Staying street SMART with project management
Step 3: Sequence activities/work items
Activity-sequencing is a necessary step when creating an accurate schedule. By taking the WBS work items, the relationships between them can be determined, and any dependencies classified. In other words, the tasks can be put in the order they are to be completed by answering what must be finished before another step can begin.
A ‘relationship’ is one task that directly relates to another (e.g. forms and footings, insulation and vapour retarders), while a ‘dependency’ can be logical or mandatory. In the first category, an example would be, “I have been doing this for X years, and I know I can have both of these trades on site working at the same time.” The second category means this must be completed before moving on—for example, an electrical inspection must be passed before the insulation and vapour retarders can be installed. The four types of dependencies are:
- Finish–Start: must finish Task A before starting Task B;
- Finish–Finish: must finish Task A before finishing Task B;
- Start–Start: once Task A has begun, Task B can begin; and
- Start–Finish: after Task A has started, Task B can be finished.
Determining dependencies is a technique most design/construction professionals already use when scheduling projects—it is the natural flow of the job.
Figure 3 displays a typical activity-sequencing chart. The one on the bottom uses the task names as opposed to ID numbers or letters. The network diagram (Figure 4) shows the relationships (arrows) between the main activities (rectangles) required to build a shed. One can flesh out the following information from the above diagram:
- the ‘cut wood’ activity can be carried out in parallel to the ‘build shed base’ and ‘supervise cement-hardening’ ones, assuming different teams working on each set of activities; and
- the dark arrows show what is known as the Critical Path (i.e. buy materials–build shed base–supervise cement-hardening–assemble shed).
The Critical Path is the sequence of activities taking up the most time to complete a project. Any delay in this sequence of activities impacts the overall timeframe, so one should carefully monitor all activities on this path.
Step 4: Create responsibility assignment matrix
A Responsibility Assignment Matrix (RAM) is a clear way to assign a resource, person, or organization to a specific task/work item. It is a simple matrix defining who is responsible for a given task, whose input is required, and who needs to check for completeness and accuracy (Figure 5).
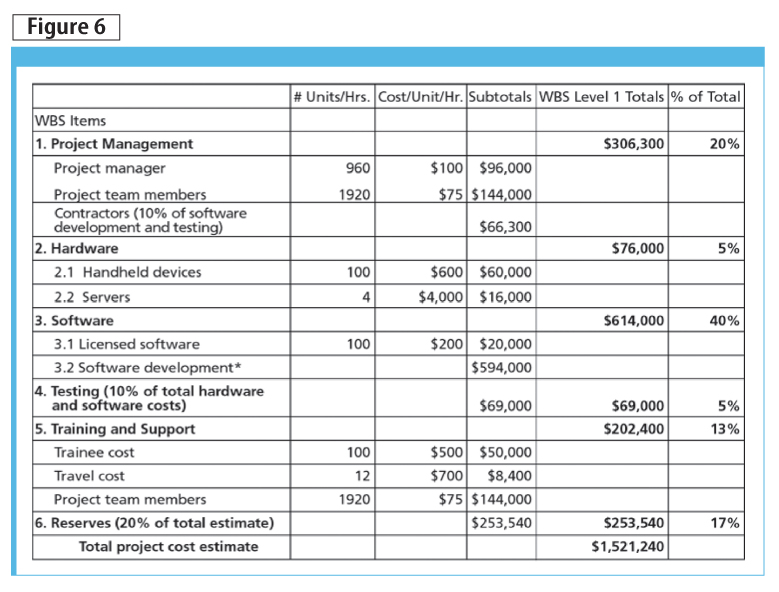
The RAM provides all installers/contractors with an outline of exactly what they, as well as others, are responsible for; it creates an overview for the entire job. Managers tend to want to oversee every step of the process, but this can consume time and smother individuals. One must trust them to take care of the tasks they are assigned, checking in at ‘milestones’ (i.e. significant point/event) while always being available for questions.
Step 5: Activity duration
Activity duration involves ‘estimating’ the time required in days to complete each task; from here, one can create a realistic total project schedule. The person who actually does a given task should be responsible for determining its duration. If you inaccurately document or use an unrealistic duration for a specific task, it causes issues during project execution and leads to discrepancies when calculating Earned Value (EV), as discussed later in this article.
When collecting information on duration, responses from subcontractors may vary drastically. For those instances, a simple Three-point Estimating Technique (PERT) formula can be used (Figure 6).
Step 6: Estimate cost/budget
Developing the budget requires referring back to the WBS work items, giving each task/work item or work package a ‘cost to complete.’ This could be an hourly wage per employee or the total contracted cost for a particular portion of the project (Figure 7). There are two types of cost-estimating techniques:
- top-down (analogous): using actual cost of previous, similar projects as the basis for estimating the cost of a job; and
- bottom-up: estimating individual work items or activities and summing them to get a project total.
There is progressive elaboration with this procedure—the farther one gets into a project, the more detailed one’s estimates become.