Sprayed Polyurethane Foam: Controlling airflow and water movement
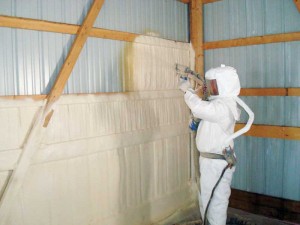
To create a successful air barrier assembly, one material must be selected as the main air barrier, and then be continuously connected around the facility. Often, finished surfaces or structural materials like drywall, sheathing, and decking will be specified. This can be convenient for builders because the facing materials of ceilings, walls, and floors have to be installed anyway. Without a deliberate focus on designing and installing a complete air barrier around the entire structure, gaps and holes are inevitable.
It is important to note a material’s permeance is simply a measurement of the air migrating through the air barrier. Gaps, spaces, or holes around the air barrier that result in infiltration and exfiltration destroy its effectiveness. To reduce the amount of uncontrolled air flowing through a building, the air barrier must be part of a continuous assembly. There are many ways to construct an air barrier assembly, and the type of material used often determines the most effective design.
The primary air barrier material or system can be located anywhere within the building enclosure––near the interior, near the exterior, or in between. This choice can be made irrespective of climate. The exception is when the air barrier material is also a vapour retarder, which is the case with certain types of SPF and numerous fluid-applied and peel-and-stick air barrier materials. If the material is also a vapour retarder, it should be located on the insulation’s warm side.
Air barrier materials
Air barrier materials are tested for their air permeance, or the volume of air passing through the material under given conditions. Testing is done according to standards established by ASTM, which creates standards for air barrier materials and assemblies, along with whole building performance testing. The lower the permeance, the better the material or assembly at blocking airflow.
ASTM E2178, Standard Test Method for Air Permeance of Building Materials, is the test method for determining air permeance of building materials. The industry-accepted baseline for an effective air barrier material is not to exceed 0.02 L/(s•m2) @ 75 Pa (0.004 cfm/sf @ 1.57 psf).
In ASTM E2357-05, Standard Test Method for Determining Air Leakage of Air Barrier Assemblies, wall, roof, window, and door assemblies are put through a test series to measure the volume of air passing through them. The industry-accepted baseline for an effective air barrier assembly is not to exceed 0.2 L/(s•m2) @ 75 Pa (0.04 cfm/sf @ 1.57 psf)—this is 10 times the limit for air barrier materials.
Lastly, whole-building performance testing may be done using a blower door test. In this test, the structure is either pressurized or depressurized to a standard pressure using fans. The larger the airflow required through the fans to achieve the standard pressure, the leakier the building envelope.
Gypsum drywall and plywood
Rigid building materials—such as gypsum drywall and plywood––are sometimes selected as the primary air barrier material due to their relative low cost and familiarity. An unpainted, 13-mm (½-in.) sheet of gypsum wall board has an air permeance rating of 0.002 L/(s•m2) @ 75 Pa (0.004 cfm/sf @ 1.57 psf)—the maximum allowable amount of leakage an air barrier material can have. (For more information, see “Understanding Air Barriers” by Joseph Lstiburek, PhD, P.Eng., FASHRAE. Visit www.inhomesprayfoam.com/uploads/6/8/7/1/6871103/2-understanding_air_barriers_-_all_color.pdf). Gypsum often fails, however, as the primary air barrier material because of the difficulty and time to create a continuous air barrier. A system called the airtight drywall approach (ADA) requires joints between the gypsum board and connected assemblies and materials be sealed with gaskets. While this system works as an air barrier, it can be technically challenging to install.
Building wraps
One of the most common kinds of air barrier material is building wrap. This is usually made of fibrous-spun polyolefin plastic with additional materials woven in to increase strength and durability. A building wrap is delivered to the construction site in large rolls and attached to the structure using mechanical fasteners like staples. The material, once applied to the facility’s frame, is sealed using tape between each seam. Depending on the manufacturer, style, and material quality, building wraps can be effective water barriers, especially against wind-driven rain. However, they are less successful as an air barrier.
If unsupported on both sides, as is the case with a brick cavity wall, a building wrap can be challenged by negative wind loads, which can rupture the fabric or tear at the mechanical fasteners. When evaluated by the basic criteria for a successful air barrier, a building wrap is not the best choice as the primary material. These products can be easily damaged during construction, are not completely impermeable to airflow, and will be effective only as long as the adhesive on the tape used to seal joints and seams is maintained.
Polyethylene sheets
Similar to a building wrap, some building contractors use a single polyethylene sheet as an air barrier. Installed on the wall assembly interior, the polyethylene sheet is usually stapled to the wooden framing members and rests against fibreglass batt insulation. Although polyethylene has one of the lowest air permeable ratings—about 0.005 L/(s•m2) @ 75 Pa (0.001 cfm/sf @ 1.57 psf)—it is almost impossible to successfully secure the material without holes, gaps, and tears around the fasteners, transitions, and wall penetrations.
Self-adhering sheets
Self-adhering, or ‘peel-and-stick,’ membrane sheets are another type of air barrier material used in both residential and commercial construction. These large sheets of modified bituminous (mod-bit) material are usually made out of styrene-butadiene-styrene (SBS) rubberized asphalt that has been reinforced with a cross-laminated polyethylene. They are mostly impermeable to air, water, and water vapour.
Membrane sheets can provide a continuous air barrier and adhere well to most substrates. Sheet installation can be difficult, labour-intensive, and usually requires a skilled craftsman––particularly around penetrations and gaps. They must be properly supported across all voids or gaps in the wall structure to avoid undue stress. Additionally, care should be taken to follow the manufacturer’s instructions to minimize the chance of the sheets pulling away from the substrate material.
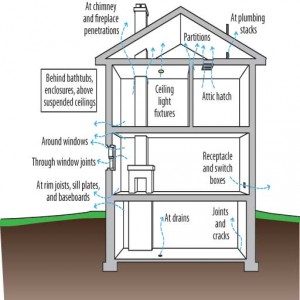
Spray-applied
Spray-applied or painted-on air barrier materials are liquid membranes made from synthetic rubbers or elastomeric bitumen. As the name implies, in this case the material is sprayed onto the exterior of the building substrate before drying in order to form a continuous air barrier. These spray-applied air barriers may require several coats to ensure that the proper thickness is being achieved once the material has dried.
When properly installed, the spray-on membranes can perform well. They are also faster to install and generally less expensive than peel-and-stick membranes. However, spray-applied air barriers have marginal bridging capabilities around small gaps and cracks in the wall assemblies.
SPF
Sprayed polyurethane foam insulation is made by reacting two liquid components to form a urethane foam. The resulting foam matrix expands to fill gaps and cracks. It is often used as a water, vapour, and air barrier material in the building assembly. SPF can be sprayed between framing members or over substrate material walls on the exterior. It can also be sprayed as a roofing material. It immediately adheres to the surface, expands 30 to 120 times it size, and then solidifies into a foam matrix that fills gaps, cracks, and other air penetration points.
There are two kinds of SPF used in construction today: closed-cell SPF (ccSPF)—32 kg/m3 (2 lb/cf)—and open-cell SPF (ocSPF)—8 kg/m3 (½ lb/cf). Besides having an almost zero air permeable rating, ccSPF has a high insulating property with an R-6 rating per inch. When properly installed, SPF can be an ideal air barrier material because it forms a continuous air barrier around penetrations like pipes, door assemblies, and windows. Additionally, ccSPF is structurally strong enough to withstand significant air pressures from inside and outside the structure, and is very durable during and after construction. In addition to thermal and air barrier performance, ccSPF offers unique attributes in stormy climates by adding structural strength. It can also be used in commercial roof replacement as a simple, effective way to replace an old roof, while adding energy and water durability performance.
Open-cell SPF insulation also has a low air permeability rating (at a thickness around 127 mm [5 in.]) and an R-value of 3.7 per inch. It offers different advantages than ccSPF. For example, open-cell SPF is vapour-open, allowing wall assemblies to dry in both directions. It also has stronger acoustical benefits, and can be less expensive. Having ocSPF installed within the stud cavities can successfully create high-performing air barrier assemblies. It is not applied to the exterior wall or in a cavity wall assembly as it will not withstand bulk water ingress.
Other
Other materials do not qualify as air barrier materials because they fail to stop an acceptable volume of air when put under pressure. These include:
- uncoated concrete block;
- asphalt impregnated fibreboard;
- expanded polystyrene (EPS) insulation board;
- perforated building wraps;
- cellulose spray-on insulation; and
- unfaced fibreglass batt insulation.