Specifying the right grout for the project
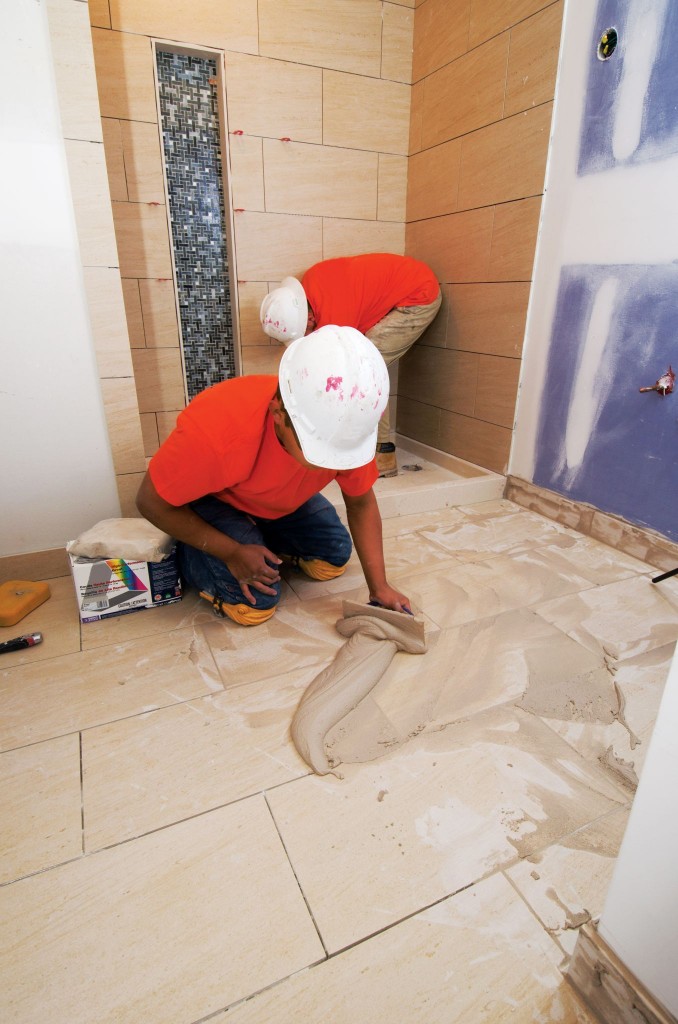
TCNA defines furan resin grout as a grout system consisting of furan resin and hardener portions. It is specialized and used in industrial and commercial installations that may require chemical resistance. Furan is a thermosetting polymer that can withstand continuous exposure to temperatures up to 176 C (350 F). As a grout, it is primarily used in applications such as dairies, that require resistance to routine exposure to organic acids (contained in milk products) and elevated temperatures. Furan is a reactive polymer-like epoxy. These grouts require special installation techniques and should not be attempted by a novice. They cannot be cleaned from the surface of the tile with water alone during the installation process. The performance of furan grout is defined in ANSI A118.5, Chemical-resistant Furan Mortars and Grouts for Tile Installation.
While furan is not widely used, many tile installation product manufacturers have developed improved epoxy grouts meeting the performance requirements of ANSI A118.5. These epoxy grouts have improved chemical resistance and will hold up when exposed to high temperatures. They are ideal for use in commercial kitchens routinely cleaned with steam and harsh chemical cleaning agents, including the no-rinse enzymatic cleaners.
The most recent addition to the grout selection in the TCNA Handbook is premixed polymer resin grout and is defined as a one-part liquid ready-to-use grout requiring no mixing with water. These easy-to-use grouts are generally a mixture of polymer (acrylic, silicone, or urethane), fine fillers, and water. They are pre-blended at the factory and can be applied to the joints between the installed tiles straight from the container; no mixing is required. While these premixed grouts are recognized by TCNA and the tile industry, they do not have an ANSI specification at this time and performance can vary from manufacturer to manufacturer. However, the pre-mixed or single component grouts have been specifically formulated to eliminate the issues seen with traditional cement and epoxy grouts. When fully dried, they can be hard, uniformly coloured, and completely stain resistant.
Installers also benefit from not having to use a full container of product. At the end of the day, they reseal the lid for the next day or the next job. Traditional cement and epoxy will harden in the mixing container and need to be disposed of the next day. This also reduces waste in the field. Premixed grouts are easy to spread and will completely fill the joints between the tiles. The grout can be used in most applications where a cement or epoxy grout is used. While premixed grout may be twice the cost of a high-performance cement grout, it is much less than an epoxy grout, and may not require the use of a grout sealer.
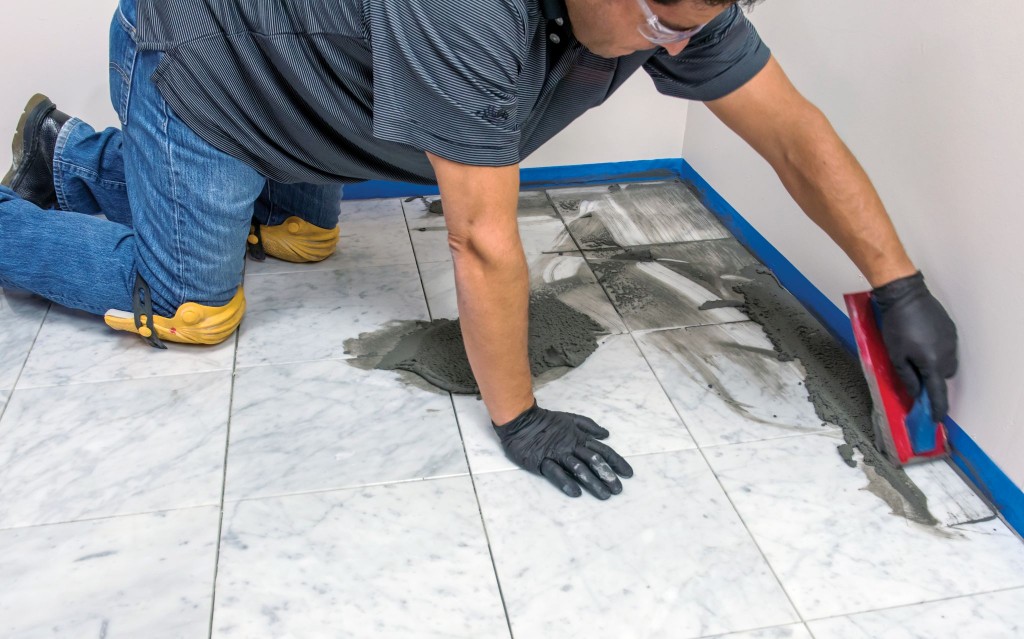
Caulking movement joints
While caulks and sealant are not classified as a grout, they do fill the movement joints between tiles in a correctly installed tile assembly. They are defined in the TCNA Handbook as suitable sealants/caulks that include silicone-, urethane-, and polysulfide-based materials. The sealant/caulk must meet the requirements of ASTM C-920, Standard Specification for Elastomeric Joint Sealants:
- Type S (single-component) or M (multi-component);
- Grade P (pourable) or NS (non-slump);
- Class 25 or 12.5 (i.e. allowable per cent movement); and
- Use T (traffic) or NT (non-traffic), M (use on mortar), and G (use on grout).
Sealant/caulk for use in traffic areas requires a shore hardness of 35 or greater.
The tile installation is not complete until the soft movement joints are properly installed. There is movement in every floor and wall, which can be caused by curing of cement/concrete surface, thermal changes, or even settling of the structure. Wherever movement is suspected, an elastomeric sealant or caulk should be installed in place of the rigid grouts previously described.