Specifying sound absorption and diffusion for optimal acoustic spaces
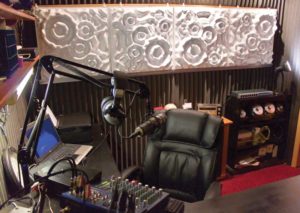
Electrical current is converted into electromagnetism which moves a loudspeaker, which in turn, creates varying pressures through the air as it moves. This energy is propagated from air particle to air particle in all directions—lessening in intensity as it travels away from the source, because it is spreading that energy out in accordance with the inverse square law, which states with every doubling of distance away from the sound source, the sound will be four times less intense. That is, until it hits something. Now, in the case of a frictional absorber, that “something” is generally a lightweight, porous material, which converts acoustic energy into heat energy. As acoustic energy hits a porous surface, it tries to move the material, and the resistance to moving is what causes acoustic energy to be converted into heat.
The materials one generally finds in frictional absorbers are fibreglass tile or boards of different densities, felts and other fibrous materials, or foam. These materials all have different properties in density by weight, fibre length, thickness, binder materials, rigidity, and pore size. These variables affect the acoustic resistance of absorbers and, as a result, their effectiveness at different frequencies.
A SUMMARY OF DEFINITIONS |
Absorption: The removal of acoustic energy from an environment. Diffuse field: First reflection points: Frictional absorber: Geometric diffusers: Mathematic diffusers: |
There is no frictional, broadband absorber which is “ruler-flat” in its frequency response throughout the entirety of the human hearing range. However, many of them are nominally effective through a wide range of frequencies—and mostly the higher frequencies. High frequency sounds are more effectively reduced by frictional absorbers than low-frequency sound—this goes back to the laws of energy conservation. High frequencies oscillate over a shorter wavelength than low frequencies, and when travelling at the same speed as low frequencies, attempt to oscillate the fibres in frictional absorbers faster than low frequencies. Low frequencies retain more energy over the long travel of the wavelength than high frequencies—and penetrate deeper into those frictional absorbers due to this fact.
This then leads the conversation to material thickness. With a frictional broadband absorber, the general rule is: the thicker it is, the better the low-frequency absorption. As stated above, high frequencies absorb quickly and easily, but the low frequencies retain energy and penetrate deeper into the frictional material; therefore, the solution to low frequencies is “just make it thicker.” When looking up absorption test results for a frictional absorber material, one will find many of them are tested repeatedly at different thicknesses. This is where one truly sees why they are called “broadband” absorbers—go thick enough and they can absorb almost everything.
Why not just exclusively use broadband absorbers? If they are “thick enough,” can they not absorb almost everything? Firstly, “thick enough” is a broad term, pardon the pun. When a situation calls for thicknesses up to 914 mm (36 in.) deep or more to absorb the lower frequencies, broadband absorbers start to become impractical. Second, it is very rare for a space design to entail absorption of “everything.” Anechoic chambers which block outside sound and reflections do not make superb listening rooms—they are muffled and claustrophobic sounding. High frequencies will attenuate naturally, just by travelling through the air… and because they are also easily absorbed. An apparent low-frequency buildup remains due to the imbalance in the absorption rate of the various frequencies, resulting in a bass-heavy environment.