Specifying resinous flooring according to different chemistries
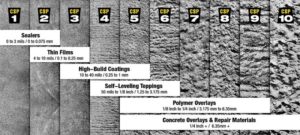
Surface preparation
The most important foundation of a resinous flooring system is the substrate it is being placed on. The most common substrate is a concrete slab which is steel troweled or has a “darby” finish. The top or “cap” of the concrete substrate is the weakest part of the slab. Even if the resinous system can penetrate through the top of the slab, the “cap” still may delaminate from the rest of the slab, which would still result in failure.
To prevent this from being a weak foundation of the flooring system, a concrete surface profile (CSP) must be specified. CSP was created by the International Concrete Repair Institute (ICRI) to help standardize concrete repair methods. This specification is on a one to 10 scale, with the higher number being the most aggressive profile for products that will be laid thicker than 6.4 mm (0.25 in.). This is important to specify correctly, based on the system, because the CSP may show through a thin film system, or the substrate may need to be patched to prevent the CSP from telegraphing through. If a substrate is not prepared well enough, the product applied may delaminate and fail.
How the CSP is achieved is typically up to the installer, as they are liable for the installation of a resinous flooring. Depending on the specified profile, project size, and specified system, an installer can choose a range of mechanical surface preparation techniques. One thing that must hold true is that all the substrates must be mechanically prepared to the specified profile. Commonly used equipment include: grinders, shot blasters, scarifiers, scrabelers, hammers, and sometimes even needle guns. Always check with the manufacturer’s recommendations and best practice, as some do specify the type of mechanical prep equipment that must be used.
Moisture mitigation
Moisture in a concrete substrate is always present because concrete requires cement and water to cure. Moisture testing is always recommended. A common practice is to begin moisture testing after a concrete slab has been conditioned for 28 days after being placed.
In addition to having water as part of the curing process, a concrete slab on grade acts like a sponge and will absorb moisture from the soil or ground. The best way to avoid needing a moisture mitigation remediation is to specify a vapour barrier (i.e. vapour retarder) under the concrete slab. Whether its residual moisture from the curing process or moisture being introduced from a slab being on grade, when this moisture is left unchecked, it can force the resinous system off the substrate, causing a failure.
When writing a specification, it is important to include the manufacturer’s recommended maximum moisture for the flooring or coating system being specified. This way, testing can be performed and if the recommended moisture content is surpassed, a mitigation solution from the specified manufacturer can be used first. There are many types of moisture mitigation solutions that will vary from each manufacturer and by the chemistry being specified.
The two most common testing methods to test for moisture content are calcium chloride and relative humidity (RH) probe/metre. Calcium chloride results are reported in a unique unit,
kg/93 m2/24 hr (lbs/1000 sf/24 hr), while RH probe/metre provide a humidity reading as a percentage. Calcium chloride’s unit provides a correlation to the amount of moisture coming through the slab, and RH probe/metre gives a reading of moisture inside the slab at a 40 per cent depth. ASTM International standards for the two testing methods are ASTM F1869, Standard Test Method for Measuring Moisture Vapor Emission Rate of Concrete Subfloor Using Anhydrous Calcium Chloride, and ASTM F2170, Standard Test Method for Determining Relative Humidity in Concrete Floor Slabs Using in situ Probes.
Calcium chloride testing has been in use since the 1950s and has an advantage of providing a quantitative value to the amount of moisture that is actually reaching the slab. RH probe/metre in situ testing can provide more accurate data and a core with a probe in place, and can be evaluated more than once so that conditions that may be changing can be monitored. For more prestigious products, it may be best to use RH probe/metre.