Specifying the right grout for the project
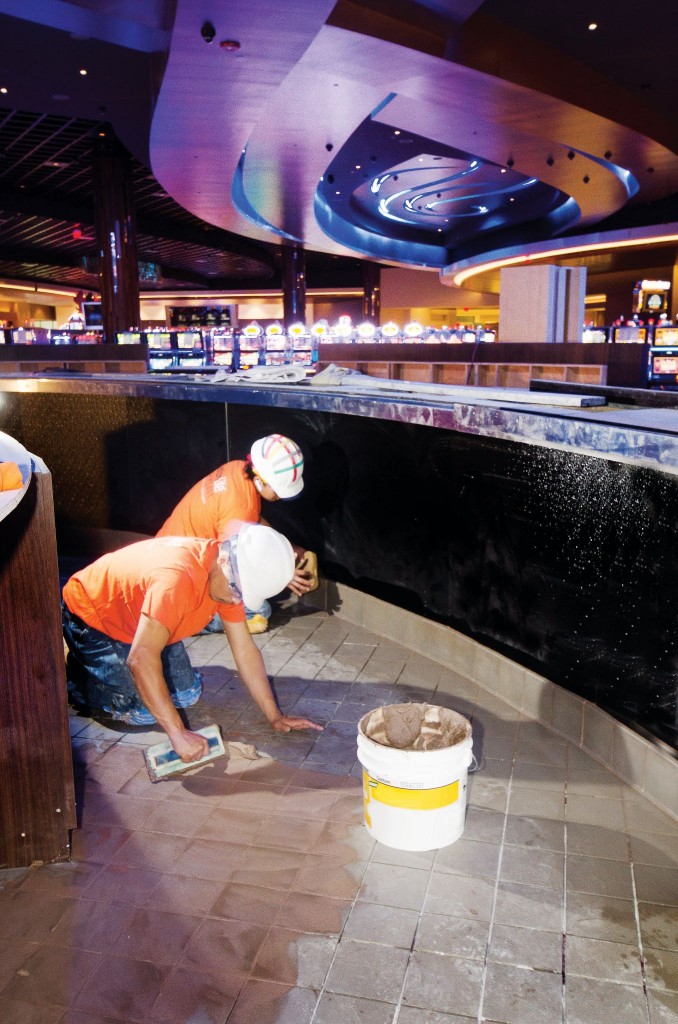
By Steve Taylor
The vast array of tile materials and grout colours makes tile design an exciting element of construction projects. However, this can also mean the grout type is relegated to an afterthought, instead of being planned as an integral part of the installation system.
Primarily, grout choice should be driven by the needs of a tile assembly, which is based on environment and usage. Some considerations for design professionals include:
- determining whether the tile and grout will be exposed to moisture and temperature fluctuations;
- potential damage from acidic materials and cleaning regimens; and
- owner expectations toward grout maintenance.
The demands that will be made of the tile will also affect the grout and how it will hold up as a part of the installation.
Choosing the right colour to match or contrast with the tile is only a secondary consideration once the critical specification of grout type has been made. Owners expect a tile assembly to be hard and durable, esthetically pleasing, and stain-resistant—and this includes the grout. These goals can be achieved by specifying the exact type of grout used in the installation in addition to the colour.
With advances in grout technology, there are many factors to consider when selecting the right grout. This article helps to explain the different types and how to choose the appropriate grout for specific projects. The Tile Council of North America (TCNA) and the Terrazzo, Tile, and Marble Association of Canada (TTMAC) define six types of grout based on the chemical composition and performance of each. The expected use of the tile assembly should ultimately determine which one must be specified.
Grout types
Standard cement grout is a general purpose grout traditionally used in various installation types. It is defined in the TCNA Handbook as a factory-prepared mixture of cement, fine aggregate, and other ingredients to produce a water-resistant, dense, uniformly-coloured material for joints that are 3.2 mm (1⁄8 in.) or less. The fine aggregate is generally replaced with clean, graded sand for joints greater than 3.2 mm. The coarser grout for larger joints is labelled as sanded grout and the finer-grade material suitable for joints less than 3.2 mm is referred to as non-sanded grout. Non-sanded is also preferred for highly polished tile or soft stone tiles easily scratched by sand. The performance of this type of grout is defined in American Nation Standards Institute (ANSI) in A118.6, Standard Cement Grouts for Tile Installations. Standard cement grout can be specified for interior, exterior, wet, dry, and even submerged applications.
Today, most of these grouts incorporate polymers to reduce water absorption and increase flexibility. The addition of polymer also reduces efflorescence and grout cracking. Since this grout is porous, it should be sealed regularly with a penetrating sealer to improve the stain resistance and durability. Typically, this general purpose grout has the lowest cost per pound.
High-performance cement grout should be specified wherever higher bond and flexural strength is desired or reduced water absorption is needed. This category of grout is defined by TCNA as a factory prepared mixture of cement and other ingredients, including a re-dispersible latex/polymer powder (to which water is added at the jobsite) or a liquid latex admixture (added at the jobsite in place of the water) designed for grout joints 3.2 mm (1⁄8 in.) or less. Generally clean, graded sand is added for grout joints greater than 3.2 mm. High-performance cement grout is defined by ANSI A118.7, Polymer-modified Tile Grouts for Tile Installations. In some installations, regular standard cement grout fails because it does not dry hard (compared to the tile surface). It can mottle or shade in the joints and cure with efflorescence on the grout’s surface.