Specifying Reflective Insulation: Applications for the building envelope and equipment use
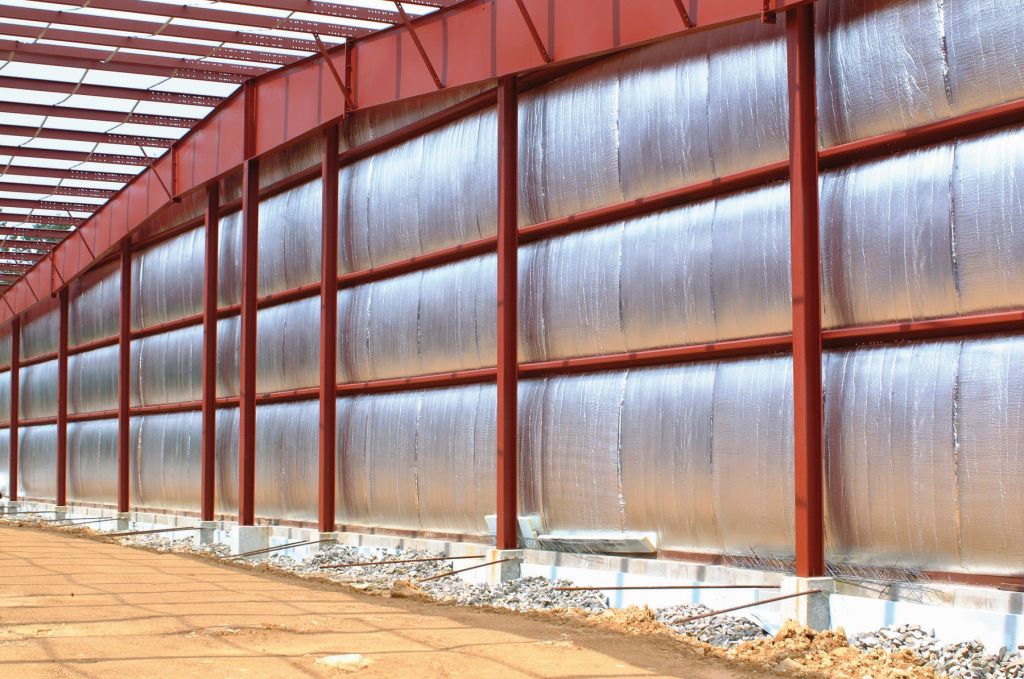
By David W. Yarbrough, PhD, PE
The effective specification and installation of all types of thermal insulation requires an understanding of the factors affecting performance. The specification of a thermal resistance (RSI or R-value) alone does not ensure the intended heat-flow reduction. In virtually all cases, space for insulation must be provided and insulation material must be installed to conform with the manufacturers’ requirements. In the case of reflective insulations, factors such as heat-flow direction, air-space dimensions, and location in the building envelope should be considered.1
The specification of conditioning equipment and reliable prediction of utility use requires understanding of the variation of the performance of any selected insulation with, for example, temperature, air movement, and thickness. In addition, the thermal performance of enclosed reflective air spaces (reflective insulations) depends on heat-flow direction, placement of low-emittance surfaces, and temperature differences.
This article discusses factors to be considered in the specification of reflective insulation systems. In the United States, the labelling and specification of reflective insulations for use in the building envelope or to insulate equipment is set out in ASTM C1224, Standard Specification for Reflective Insulation for Building Applications. However, Canada has not yet published a standard or guide for the evaluation of reflective insulation products.
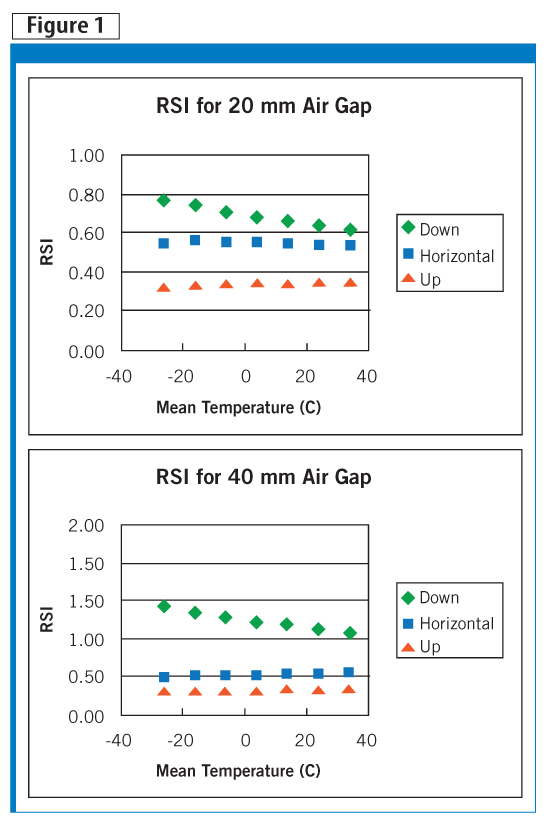
Therefore, the development of a specification for a specific project should take into account the intended location and space available for the reflective insulation assembly. It should also examine other criteria to parallel the ASTM standard. These include:
- location, dimensions, and heat-flow direction for the space to be insulated;
- RSI m2∙K/W (R-value) for the installed reflective insulation assembly (assembly value includes the RSI for the material);
- emittance of the surface(s) of the reflective insulation material;
- resistance to humidity should be represented by test results showing emittance is not significantly increased by exposure to high humidity;
- surface burning characteristics, along with flame-spread and smoke-development indices;
- water vapour transmission (i.e. permeance)—both water vapour retarder and water vapour-transmitting (i.e. perforated) products are available, with selection depending on local regulations and building enclosure design;
- installation instructions for building or equipment applications;
- resistance to fungal growth, absence of bleeding and delamination, and satisfactory pliability are elements of ASTM C1224—a laboratory test report should show satisfactory performance is achieved.
Basis for performance
Thermal radiation across air spaces is an important part of the overall heat transfer across the building envelope in all climates. This thermal radiation is proportional to the effective emittance (E), which depends on the emittances of the hot and cold surfaces enclosing the region, as shown:
E = 1/(1/εcold + 1/εhot – 1) (1)
In other words, the effective emittance for an enclosed air space depends on the emittance of both the insulation and the surface it faces.
‘Effective emittance’ describes the performance that results from two parallel surfaces bounding an enclosed reflective air space. It does not depend on the direction of heat flow. The locations for emittances, hot and cold, can be reversed without changing the value of E. This means a low-emittance surface performs the same when installed on either the cold or warm side of an enclosed air space.
Reflective insulation products use low-emittance surfaces to suppress thermal radiation, providing thermal resistance. They differ from many other insulations in that the thermal resistance is based on an assembly consisting of both the product itself and the adjacent enclosed air spaces. (Reflective insulation materials installed in the building envelope result in reflective insulation assemblies.)
Thermal emittance is a number between zero and one. Reflective products have at least one surface with an emittance near zero and facing an enclosed (unvented) air space. Metals with smooth polished surfaces generally have emittance less than 0.1, while most building materials like wood and masonry are around 0.9.
Aluminum foils and metalized films have been the materials of choice for the exterior surfaces of the reflective insulation (i.e. facers) because of their low emittance, low cost, corrosion resistance, and favourably mechanical properties. Aluminum in the form of thin foils or metalized films laminated to a substrate such as paper, wood, or plastic are used to produce reflective insulations. The thermal emittance value (total hemispherical emittance), consequently, is an important specification requirement for reflective insulations—it is generally in the 0.03 to 0.06 range.
The following equations are often used to estimate the thermal resistance (RSI) for an enclosed reflective air space that is part of the building envelope.
RSI = ∆T / (Q rad + Q convection-conduction)
Qrad = E · σ · ([Thot + 273.15]4 – [Tcold + 273.15]4)
where σ = 5.67 · 10-8 W/(m2∙K4) and T is in degrees C.
This equation is also one of many expressions used to calculate the convective contribution to the total heat flow:
Qconvection-conduction = Nu ∙ ( λ air ∙ ∆T /L)
RSI for enclosed reflective air spaces can be measured using a hot-box facility, which is a large-scale apparatus for measuring the heat flow across a building element such as a section of wall. It must be operated in accordance with ASTM C1224 or reliably estimated using engineering correlations2 or computer simulations.3
Products
Reflective insulations include single-sheet products that consist of low-emittance foils or films bonded to a substrate such as paper, plastic, or polyethylene bubblepack and multiple-layer insulations (Figure 1). In most cases, both sides of the single-sheet insulation are faced with low-emittance foil or film. When only one side has a low-emittance surface, it is important to install that facing the enclosed air space. Reflective insulations with low-emittance surfaces on both sides are commonly used to create two enclosed reflective air spaces in series.
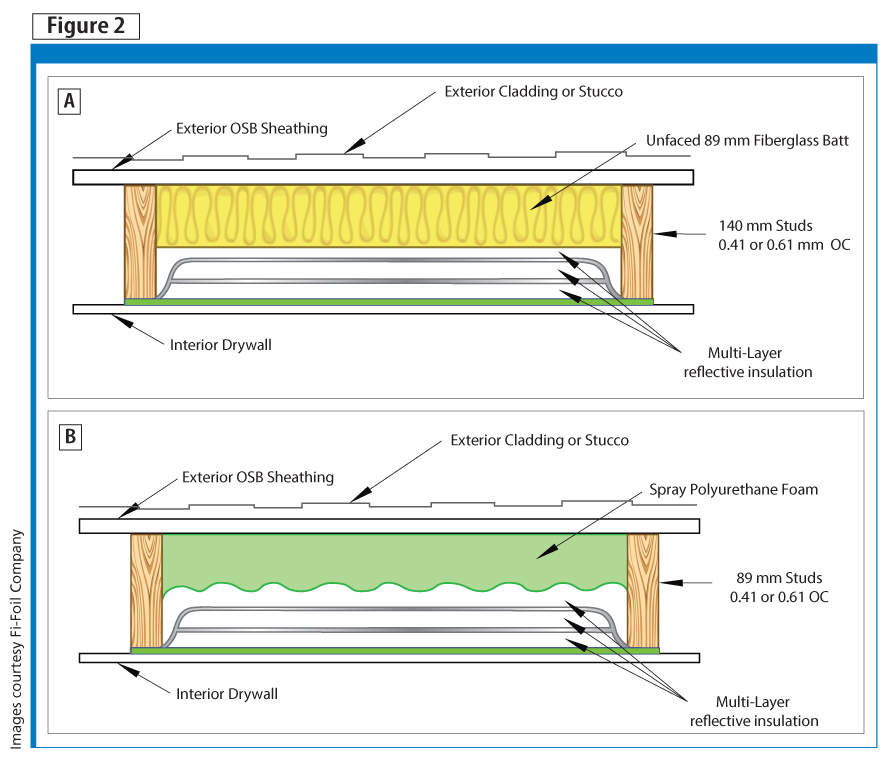
The reflective insulation products with multiple layers are installed to form two or more enclosed reflective air spaces. The specified number of layers and the spacing must be present for the expected thermal resistance to be achieved. Polyethylene bubblepack faced with low emittance foil or film is generally available in two thicknesses: ‘single’ bubble products nominally 6 mm (1/4 in.) thick and ‘double’ bubble products 12 mm (1/2 in.) thick. The applications for the two are the same, but the double-bubble insulation has a greater material R-value and tear strength.
Most reflective insulation products can also be used as ‘radiant barriers’—a term employed for ventilated spaces or large air spaces like a residential attic. The distinction between reflective insulations and radiant barriers results from the way the material is used. Reflective insulations are enclosed reflective air spaces (i.e. non-ventilated) while radiant barriers involve ventilated air spaces. Enclosed reflective air spaces are labelled with RSI-values that have the same units and same meaning as other building insulations; radiant barriers are not labelled with an RSI-value.
The thermal performance of reflective assemblies varies with temperature, as is the case with all insulations. R-values for thermal insulation materials typically decrease as the temperature increases. Products are labelled at a particular temperature—for example, 24 C (75 F)—so comparisons of competing products can be made on a uniform basis.
The thermal performance also varies with temperature difference since gravity-driven convection is a factor. The convective component increases as temperature difference across an enclosed reflective cavity increases. The thermal resistance has a strong dependence of heat-flow direction, thus requiring the intended use or location of the reflective insulation be known before RSI values can be assigned. This is because the temperature of the enclosed air space and the temperature difference across it depend on the location in the envelope.
The temperature difference across an enclosed air space depends on the overall design of the building envelope where the reflective insulation is to be used. The air-gap temperature difference is a fraction of the total air-to-air temperature difference at the location in question.
∆Tair gap = ∆Ttotal ∙ RSI air gap / RSI total
RSI air gap = ∆Tair gap ∙ RSI total / ∆T total
A solution for ∆Tair gap or RSI air gap involves an iterative procedure since RSI total includes RSI air gap and ∆T total includes ∆Tair gap.4 The performance of the enclosed reflective air space is best when the ratio RSI air gap / RSI total is small. This is often the case when an enclosed reflective air space is part of a hybrid insulation assembly.
The variation in thermal resistance (RSI in W/m2∙K) is shown in Figure 2 for mean temperatures from −26 to 94 C (about −15 to 200 F) and air gaps of 20 and 40 mm (4/5 and 1 3/5 in.) in a wall, ceiling, or floor assembly. The RSIs were calculated using the procedure described in ASTM Special Technical Publication (STP) 1116, Insulation Materials: Testing and Applications, using a 10-C (18-F) temperature difference across the air gap.
The RSI-value in Figure 2 demonstrates the reflective assemblies perform as well or better at low temperatures than they do at high temperatures. The significant difference in RSI with changes in heat-flow direction is shown in the figure. The differences in RSI with heat-flow direction is due to the convective component largely absent in the heat-flow down direction. There is significant increase in RSI with thickness in the heat-flow down direction because the heat transport is primarily conduction. There is not a significant increase in RSI with thickness increase from 20 to 40 mm when radiation is the dominant heat-transfer mechanism. This type of performance differs from fibrous or cellular plastic insulation where convection is not usually present.
Hybrid insulation assemblies
Reflective insulations are used with other insulations like fibreglass or sprayed polyurethane foam (SPF) to form hybrid insulation assemblies. The thermal resistance of the hybrid assembly is the sum of the individual RSI-values. The use of enclosed reflective air spaces in this case is attractive because uninsulated space can be ungraded to an enclosed reflective air space. Additionally, the temperature difference across the reflective air space is generally small, making the convective component of heat transfer small or absent. This is an optimal situation for a reflective insulation assembly.
Figure 3a contains an example of a hybrid system that combines fibreglass insulation and a reflective insulation. Figure 3b is a hybrid system using sprayfoam as one component. In both cases, the total thermal resistance in the cavity is the sum of the fibrous or foam insulation and the reflective insulation assembly. A specification should identify the total thermal resistance to be provided by the hybrid assembly.
For this type of system, the overall thermal resistance should be stated along with the RSI-value to be provided by the fibreglass or spray-foam insulation. The space allocated to the reflective components should also be specified. If the reflective insulation assembly is intended to be water vapour transmitting or a water vapour barrier, then the type should be specified.
Figure 4 shows a fibreglass-reflective hybrid. The fibreglass has been compressed to provide space for inset stapling of the reflective insulation. This type of assembly can also be constructed using furring strips as spacers. The photograph shows only two cavities with reflective insulation installed.
Reflective duct insulation
Reflective insulation can be installed on air-handling equipment (i.e. ducts) with and without spacers—material to maintain an enclosed air space between the duct surface and the insulation material wrapped around. Figure 5 shows an example of a reflective duct installation that includes radial spacers and two reflective air spaces.
The thermal resistance of this type of product is determined in accordance with ASTM C1668, Standard Specification for Externally Applied Reflective Insulation Systems on Rigid Duct in Heating, Ventilation, and Air Conditioning, for an assembly specified by the manufacturer. The specification of this type of insulation should include the requirement for spacers (when appropriate), the distance across the air gaps, and the thermal resistance.
Specialty applications
Reflective insulation assemblies for water heaters and garage doors have been available for many years. The thermal resistance intended for the application should be specified along with a requirement for detailed installation instructions. The thermal performance includes a contribution from the air space between the surface of the door and the reflective insulation. The assembly should be specified in terms of number of layers and spacing that will provide the label RSI-value.
Conclusion
Enclosed reflective air spaces provide resistance to heat flow by significant reduction in radiation across air spaces due to presence of low-emittance surfaces. In many cases, there will be air movement (convection) inside the enclosed air space. The convective component of the total heat gain or loss varies with heat-flow direction being the least when the heat-flow direction is downward and temperature difference that is usually small in the case of hybrid systems.
Like all thermal insulations, the thermal performance of enclosed reflective air spaces is characterized by an R-value. The use of reflective insulation as part of a hybrid system provides a way to optimize the use of the available space for insulation in cold climates.
For more information on reflective insulation, design/construction professionals can contact the Reflective Insulation Manufacturers Association (RIMA International).
Notes
1 This author acknowledges Wesley Hall (Reflectix) for reviewing the article. (back to top)
2 For more, see ASTM Special Technical Publication (STP) 1116, Insulation Materials: Testing and Applications, by this author and A.O. Desjarlais. Also, see International Organization for Standardization (ISO) 6946, Building Components and Building Elements—Thermal Resistance and Thermal Transmittance: Calculation Method. (back to top)
3 See the article, “Investigation of Thermal Performance of Reflective Insulations for Different Applications,” by Hamed H. Saber, which appeared in volume 52 of Building and Environment (Elsevier, 2012). (back to top)
4 See ASTM STP 1116. (back to top)
David W. Yarbrough, PhD, PE, is vice-president of R&D Services, an accredited, independent laboratory specializing in thermal insulations and related building materials. He is an emeritus professor of chemical engineering at Tennessee Technological University, and a registered engineer in the states of Tennessee and Florida. Yarbrough is a member of the Building Enclosure Technology and Environment Council (BETEC) Board of Directors, an active member of ASTM Committee C 16 (Thermal Insulation), the International Thermal Conductivity Conference, and the American Society of Heating, Refrigerating, and Air-conditioning Engineers (ASHRAE). He can be contacted via e-mail at dave@rdservices.com.