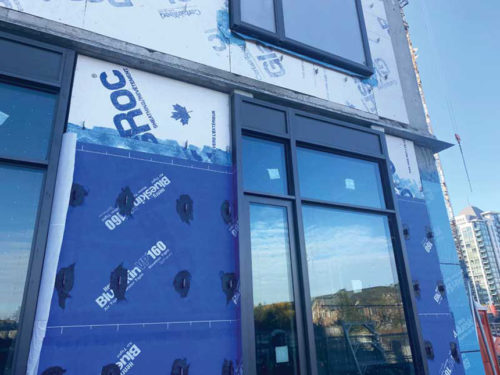
“Tarion, the organization that administers the Ontario New Home Warranties Plan Act, requires vendors to complete certain mock-ups as a requirement during the construction of Condominiums in the province of Ontario. Field Review Consultants (FRC) are retained by Vendors and follow an inspection protocol during construction, which is detailed in the guidance document, Registrar Bulletin 19 (RB19),” say Sandro Nevicato, technical manager, field review, common elements.
“RB19 details the risk areas where mock-ups are required as they are a critical part of minimizing risk for a project. Currently, we require field mock-ups for risk areas that lead to more frequent warranty claims, including exterior insulated finish system (EIFS), insulated concrete forms (ICF), and window wall systems. Tarion may require other mock-ups for new materials or systems being proposed. Ultimately, mock-ups help the vendor, builder, field review consultant, and design team in identifying potential challenges that are not always apparent in drawings, such as sequencing, configuration, and compatibility of materials. Resolving these challenges early can reduce the risk of future warranty issues.”
In addition to Tarion’s requirements, Pro-Demnity, the architects’ professional liability insurance company, introduced a new technical requirements schedule as of April 1, 2024. This schedule reiterates that full-scale mock-ups for precast assembly and window wall systems are also included in
their requirements.
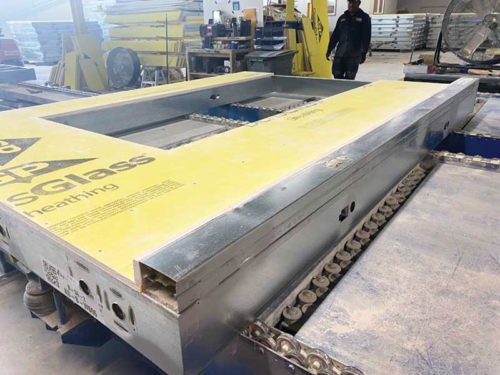
Misconceptions
There might be misconceptions about in-situ mock-ups in the construction industry (e.g. additional cost, redundant work, time consuming, etc). Some believe this approach is an outdated one and today’s tools or technology allow professionals to be more precise in modelling the outcome. Therefore, they become resistant due to the belief that a mock-up is a waste of time and effort.
Three-dimensional modelling can help virtually visualize and identify how the assemblies will interface and be seen among other cladding or within various patterns of building finishes. They may demonstrate a method or show variable scenarios of installation; however, they cannot identify issues that develop on site when trades try to co-ordinate their activities.
The evidence shows even though modelling may work, in most cases, they are set in a virtual environment which may not necessarily speak to the site-specific conditions. Good as they may be, they lack the required parameters to predict the exact or real outcome.
While the contract documents and specifications indicate the requirement for mock-ups, for the most part, it remains as a pledge in the hands of the architect, builder representative, and construction manager to enforce. In some situations, it seems there is even resistance to in-situ mock-up staging due to the misplaced belief of saving time and unnecessary work.
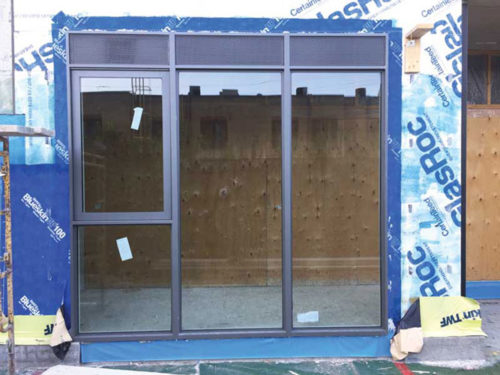
Potential consequences
While projects can go without mock-ups but who wants to multiply inaccuracies or errors in installation by the number of floors, suites, or typical locations throughout the project? Who would be responsible for potential difficulties that may be encountered such as discrepancies, remedial work, or even lawsuit? It is only a matter of time before such conditions are discovered based on symptoms of performance or as a result of auditing.
One drawback of omitting an in-situ mock-up is it may extend the schedule and overall project delivery; however, carrying out mock-ups may bring the project up to speed and enhance the chances of compliance to stay on budget.
Many dilemmas are possible but one worth mentioning is when the inappropriate method of installation of one system not only disturbs itself, but goes beyond to affect the other adjacent systems or components, their presentation, making them deviate from their initial concept.
Removing a defective portion of non-compliant work may not be a difficult assignment, but when it affects multi-storey building, it becomes a significant load at a significant cost to the project. Also, when dependent tasks or building components on the project get affected, it becomes clear how serious this would be in the midst of tight construction deadlines and busy delivery schedules. This is called the domino effect or chain reaction—when one improper event or installation causes a series of unexpected and dramatic results on a series of concurrent tasks construction activities.
Not to mention the hassle and coat caused by the technical errors and potential issues down the road, due to infringement to contract documents, poor performance, failure to comply, or deficiencies captured by the auditor. This may come at an exacerbated cost and consequential delays, where trades may not be around anymore and takes considerable time to bring them back, where mobilization cost get factored to the equation, and access may not be ready and most likely not welcome by the property management and occupants.
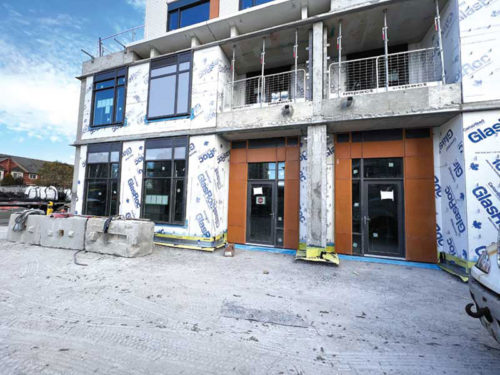
Optimum path
From a building science perspective, in-situ mock-ups are critical milestones in a project cycle to maintain quality and compliance.
This is what Dr. Gina Cody, the co-chancellor and namesake of Gina Cody School of Engineering and Computer Science at Concordia University had to say about mock-ups:
“In-situ mock-ups are necessary to enhance building durability and an essential part of construction methodology to meet the next generations of energy efficiency buildings.”
Certain builders understood the benefits of mock-ups and proceeded ahead of the game, building full in-situ mock-up suites at the outset of their projects. This aided them and their trades to trace and detect any potential issues early in the project. It allowed mechanical/electrical trades, drywall and finishing contractors, and others to assess their expectations. It also permitted the prime consultants to evaluate their design, receive feedback and obtain a glimpse of the completed end-product.
This handful of builders, who are tenacious, have considered full mock-ups, thought about quality a great deal in every step, and have concluded it is worthwhile to employ in-situ mock-ups in their projects.
Not only does taking on mock-ups save a great deal of annoyances, but it also helps maintain consistent quality. By doing so, goals are achieved with far greater ease and compliance, keeping projects on time and budget throughout the construction process.
An in-situ mock-up is a smart and simple way which may bring a positive effect and profound benefit on a project and can be seen as a solution to overcome obstacles in the construction field.
Ignoring the benefits of requiring in-situ mock-ups may shake up a project’s budget deadlines and milestones.