Sprayed Polyurethane Foam: Controlling airflow and water movement
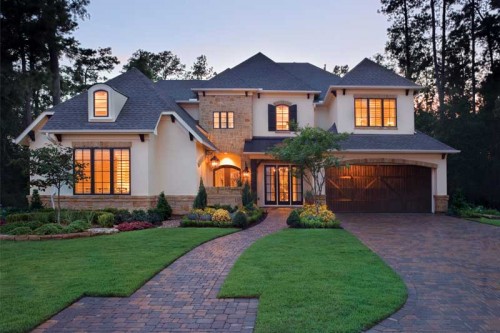
By Andrew Hunt and Monica Karamagi
Energy use, indoor air quality (IAQ), comfort, moisture intrusion, and durability are important considerations for design/construction professionals. To create a healthy, energy-efficient living space, a facility must be able to control airflow and water movement through the building envelope. The phrase “build tight, ventilate right” is used by building science experts to express the recommended building approach. One way to help address these concerns is through the use of sprayed polyurethane foam (SPF) insulation or other materials with similar properties.
In residential and commercial construction (both new and retrofit), the building envelope should be the first thing architects and builders consider when trying to create a more energy-efficient, durable, and healthy living environment. It is the ‘shell’ protecting the structure from water intrusion and uncontrolled air movement between conditioned and unconditioned spaces.
The building envelope must be complete, sealing all penetrations and gaps around the entire structure, as well as being durable and capable of controlling airflow. The key component to designing and installing a complete and successful building envelope is the air barrier. This is the physical material used to block air from moving into the facility from the outside (i.e. infiltration), or conditioned air from escaping to the outside (i.e. exfiltration).
What is an air barrier?
In simple terms, an air barrier is a material (e.g. film, sheet, coating, or membrane) that controls or stops airflow from the outside of the building to the inside. It can be made from many different materials, but to be effective, it must be properly installed and provide a complete shield around all sides of the building. When installed in a structure, the air barrier material becomes part of an air barrier assembly, which combines with the building’s windows, doors, and other design features to form an air barrier system.
The primary objective of the system is to block the random air movement into and out of a building and its walls and roof assemblies. A facility with unchecked air movement can have a host of problems, including higher energy use and costs, water intrusion, moisture issues, and poor IAQ.
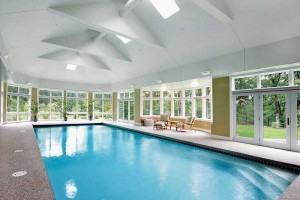
Images courtesy Huntsman
There are five key attributes to a well-designed and successfully installed air barrier system:
- be impermeable to airflow (airtightness);
- have sufficient durability over the building’s expected life, without being easily damaged or compromised during construction;
- provide continuous coverage around the building from the roofing to the below-grade structure (if any part of the air barrier system fails to control air movement, the entire system is considered a failure);
- have structural integrity; and
- resist wind loads, stack pressure, and other pressure loads without deforming or failing.
A well-constructed air barrier that satisfies these requirements will help control moisture in a building, reduce pollutants, improve air quality, and save energy and money on heating and cooling costs.
Improving IAQ
Uncontrolled air movement between unconditioned and conditioned building spaces can lead to indoor air quality issues. As air moves from unconditioned spaces (e.g. attics, crawlspaces, utility rooms, attached garages, and the exterior), it can transfer dust, allergens, pollutants, exhaust fumes, and chemicals directly into the interior environment. When these pollutants enter the common breathing space, they can create a host of issues for occupants, including:
- eye, nose, and throat irritation;
- headaches;
- fatigue; and
- dizziness.
While these ailments may be short-term, continual exposure to indoor air pollutants have the potential for chronic health effects.
In a home, controlling air movement from an attached garage to the living space is critical. Exhaust fumes from cars contain many known pollutants, including carbon monoxide (CO). Often, a garage will contain gasoline, pesticides, paints, and cleaning products, which can release toxic chemicals that must be kept from the living environment. An improperly installed or insufficient air barrier between the attached garage and the living area can be a serious concern for occupants, and is a National Building Code of Canada (NBC) violation.
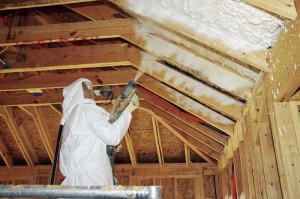
IAQ can also be compromised by the presence of excessive water vapour. Moisture moves into and out of the home either as a liquid or as water vapour. While plumbing leaks, wind-driven rain, or minor flooding may be dramatic, some water damage in homes is caused by vapour due to uncontrolled air movement.
Exfiltration in colder climates poses a problem for IAQ. Warmed interior air will often be more humid than cold exterior air, and as the humid air passes through the walls, moisture condenses on the inside of exterior walls. Humidity from cooking, laundry, and simply breathing can create large amounts of moisture, which can collect in wall cavities and unconditioned spaces. Once there, it can condense and cause damage to the insulation. Excessive water in framing members can also lead to rot, compromising structural integrity.
Standing water or water-damaged framing members and insulation can also quickly result in mould and bacteria growth. This is of special concern because spores in the air can result in headaches, breathing difficulties, allergic reactions, and aggravated asthma symptoms.
Reducing heating and cooling costs
According to Natural Resources Canada (NRCan), “air leakage represents 25 to 40 per cent of the heat lost from an older home.” To create comfortable work and living environments for occupants, and to reduce heating and cooling costs, a building should be insulated and air-sealed. However, an improperly installed, poorly sealed, or incomplete air barrier can effectively negate insulation and other energy-saving devices. Even small gaps or holes in the air barrier allow unconditioned air to move freely throughout, making the space uncomfortable.
The amount of airflow migrating from inside the home to the outside can be quantified in terms of natural air changes per hour (NACH). A NACH rating of 1 means the home’s total volume of air is replaced with outside air over the course of an hour. For example, a typical existing North American home can have a NACH rate of 0.5 to 1. This means every one to two hours, the entire air volume within the home is exchanged with air from the outside. Every bit of air entering through infiltration must be heated or cooled to keep the building at the thermostatic set point, making leaky structures expensive to heat and cool.
There are many advantages of controlling air infiltration and exfiltration. The primary benefit is energy costs can be greatly reduced by lowering thermal transfer between the home’s inside and outside. This can provide healthier IAQ by decreasing the amount of pollutants and toxins entering the living space, and also lessen the chance of structural damage to the building through moisture damage.
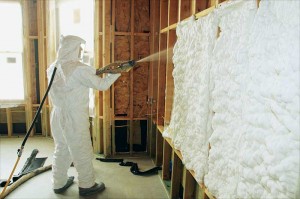
Successful design and installation
When properly installed, an air barrier should reduce or stop air leakage and movement caused by wind, stack effect, and air pressures from mechanical equipment and ventilation units. To successfully create an air barrier, a combination of components and materials must be properly and continuously assembled around the entire building envelope.
There are several air barrier materials commonly used today in residential and commercial construction. These include:
- gypsum wallboard;
- structural sheathing;
- polyethylene film;
- house wrap;
- self-adhered membranes; and
- SPF insulation.
Each of these can reduce airflow, but will have varying results depending on the air barrier assembly’s design and installation. Some assemblies use a combination of these materials.