Steel framing and panelization chosen for mid-rise retirement residence

Panelization extends the speed and quality control advantages of mass production to the fabrication of complete assemblies. Loadbearing wall panels for this building were pre-built offsite and erected upon a 1301-m2 (14,000-sf) floorplate. Window openings are prefabricated as part of the pre-assembled panel, so as each storey is completed, windows can be installed.
Platform-type construction was used for upper levels of this project, meaning each floor acts as a working “platform” for the next storey.
Another potential benefit of the pre-assembled LSF construction method is its ability to have one construction contractor perform multiple functions. On the Seasons Retirement Community project, the same company erected the interior loadbearing steel-framed walls, installed the pre-assembled LSF wall panels on the outside, and installed the steel deck and the concrete for the composite floor.
Shane Mitchell of Glos Associates, the architect on the project, says the LSF system contributes to erecting a building quickly, in part because it allows panelizing walls in a plant before they are delivered to the site.
The design of the building required consideration of the character of the heritage area in which it was being constructed. The architects chose two types of materials: primarily masonry (brick and stone) for the base of the building, and LSF assemblies for the tower. The prominent scale of a building in that neighbourhood is two to three storeys. Since they were introducing an eight-storey building into the neighbourhood, Glos Associates wanted to “reflect the architecture and the scale of the street with a two-storey masonry podium.” Then, the tower rising from the podium could be a lighter, more modern material.
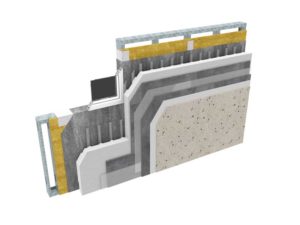
Image courtesy Durabond Products
This typology of building adapts well to stacked, prefabricated units. Panelization and LSF are often well suited for student residences, retirement homes, hotels, and condos if they have square footprints moving up vertically.
With this type of construction, the fabricator of the walls typically builds as much of the structure as possible offsite. This generally includes all of the light-gauge steel walls, both interior and exterior. The exterior walls will have the sheathing (or in this case, EIFS) already installed. One touted benefit of offsite factory built assemblies is the resulting higher level of quality assurance, due to the controlled working environment.
With this type of prefabricated LSF, lighter gauge steel can be employed on upper floors. Dino Fantin, construction manager for the wall assemblies supplier, explains how, in a 10-storey building, the lower floors would likely use 12-gauge steel for the loadbearing walls. Then walls could incorporate lighter gauge steel in the upper levels. Although the building materials are lighter with the higher floors, Fantin says the structure itself is still very secure. The composite floor, formed of concrete poured on top of the steel deck, functions like a beam on top of every wall. This makes the system very stiff. Stair towers and the elevator towers give the structure lateral support.
The composite floor system used in Seasons’ Cambridge facility is two-hour fire rated, designed for use in hotels, multistorey residential buildings, schools, and office buildings. This type of floor will accommodate a variety of wall systems, including lightweight steel framing, structural steel, masonry or poured concrete, insulated concrete forms, or wood framing construction.
A lightweight steel-framed structure may also be beneficial on projects having poor soil conditions, because this type of building is lighter than a conventional concrete building and the foundation will have to support less weight ( Information regarding structural design with lightweight steel framing is contained in the Canadian Standards Association (CSA) S136, North American Specification for the Design of Cold-Formed Steel Structural Members.).
New Manufacturer Certification for Cold-formed Steel (CFS) Framing |
The Canadian Sheet Steel Building Institute (CSSBI) and its members have recently established a third-party certification program for cold-formed steel (CFS) framing members being manufactured in Canada. The program will become a CSSBI membership requirement for manufacturers of cold-formed steel framing, effective September 30, 2018.
Under the new certification program, a participating manufacturer certifies the designated structural and non-structural cold-formed steel framing members it produces meet or exceed the relevant ASTM International (ASTM), Canadian Standards Association (CSA) and American Iron and Steel Institute (AISI) standard requirements referenced by the National Building Code of Canada (NBC). The certified products are validated by regular third-party inspections of the manufacturer’s production and quality control practices. The certification program applies to products manufactured for sale in Canada falling within the range of standard sizes specified by CSSBI. Complete details of the certification program can been found in the publication CSSBI 61-2018, Manufacturer Certification for Cold-Formed Steel Framing Member. To learn more about cold-formed steel framing, visit CSSBI. |
Jon Hiltz has been a journalist for 10 years and writes for a number of popular publications. He often covers politics, policy, real estate, construction, and agriculture.