Specifying steel curtain walls with enduring beauty
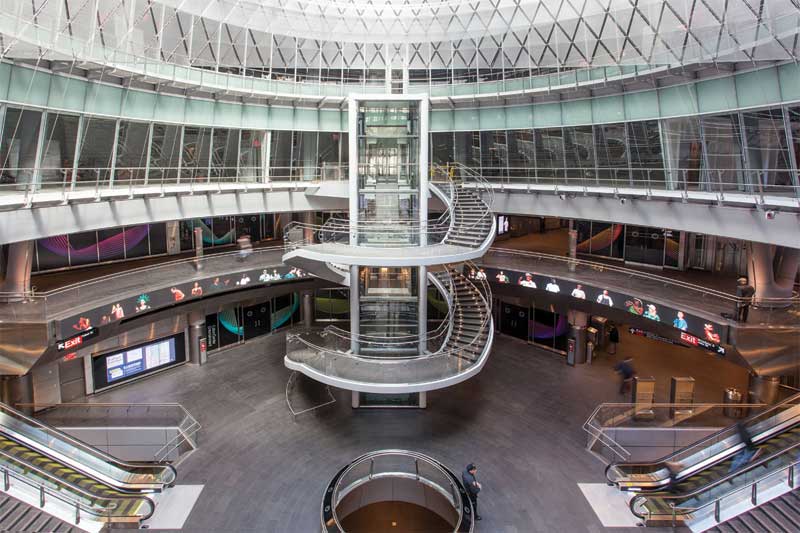
Corrosion
Steel rusts in the presence of moisture and oxygen. This is a seemingly irreconcilable performance obstacle since many curtain walls serve as the divider between interior and exterior spaces. Additionally, because steel frames do not require cladding or reinforcement to support expansive captured and non-captured curtain wall systems, properly sized frame members can act as structural elements. In many instances, they serve as the finished, exposed material, making their long-term beauty integral to the assembly’s overall look.
To help protect against rust and preserve the appearance of carbon steel members, double-sided pre-galvanization can be applied to the raw material (prior to forming and finishing). For example, the steel framing may be prefinished with liquid zinc and top-coated with a durable primer and finish colour to match virtually any design scheme. Generally, no special coatings beyond these are required to prevent corrosion.
To meet their specific project goals, design professionals can choose from various finishes, including powder coating and liquid-applied finishes specifically formulated for steel. Powder coating or liquid-applied finishes can be applied with proper cleaning or blasting, depending on the quality of the required finish. One caveat to note is typical finishes applied to aluminum, such as liquid-applied fluoropolymers, are not suitable for steel, as the chemical bond between raw materials and paint vary by material.
In some instances, design professionals may prefer steel’s strength, but desire stainless steel’s esthetic and enhanced corrosion resistance (i.e. for use with high-end storefronts or applications in coastal areas). To achieve this design intent, the exterior caps or interior back mullions can be made from stainless steel. Depending on the material thickness, suppliers can brush or bead-blast stainless steel finishes.
Finishes
Finishes are typically applied to stainless or carbon steel framing components after fabrication is complete and before installation. This eliminates potential for damage to the finish during sawing, welding, drilling, or final assembly. Additionally, it ensures minimal coatings are applied on rough edges that would otherwise be exposed during shipping to the jobsite.
Manufacturers can powder- or wet-coat steel systems using any coating suitable for architecturally exposed structural steel (AESS). While many fabricators and glaziers are familiar with liquid-applied paints common to aluminum, the downside is they can release from steel over an extended period, even with a primer. By comparison, the powder-coating process creates a tight adhesion.
During powder coating, the coating chemically reacts in the presence of heat. It produces long, densely cross-linked molecular chains that resist breakdown. The tight adhesion the reaction provides better protects against human and object impact, moisture, chemicals, ultraviolet (UV) light, and extreme weather conditions. However, as is the case with any finish material, significant surface abuse will result in wear over time.
Stainless steel profiles are generally passivated after fabrication to remove any steel particles that may form on the stainless during fabrication. Exposure to steel particles is common, as stainless steel fabrication typically takes place in the same factories where steel is processed. Passivation removes any non-stainless particles from the material surface and restores its natural oxidized finish, which may have been removed due to grinding, cutting, drilling, or welding during the fabrication process. If the stainless steel is not passivated, the carbon steel particles can form in the natural oxidation and later appear as rust flecks, calling into question whether the material is actually stainless.
Regardless of the selected finish, considering the following tips during the specification process can help ensure a quality steel frame finish:
- Specify a protective primer for carbon steel applications subject to harsh weather conditions, as well as those in areas subject to frequent use.
- Use frames with finishes designated for interior applications in interior applications only, as they do not provide adequate UV resistance for exterior applications.
- Use factory-finished frames (where the manufacturer or supplier applies the finish in a controlled, in-house environment prior to shipping to limit exposure of the steel to corrosion during transportation and installation), as opposed to a finish that is applied once the windows or curtain walls are exposed.