Specifying building wrap for moisture management and drainage
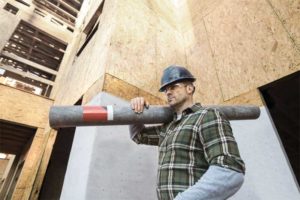
WRBs, on the other hand, are usually limited to residential and low-rise structures. In fact, building codes require the use of such barriers, but some provinces have added even more prescriptive measures to their codes to include the use of drainage planes.
In the U.S. for example, Oregon requires the building envelope to consist of an exterior veneer, a WRB, a minimum 3-mm (0.125-in.) space between the weather-resistant barrier and the exterior veneer, and integrated flashings. The envelope must provide proper integration of flashings with the WRB, the space provided, and the exterior veneer. In lieu of providing the 3-mm (0.125-in.) space between the exterior veneer and the WRB, builders can install the exterior veneer over a barrier that is manufactured to enhance drainage and meets the 75 per cent drainage efficiency requirement of ASTM E2273, Standard Test Method for Determining the Drainage Efficiency of Exterior Insulation and Finish Systems (EIFS) Clad Wall Assemblies, or other recognized international standards.
Cladding and vapour drive
Another factor driving the growing demand for drainable wall assemblies is cladding; specifically trends in materials and potential issues associated with those materials. Reservoir cladding such as stucco, for example, can present major problems if the wall assembly is not constructed in a way to allow adequate drainage.
In fact, it was widespread failures of stucco cladding installed over wood-based sheathing that lead both the IBC and IRC to require “a minimum 4.7-mm (0.1875-in.) space…between the stucco and water-resistive barrier or a space having a drainage efficiency of not less than 90 per cent, as measured in accordance with ASTM E2273 or Annex A2 of ASTM E2925, be added to the exterior side of the water-resistive barrier.”
ASTM E2273 was itself developed in response to thousands of EIFS buildings which experienced failures due to the lack of drainage between adhered expanded polystyrene (EPS) rigid insulation and sheathings, both oriented strand board (OSB) and gypsum board.
Brick and fibre cement siding remain popular with home buyers and, similar to stucco, are reservoir claddings are also presenting specific moisture management challenges. In fact, several fibre cement siding manufacturers are beginning to stipulate that wall assemblies using their products incorporate drainage to qualify for warranty coverage.
This is because moisture absorbed by reservoir claddings such as brick, fibre cement, stucco, and unpainted wood can be driven inward by solar radiation. The heating of the stored water raises its vapour pressure, driving it both inward and outward. This inward vapour drive is even higher when the indoor environment is cooled by air conditioning. Proper drainage strategies ensure the inwardly driven moisture does not infiltrate the wall cavity, where it can create mould issues and other potential health threats.