Specifying building wrap for moisture management and drainage
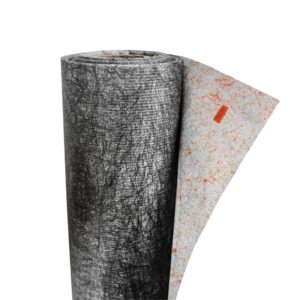
Typically, this inwardly driven moisture vapour is managed by separating the cladding from the rest of the assembly with a capillary break, which can be an air gap or a sheathing material that sheds water or does not absorb or pass water.
Impermeable sheathing, such as extruded polystyrene (XPS), is a possibility for halting inward vapour drive. In these assemblies, the inwardly driven moisture condenses on the surface of the XPS sheathing and drains downward.
However, in situations where a reservoir cladding is paired with a highly permeable sheathing, sich as gypsum board (which can be as high as 50 perms), or a moisture-retentive material such as OSB, an air gap may not be enough to slow down inward moisture intrusion. In these applications, an added weather-resistant barrier—commonly referred to as a building or housewrap—is needed to reduce unwanted moisture intrusion.
In an article on the topic, Drain the Rain…On the Plane…the Drainage Plane,1 building scientist Joseph Lstiburek argues there are two reasonable ways to deal with inward vapour drive—a “vapor throttle” or an air gap. Lstiburek writes, with a small air gap (less than 4.7-mm [0.1-in.]), there is a “sweet spot” for vapour transmission control of the water control layer. That “sweet spot” is somewhere between 10 and 20 perms. If it is any more permeable, the moisture driven out of the back side of the reservoir cladding into the air space will blow through the layer, through the permeable sheathing, and into the wall cavity. Any lower, and the outward drying potential of the cavity is compromised.
Evolution of building wraps
Due to their durability and ease of installation, building wraps made of polyethylene or polypropylene fabric have been a popular method of protecting against moisture intrusion since the 1970s. However, as building assemblies have gotten tighter, building wraps have taken on a new function: helping remove trapped water from the building enclosure. Their unique functionality enables them to block moisture from the outside while allowing walls to “breathe” to prevent vapour buildup. The latest innovations in housewrap technology are taking this moisture removal function one step further to incorporate drainage capabilities as well.
Historically, drainage has been achieved by using furring strips that separate the wrap from the structural sheathing and framing, but today’s advanced building wrap products create integrated drainage gaps through creping, embossing, weaving, or filament spacers. By eliminating the need for furring strips, these wraps can help to reduce material costs and streamline installation.
The drainage efficiency of a building wrap is generally tested in accordance with ASTM E2273. In simple terms, this test involves spraying water onto a wall assembly and measuring its collection over time. However, given the variety of drainable building wraps available, how quickly bulk water is drained can vary significantly. The following is a look at a few methods modern building wraps use to drain water from a wall assembly.
Integrated rainscreens
One method for achieving bulk water drainage is the integration of a rainscreen material onto the building wrap. These products eliminate the cost and time-consuming labour of installing furring strips by creating a gap between the sheathing and the cladding, which facilitates both drainage and continuous airflow. Where wood strapping only vents approximately 85 per cent of the wall, building wraps with an integrated rainscreen provide a continuous vented airspace over the entire surface area of the wall, providing greater drainage and more effective drying. Further, since many rainscreen products use a matrix of plastic material to achieve the gap, they are not subject to saturation and decomposition that could compromise wood furring.