Staying street SMART with project management
A practical example
Once the three data points have been determined, they can be plugged into the EV formulas. The ‘variances’ are the differences between your planned and actual and the ‘Performance Index’ is used for forecasting.
A positive variance for cost and schedule is favourable and a negative one is unfavourable; similarly, a Performance Index greater than 1 is favourable, and less than 1 is unfavorable. In the following example, then, the project is behind schedule and over-budget:
According to the schedule and cost baselines, a project involving excavating holes around a property’s perimeter was ‘planned’ as follows:
- dig 1000 holes over 50 days;
- steady rate of 20 holes per day;
- budgeted cost per hole is $30; and
- total project budget of $30,000.
At the end of Day 10, 150 holes were dug at a total actual cost of $5200.
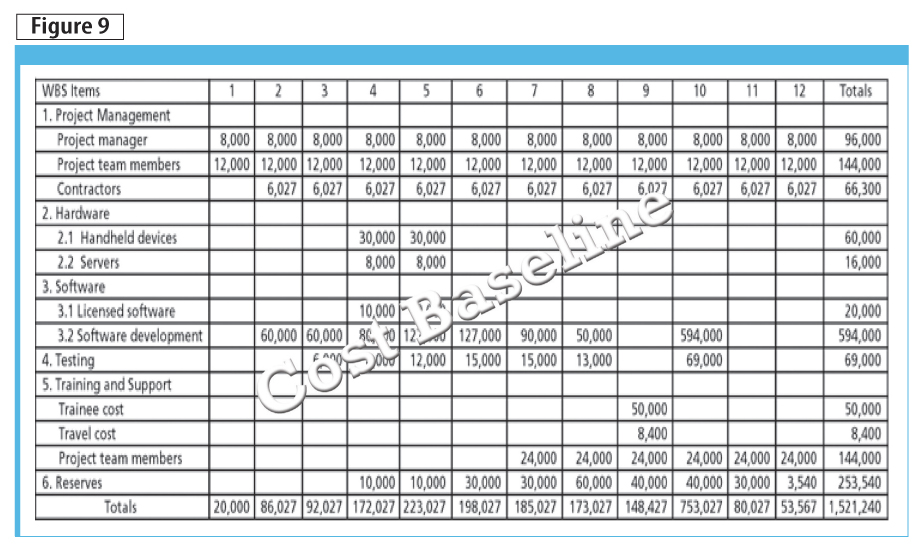
This means:
- PV = $6000 (10 days X 20 holes per day X $30 per hole [budget])
- EV = $4500 (150 holes X $30/hole [budget])
- SV = EV–PV = –$1500
- SPI = EV/PV = 0.75
- CV = EV–AC = $4500–$5200 = –$700
- CPI = EV/AC = –.87
Using the answers from the EV calculations, we can now ‘forecast’ what our schedule and budget will look like when the project is completed. Again, forecasting requires only basic calculations and no additional information. The terms used are:
- budget at completion (BAC): total ‘planned’ budget for the job;
- estimate at completion (EAC): total planned budget divided by Cost Performance Index (i.e. BAC/CPI);
- variance at completion (VAC): difference between budgeted cost and the estimate at completion (i.e. BAC–EAC); and
- schedule at completion: total planned schedule in days divided by Schedule Performance Index (i.e. original schedule/SPI).
Once you have completed the calculations for EV, you must than determine what type of ‘corrective action’ is required to bring your project schedule back on track. The two terms used are crashing and fast-tracking.
Crashing
This type of project schedule compression is performed for the purposes of decreasing the total period of time—essentially, it involves throwing additional resources at a job in the hope of completing it faster. However, this particular technique increases not only the project’s overall cost (i.e. hourly wages for additional employees), but also the risk or possibility for mistakes. It also raises the likelihood of issues arising between contractors who are now tripping over each other to finish their tasks.
Fast-tracking
The intent of fast-tracking is to take the entire schedule of a project and compress it into a smaller period. It is doing tasks in parallel that would normally be done in sequence—for example, having both electrical and HVAC contractors working at the same time, as opposed to installing all HVAC components and bringing in the electrical contractor after to tie it all in. Applying this technique may not increase the cost to the project, but it will again increase the risk.
Regardless of the option chosen, it is critical to remember any tasks along the ‘critical path’ (i.e. the sequence of activities taking up the most time to complete a project) are the ones with the greatest impact on the schedule.
Risk management
The process of construction is so much more interrelated than many other industries that when a minor event occurs, it disrupts everything else. Design/construction professionals must accept risk is a part of construction and identify and mitigate for those occurrences.
When this author speaks with contractors regarding risk, most assume she is referring to workplace safety standards. However, from maintaining the relationships with clients to protecting the ‘critical path,’ project management is about managing project risks.
Risks are often defined as either a ‘hazard’ or an ‘opportunity,’ but should be thought of as a variance or deviation from the approved plan. Risk planning is about reducing the likelihood that a certain risk event will occur, and/or about reducing the impact to the project when it takes place. It is planning for ‘what happens next.’ If an event were to occur on a project that was not planned for in advance, the likelihood of schedule delays or increased costs to the project are great.
Managers become responsible to come up with a solution ‘on the spot’, but what if the solution is a need for a specific resource or piece of equipment that is not easily accessible? If this risk was identified during planning and a risk response determined, than one could have prepared in advance, doing the necessary research or making the proper contacts available to when needed. Adapting the strategies/techniques outlined in this article, even if only a little at a time, can increase the success of not only one’s projects, but also one’s business.
Tina L. Vigneux, PMP, is a vice-president and program director for the Atocrates Centre of Project Sciences. She is also a professor at the School of Engineering and School of Skilled Trade at St. Clair College’s School of Skilled Trades in Windsor, Ont. Vigneux can be contacted via e-mail at tina.vigneux@atocrates.com.