Specifying Natural Stone: Quality assurance and quality control lead to quality installation
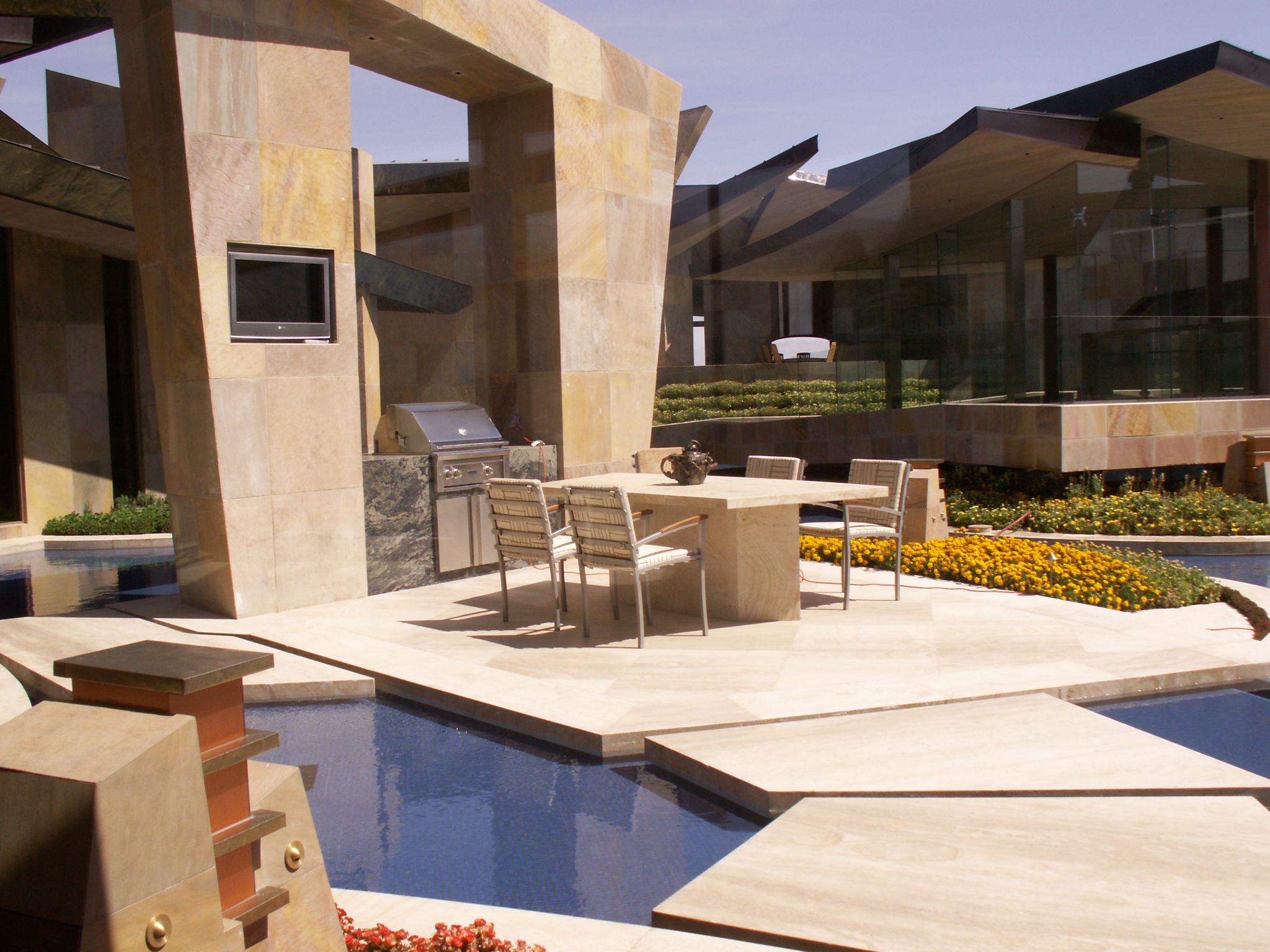
By Donato Pompo, CTC, CMR, CSI, CDT, MBA
Natural stone can be used in residential and commercial buildings in various ways, ranging from claddings and flooring to architectural trim and landscape accents. As the use of this material increases in Canadian projects, it is critical specifiers be current and accurate in their construction documentation. Products used in conjunction with these materials are rapidly changing, so it is no simple process to determine what should be employed or with what method. Further, there is the big labour factor—most natural stone failures are generally related to installer error. The solution to all these potential challenges can be found with good-quality specifications that have detailed, thorough, and clear quality assurance/quality control (QA/QC) articles.1
QC begins with the selection process. One must first understand the application, and then the intended product’s recommended use and limitations. Obviously, as a finish material, esthetics play a major part in the selection process, but only those products suitable for the intended use should be considered. This is where qualified consultants and reliable suppliers should be employed—not only to obtain information, but also to help qualify and substantiate the products suitable for the intended application.
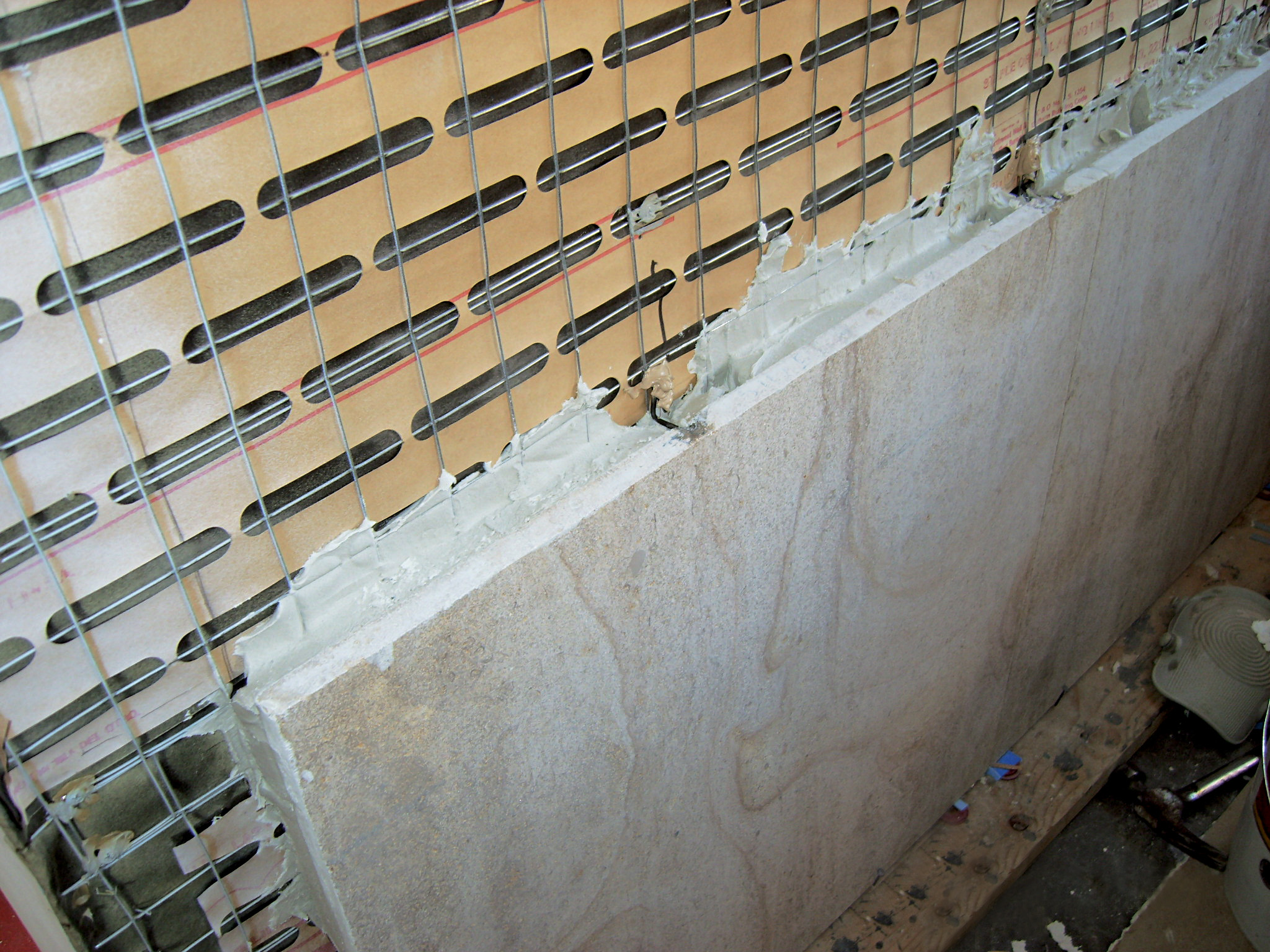
The services of a qualified consultant can help architects understand their options and avoid potential problems with high-risk natural stone applications such as:
- exterior veneers;
- ceilings;
- exterior decks over occupied space;
- high-traffic or heavy-duty applications; and
- showers, swimming pools, and other water features.
For specification writers, it is paramount to create thorough, clear documentation that avoids common ambiguities. Some architects feel reference standards are the best approach—this is certainly easier for the specifier, who then only has to make reference to those general standards. Although listing industry standards is important, it is necessary to have a performance specification to ensure the products are suitable for the intended application.
Many standards are very broad and result in products that can vary substantially in performance, while still meeting the cited standard. Considering the relatively high replacement costs for stone (due to high material and labour costs, along with the delays and loss of use), it justifies specifying better-quality products to help compensate for other potential imperfections and deficiencies during the installation process. For the same reasons, it is also important to have a detailed, clear, and thorough QA section and site QC plan to be implemented by someone other than the installer.
Ensuring appropriate materials through standards
There are numerous common failures in stone applications that can easily be avoided by preparing proper installation specifications including complete and detailed QA/QC specification requirements. Some types of stone do not hold up to various levels of acid rain and/or freeze-thaw conditions, so there are accelerated weathering tests (i.e. modified ASTM C666, Standard Test Method for Resistance of Concrete to Rapid Freezing and Thawing) that can be performed to replicate those expected conditions to verify how the stone holds up over time and whether it is suitable for the intended application.
It is important to remember natural stone typically does not have literature to go along with it. Some importers do provide data information indicating the physical properties of the stone, but this would typically be very limited (unlike ceramic tile data sheets). The referenced ASTM standards should be the minimum physical property requirements. Normally, prior to the accelerated testing, the stone is tested following the modulus of rupture test and/or other physical property tests. It is then subjected to the accelerated test based on the climatic and other conditions of the project site. After the test, it is noted whether there are any visual damages or deterioration (which is then documented), and the modular of rupture, or other tests, are performed again to determine the loss of performance. The laboratory will indicate whether the loss of physical properties is considered normal for the respective type of stone.
Some stones are moisture-sensitive and can result in curling or doming when adhered, so there is a test (i.e. European Committee for Standardization [EN] 14617-12, Agglomerated Stone–Test Methods Part 12: Determination of Dimensional Stability) that can be performed to determine whether the stone is excessively moisture-sensitive. Depending on the application, the amount of pedestrian and/or vehicle traffic to which a stone is subjected can wear and affect its slip resistance. Fortunately, there are abrasion (i.e. ASTM C1353, Standard Test Method for Abrasion Resistance of Dimension Stone Subjected to Foot Traffic Using a Rotary Platform, Double-head Abraser) and coefficient of friction (COF) tests (i.e. the dynamic COF AcuTest in American National Standards Institute [ANSI] A137.1-2012, American National Standards Specifications for Ceramic Tile) that can be performed.2
How should these test results be used to determine what an acceptable level of slip-resistance or suitability for a particular environment? There are many questions to consider:
- Is it interior or exterior?
- Is it going to be subjected to moisture?
- Is there slope on the surface and to what degree?
- What type of traffic/use will it be subjected to (e.g. grease, oil, or other contaminates)?
The current standards only say that per the AcuTest for interior wet applications, the dynamic co-efficient of friction (DCOF) minimum requirement is a 0.42. For an exterior ramp area, it could require a higher value. Depending on the type of application, the architect may need to consult with an appropriate consultant.
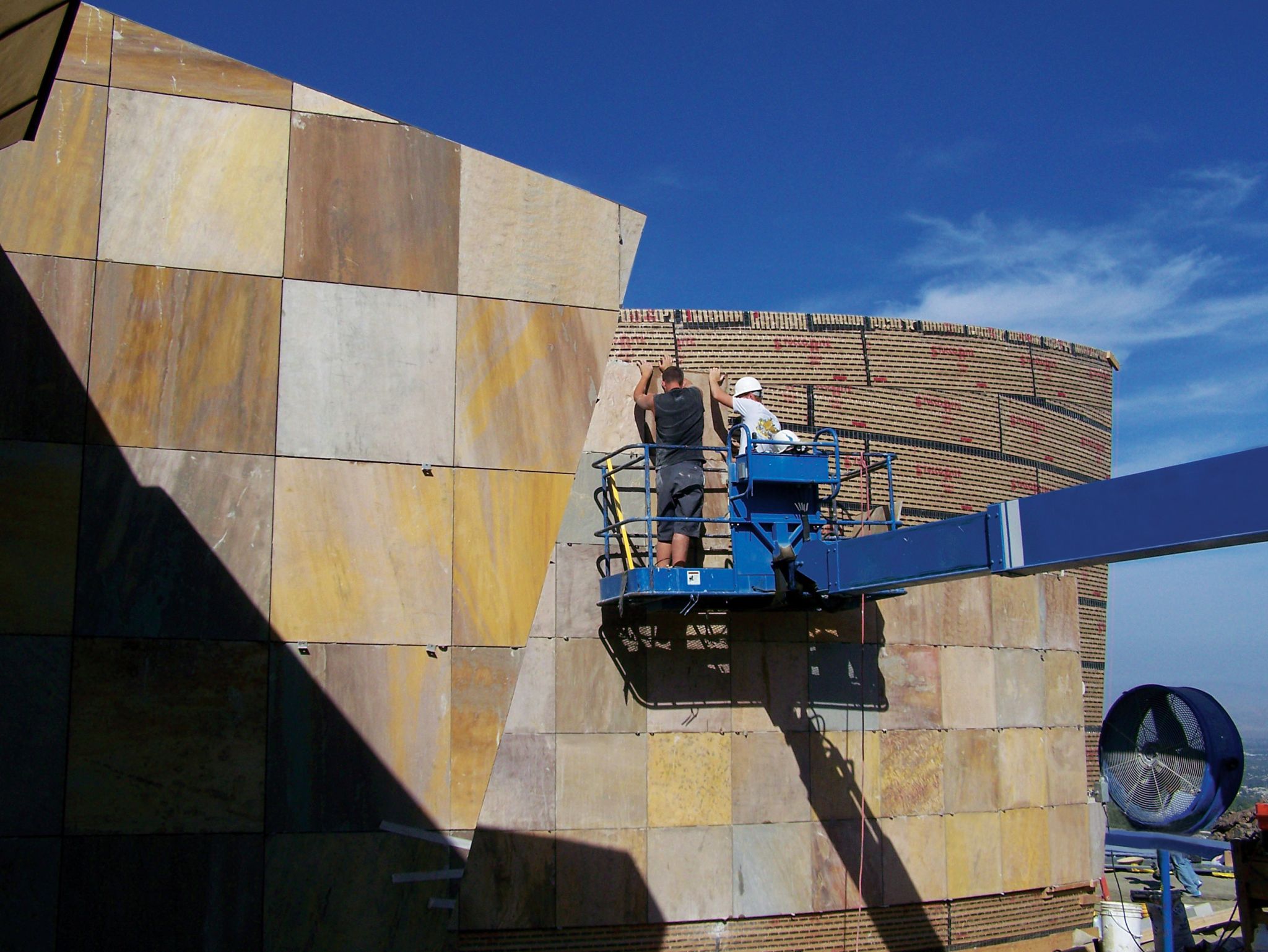
If a stone is incorrectly adhered, particularly for vertical or ceiling applications, it could result in a life safety problem. Improper adhesion can also mean a stone will not perform as it should for a floor. For adhered applications, there are shear bond tests (i.e. modified ASTM C482, Standard Test Method for Bond Strength of Ceramic Tile to Portland Cement Paste and modified ANSI A118.4-5.1 Ceramic Tile) that can be performed to ensure the stone is bondable, particularly when it involves a resin-back stone that might require an epoxy adhesive.
Anchor tests (i.e. ASTM C1354, Standard Test Method for Strength of Individual Stone Anchorages in Dimension Stone) ensure the type and configuration of stone and anchor will perform as designed. For exterior façades, stone slab applications that are being mechanically anchored can have thickness increased to meet the design and performance requirements. Performing QA testing before installation provides an opportunity to adjust the specification and avoid costly delays and problems.
There are site tests that can be performed to determine whether the stone being installed is meeting the building code requirement for shear bond strength as described in ASTM C1242-12a, Standard Guide for Selection, Design, and Installation of Dimension Stone Attachment Systems. Performing QC testing during the stone installation process enables a chance to catch mistakes early and avoid costly problems.
Managing expectations
In some cases, there are false expectations. The specifier and/or client might have certain unrealistic expectations of what they are getting. Stone is a natural product and can have various natural inclusions and other characteristics. How a countertop is fabricated from a slab of stone has limitations as well, so it is important to have shop drawings and require the owner/consultant to approve the layout using the actual stone being used.
For stone tile and slab applications, mockups should be constructed before the start of the installation; on approval, they can be used as the standard to which ongoing work can be compared.
Large mockups are normally only recommended on larger jobs where it is practical, but it can be scaled down to some degree for any job. A sensible approach is to designate the beginning portion of the installation as the in-place mockup. At that point, it is inspected for visual characteristics compared to approved samples, such as colour variation and sizing. It is inspected for craftsmanship in terms of lippage, and how transitions are installed. In some cases, a quantitative bond test can be performed to verify the bond meets the project requirements. Once approved, this portion of the installation is designated as the standard to compare to for the balance of the project.
Part 1–General
Developed by CSC and the Construction Specification Institute (CSI), MasterFormat and SectionFormat provide the structure for good-quality specifications, which produce good-quality stone installations when used correctly and thoroughly. Part 1–General is critical for several reasons. First, it is important to reference the key and relevant standards for the stone industry.
The Tile, Terrazzo, and Marble Association of Canada (TTMAC) Dimension Stone Guide should be referenced for all Canadian projects. Building Stone Institute’s (BSI) Recommended Practices for the use of Natural Stone in Construction is also a good reference document, as is the Indiana Limestone Handbook and the Marble Institute of America’s (MIA) Dimension Stone Design Manual. These stone publications, and their referenced ANSI and ASTM standards, should always be referenced for any stone application.3 However, including a reference standard alone does not require an installer to comply with it. There must be a statement, even if brief, stating “Comply with requirements of ASTM XXX” or something similar.
TTMAC references key ASTM standards applicable to stone, particularly those relative to the physical properties of the various geological classifications of the material. Since natural stone is not manufactured or synthesized in a laboratory, the physical properties and visual characteristics in any particular geological classification can significantly vary. Depending on where the stone quarry is located and which part of the quarry the stone is mined, the physical properties and visual characteristic of stone can substantially differ.
As the MIA design manual outlines, each classification of stone (e.g. granite, marble, limestone, travertine, and slate) has its own ASTM material specification that basically defines the benchmark for being a standard-grade material. The respective ASTM standard states what the minimum/maximum requirements are for each relevant key physical property and the appropriate ASTM measuring protocol. TTMAC’s aforementioned resource provides good specification guidelines for various types of stone installation applications.
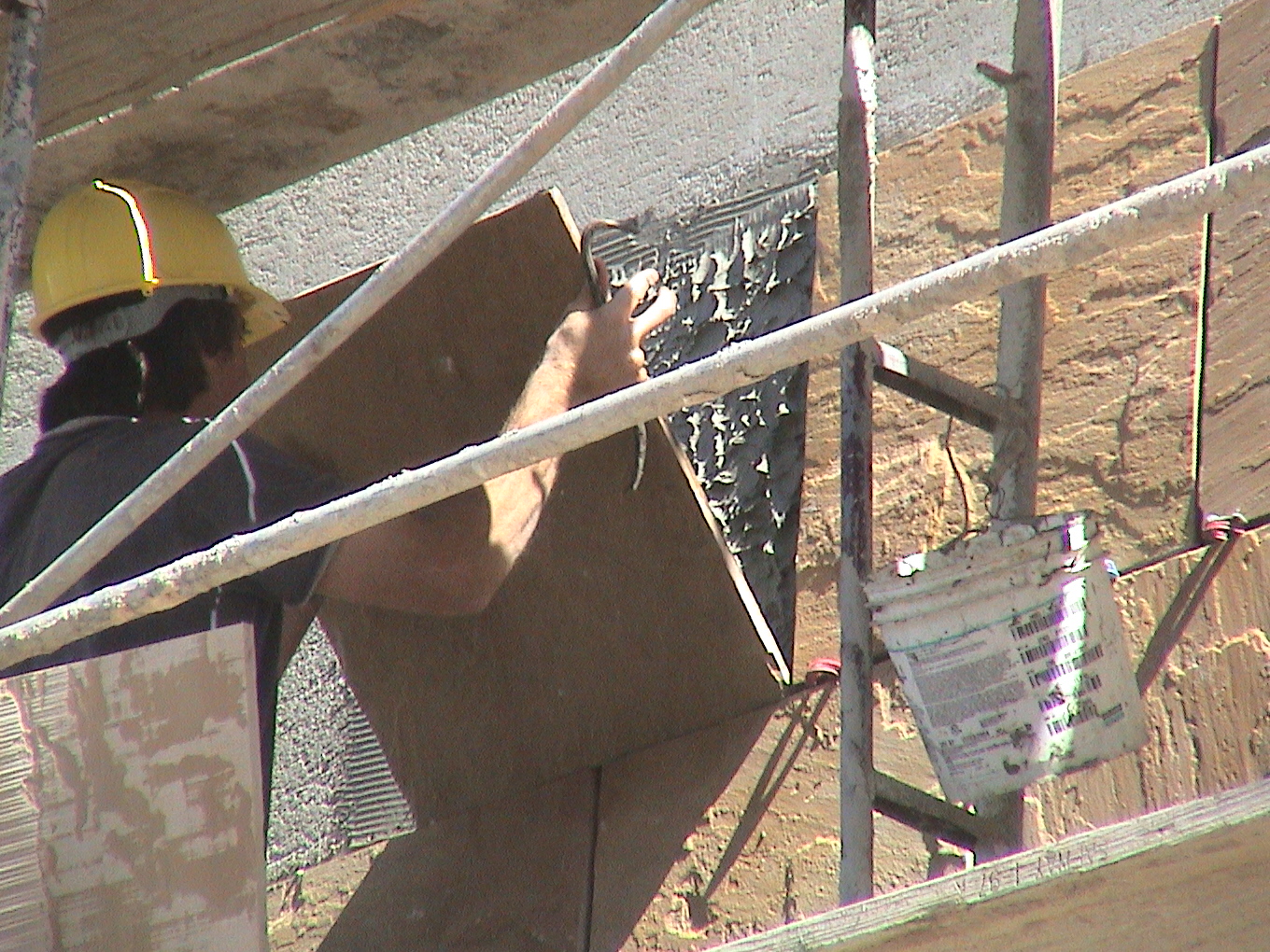
ASTM C1528, Standard Guide for the Selection of Dimension Stone, should also be referenced for any type of a stone application (i.e. it should be reviewed while creating the specification to qualify or determine the requirements to verify the suitability of the stone for the intended use). The guide, recently updated to include interior applications of stone as well as exterior, cursorily reviews the different stone types commonly used in construction, along with common applications, available finishes, and factors affecting product costs. ASTM C1242-12a should be referenced whether it is a mechanical-anchored or stone-adhered application.
In all stone-tile-adhered applications, the TTMAC Dimension Stone Guide should be referenced. It not only provides details for mechanically anchored applications, but it also has details and recommendations for various types of adhered applications. ASTM C1242-12a also covers adhered applications of natural stone.
For projects outside of Canada, one should reference Tile Council of North America (TCNA) Handbook for Ceramic, Glass, and Stone Tile Installation. In the past, it only referenced ceramic tile, although many of the details and applications were recommended by MIA and TTMAC, and commonly used for stone applications.
ANSI A108/A118/A136, American National Standards Specifications for the Installation of Ceramic Tile, should be referenced in all adhered stone tile applications. This set of standards are referenced in the TTMAC, TCNA, and MIA resources, which provide guidelines for the stone tile installation, as well as the test methods and physical properties for tile installation materials. Many of these methods and materials apply to the installation of stone tile and should be followed. ANSI A108 not only provides standards for sub-surfaces and preparations by other trades, but it also offers standards for materials and workmanship, as well as detailing the installation of various methods and materials.
The National Stone Council and NSF International are in the process of creating a Standard for the Sustainability Assessment for Dimensional Stone. Natural stone has some huge features and benefits in terms of environmental sustainability, considering the material makeup, how it is produced, and the long lifecycle. Natural stone can help projects seeking certification under the Canada Green Building Council (CaGBC) earn points in various Leadership in Energy and Environmental Design (LEED) credits, substantially contributing to a projects’ sustainability rating.4 The ANSI A108 committee has recently created the new ANSI A138.1, Specification for Sustainable Ceramic Tiles, Glass Tiles, and Tile Installation Materials, further qualifying the LEED points earned for stone-adhered applications by use of the tile installation products.
Submittals
Quality assurance needs to be project-, product-, and application-specific. The physical properties and suitability of products must comply with standards and be verified. Too often, materials like natural stone are imported without verifying physical properties and suitability, and are sold based on price and appearance, rather than standard-grade requirements and suitability. Esthetics are important, but suitability is critical.
Samples representative of what will be supplied for the project must be submitted and verified before delivery to the project site. Owners often feel forced to live with something different from what they intended. By the time a product is delivered to the jobsite, the delays and costs to replace it are prohibitive—even more so when the product gets installed before a deficiency is noticed.
Site mockups should be required and used as the quality control standard for colour range and other visual requirements like tile lippage, layout, and workmanship requirements. Required warranties should be specified, provided in writing, and clearly stated. Warranties are never ‘no-fault’ insurance—there are always conditions and limitations, so the requirements must be incorporated within the quality control process to ensure the materials are being stored, prepared, and used as required. Following industry standards is always a requirement of the warranty.
Training and supervision
A very important, but oft-forgotten, QA aspect involves requiring and verifying the installers understand and follow industry standards. Installers frequently learn on the job, and may lack formal training. On larger jobs, a group of installers will likely have varying levels of experience—those that may have the mechanical skillset to do the work might be limited in understanding the complexity of the task or knowing the industry standards.
Standards have been created by industry consensus committees to help avoid problems and ensure successful installations. If the installers do not know the standards, then how can they avoid those potential problems? It should be specified the installers working on the project verify they went through a training program to review industry standards and the quality control plan for the project.
Compounding the lack of experience and deficiency in understanding industry standards is the reality many subcontractors do not provide enough qualified supervision to manage their work force. This applies to both mechanical-anchored and adhered stone applications. There typically is not enough full-time, non-working, supervisors managing those onsite.
Supervisors normally lack formal training themselves and may be limited in their ability to manage the work force. They should not only be managing the work, but they should be supervising the installers, ensuring they are following the specifications and industry standards.
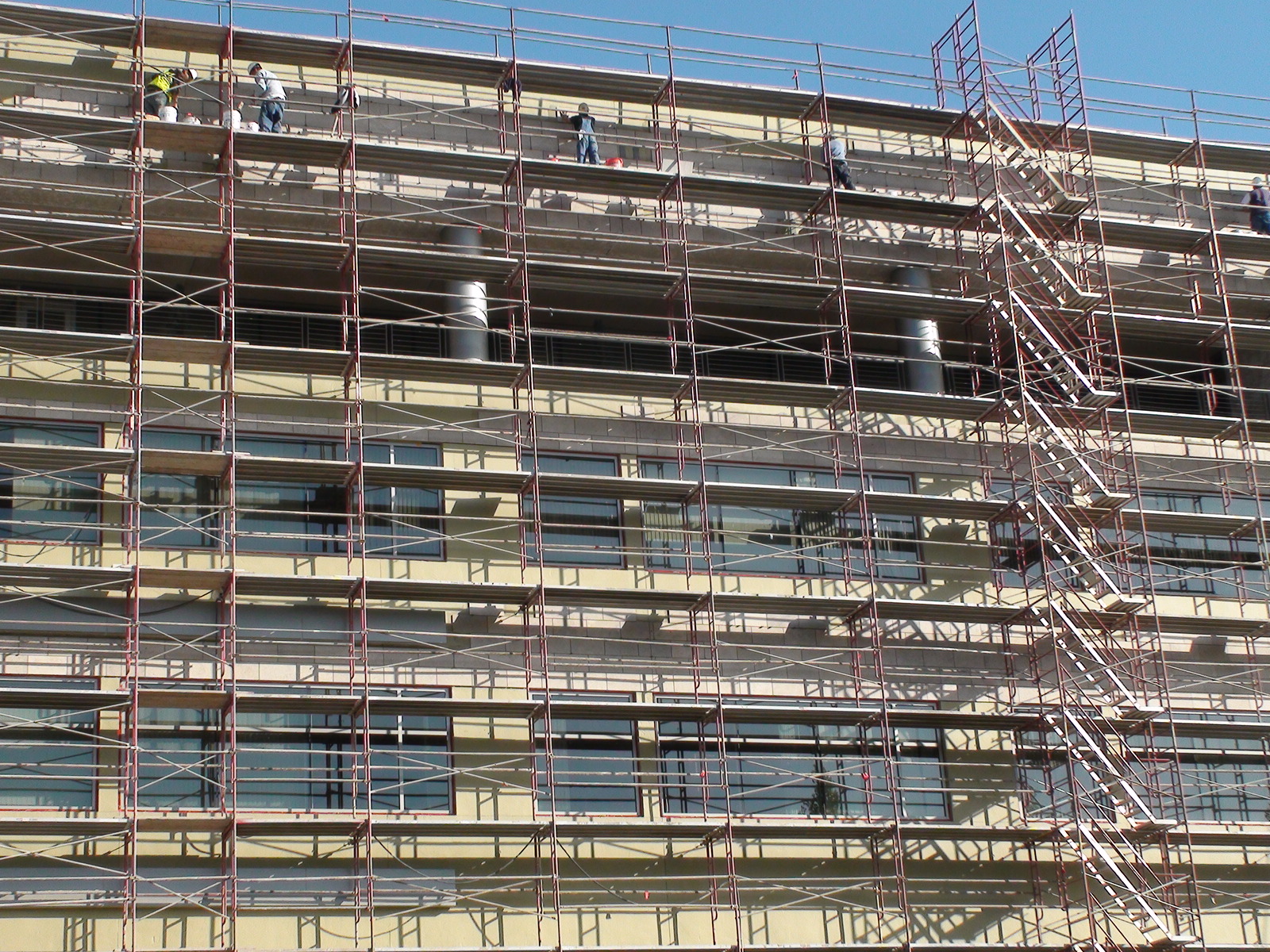
Part 2–Products
Part 2–Products is important because it gives the architect the opportunity to specify products that will not only perform as required, but can also be competitively priced. Performance-based specifications enable quality and performance to be called for without being locked into a high-priced proprietary product. Reference standards, on the other hand, allow the lowest acceptable performing product to be used, which is normally the cheapest and lowest-performing product.
As an example, for latex-portland cement mortar, ANSI A118.4 lists only minimum requirements for latex or polymer-modified thin-set mortar adhesives. It does not discern between the least-expensive/lowest-performing products and the most expensive/highest-performing products, which may represent a huge chasm of difference. If one were simply to specify “meet ANSI A118.4” without qualifying performance, then some bidders will base their bid on the cheapest product rather than what is best for the intended application. The ANSI committee is working on adjusting the standard so specifiers can select the level and type of performance required for the thin-set mortar.
The TCNA Handbook recently added International Organization for Standardization (ISO) 13007, Standards for Adhesives and Grouts, as an appendix. ISO C-Cementitious Mortars can be designated and specified to clearly show the level and type of performance required for a particular project to include:
- level of bond strength;
- setting speed;
- open time extension;
- slip resistance (non-sag);
- level of deformability; and
- suitability and level of performance for adhering to plywood.
Another common issue that comes up with natural stone tiles involves those materials supplied with a resin/fibreglass-reinforced back. Stone processors will apply the resin/fibreglass on the back of some relatively fragile stone tiles and slabs before they ship the material to avoid damage during the transportation and handling process. The problem is there is no standard for these resins and different stone processors use different resins.
Some resins are incompatible with thin-set mortar adhesives and cannot provide an adequate bond (even if the grooves are cut into the back of the stone). Thin-set adhesive manufacturers always state on their mortar data sheets to use their epoxy adhesives when adhering resin back stone, unless they have had the opportunity to test the resin back stone with their thin-set mortars to see if they are suitable for that particular stone and application.
Part 3–Execution
Part 3–Execution is critical, and this portion of the specification section should never be published without careful review. The architect must clearly specify the appropriate details and steps for each type of stone application. Consistent with the ANSI A108 standards, the substrates to which the tile is attached needs to meet requirements and tolerances for the installer to be able to provide a satisfactory installation.
Proper preparation of the substrate needs to be clarified; it will always require cleaning, but may also require scarifying the surface to remove any contaminates and opening of the concrete pores to allow for an adequate adhered attachment.
Installing over cracks is never acceptable. Structural cracks need to be repaired by the general contractor, and shrinkage cracks must be isolated with a membrane per TTMAC Tile Manual 311F, Detail C for adhered applications. Substrates also need to be inspected and properly prepared for mechanical anchored applications. Expansion and control joints must continue through the stone assembly. Specific TTMAC installation method details need to be specified for each adhered application, taking into consideration the type of substrate, whether it is on-ground or a suspended floor, a wall over solid or framed backing, interior or exterior, and whether it is a wet or dry application. Shop drawings that are code compliant and approved by a structural engineer are required for all stone mechanical anchored applications. Workmanship standards need to be specified in terms of proper stone layout, tolerances such as lippage, acceptable clean-up, and safe and proper protection of work and adjacent areas.
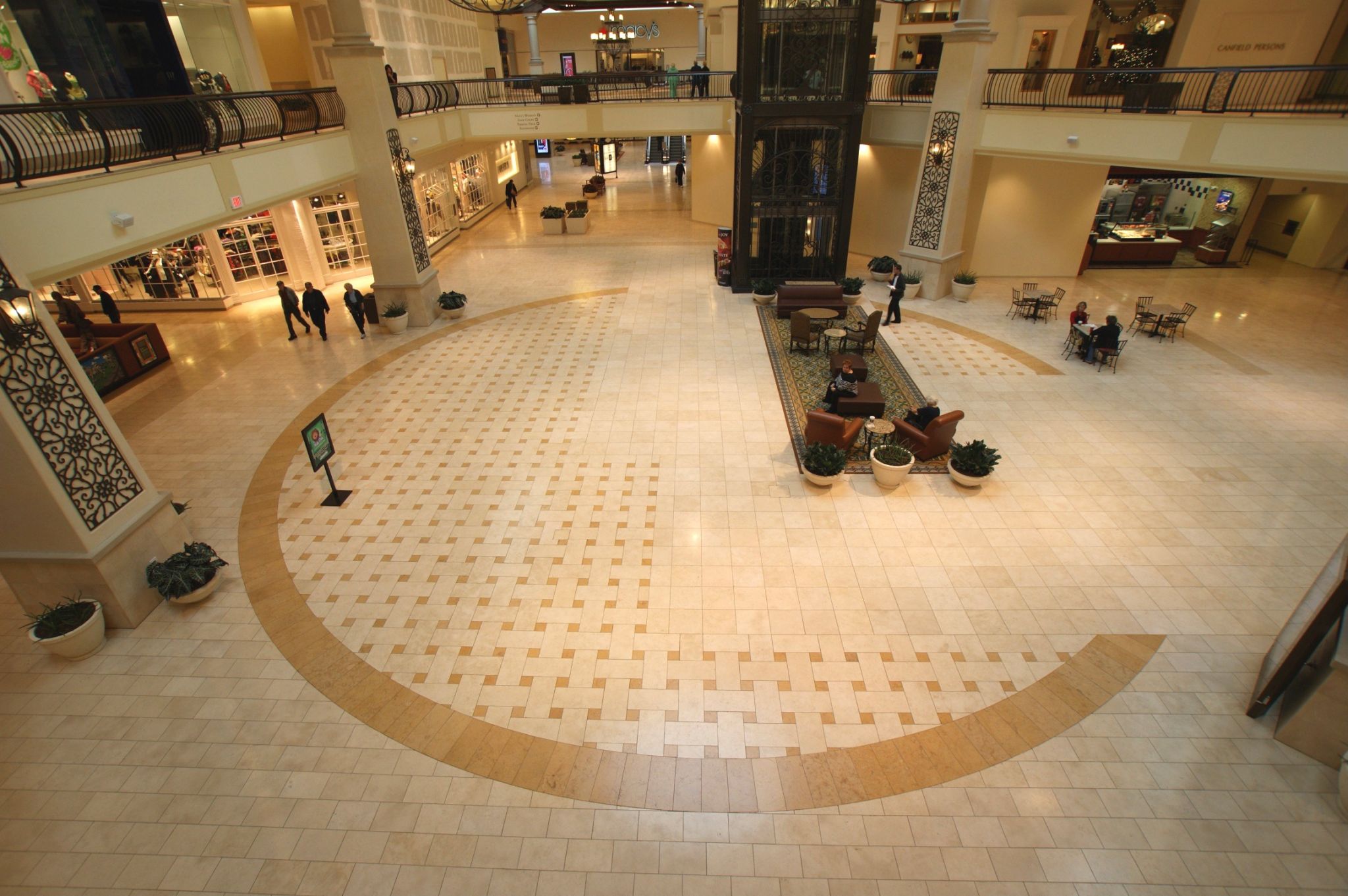
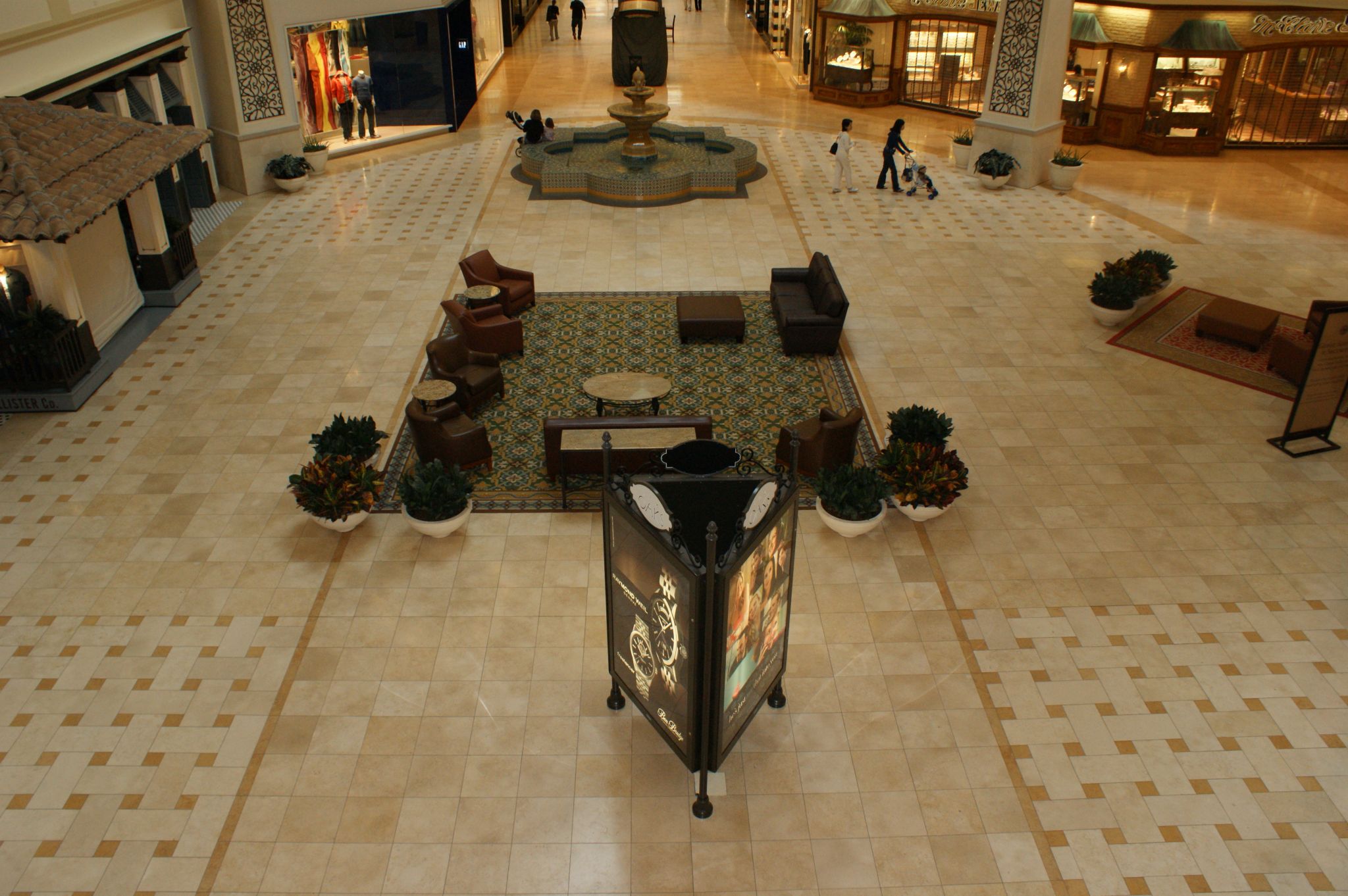
Quality control plan
Part of the quality assurance is to specify a quality control plan be established and implemented by someone other than the installer. A qualified third-party representing the owner is preferable. Part of QA is to verify the product and application will perform as intended.
For high-risk applications (e.g. adhered exterior veneers), onsite shear bond testing should be required as stated in ASTM C1242-12a. The ASTM C18 Stone committee is finalizing a new test protocol for shear testing adhered stones onsite so it can be used as a QA method. Mechanical anchored applications need a quality control process as well to make sure the anchors are being correctly installed and adjusted.
The site QC plan is critical and needs to be project-specific, thoroughly specifying, in detail, the quality control process, steps, and testing required during the stone installation process. The objective is to avoid costly delays and problems, and to catch problems before they become contributing defects in a costly failure.
Equally important to having a good QC plan is having a qualified inspector to implement it. This person should have installation experience and knowledge of stone industry standards. The quality control process is actually a great training program for the installers working on the project. As the QC inspector implements the plan, installers benefit by learning industry standards and the correct methods for installing the stone. The installers also benefit from the inspectors’ experience and knowledge. At the end of a job with a good quality control plan, the stone installers are more knowledgeable and proficient at their work—this should follow them to their next project.
The installing company should have its own internal QC plan to limit their exposure and costs, and to perpetuate a reputation as a quality installation company. In the past, installers were not able to easily and affordably learn industry standards and acceptable installation methods. Now, online courses can verify installers know industry standards.5
Conclusion
When there is a problem, it does not necessarily matter who is at fault—everyone will pay in one way or another in time, money, or reputation. It is important specifiers avoid cutting and pasting tile specifications; they should always thoroughly review the intended applications, the suitability and limitations of products, and the relevant industry standards. Quality assurance and site quality control plans are essential to ensuring a successful stone installation.
Notes
1 In an earlier form, some of this article appeared as “Writing Quality Stone Specifications” in the Fall 2012 issue of Building Stone Magazine. (back to top)
2 For more on COF, see this author’s “Avoiding the Fall” in the October 2012 issue of The Construction Specifier. (back to top)
3 For these respective resources, visit www.ttmac.com, www.buildingstoneinstitute.org, www.tileusa.com, www.marble-institute.com, www.astm.org, and www.iliai.com. (back to top)
4 Examples of natural stone’s ‘green’ attributes include a century-long lifecycle, passive thermal mass, low environmental impact, low impact on water and indoor air quality (IAQ), and waste reduction/reclamation. (back to top)
5 One example is the University of Ceramic Tile and Stone’s (UofCTS’s) TTMAC Tile Installer Thin-set Standards (ITS) verification course, which is formatted to meet Canadian requirements. Visit www.uofcts.org. (back to top)
Donato Pompo, CTC, CMR, CSI, CDT, MBA, is the founder of Ceramic Tile and Stone Consultants (CTaSC), and the University of Ceramic Tile and Stone (UofCTS). He has more than 35 years of experience in the ceramic tile and stone industry, from installation to distribution to manufacturing of installation products. Pompo provides services in forensic investigations, specification writing, training programs, testing, and onsite quality control (QC) inspection services. He has worked on numerous projects throughout Canada and the United States. Pompo can be reached via e-mail at donato@ctasc.com.