Smart, connected real estate
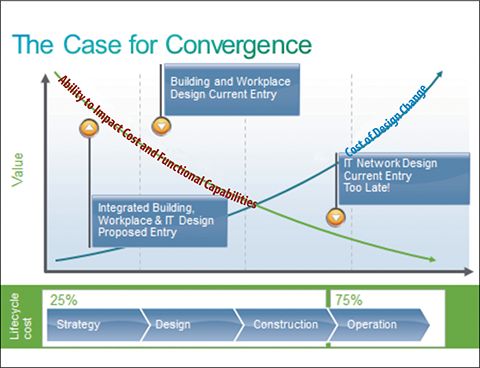
Designing WaterPark Place III
The journey of WaterPark Place III began with two queries: Would a smart, connected building deliver new value? Which stakeholders would benefit? With these questions on the table, the process began.
In addition to Oxford Properties, the project team included WZMH (architect), Hidi Rae (prime mechanical consultant), MMM Group (prime electrical/IT consultant), EllisDon (contractor), and smart building network company, FlexITy Solutions. By leveraging an IT smart network not just for the traditional IT services (e.g. Internet, communications) but also for base building applications (e.g. lighting, heating/cooling), it was clear to see replacing disparate networked siloed base building systems with one converged IT networked enterprise solution meant savings in both capital and operating expenditures as only one infrastructure needed to be constructed for multiple applications.
All project stakeholders (i.e. ownership, design, construction, and operations) focused on the concept that if this ‘converged IT infrastructure’ was considered early (i.e. during concept and preliminary design phases), then value would rise in comparison to the tried and true method of waiting until the last moment, once the majority of the building had been constructed, to install a network. For WaterPark, timing was right to take advantage of PoE at the edge, and the analysis of disparate versus converged clearly indicated the latter was the correct direction.
During the design phase, all manufacturers and solution providers responsible for HVAC control, lighting, electrical metering, security, and CCTV were asked to provide system architecture solutions with primary and secondary devices/controllers connected by either Internet Protocol (IP) Ethernet or IP Ethernet/PoE.
Each solution was reviewed and evaluated by the design team, with special attention applied to Day 1 capital expenditures and commissioning. If the solution passed a Day 1 Test, then criteria specific to Day 2 operations and lifecycle costing was applied. Once Day 1 and Day 2 criteria were met, the solution then became part of the base building design tender set.
The various solution packages where then put out to tender. These tenders were released in parallel to the prime mechanical and electrical trades. Since network convergence bridged both mechanical and electrical trades, a co-ordinated effort was undertaken to ensure traditional disparate networks were not included in pricing and commission scopes. Power and communication wiring duplication was eliminated by having a clear set of tender documents. The tender set laid out all network and power requirements, system architectures, end customer uses cases and commissioning schedules. A detailed ‘responsibility matrix’ provided needed mechanical and electrical discipline co-ordination.
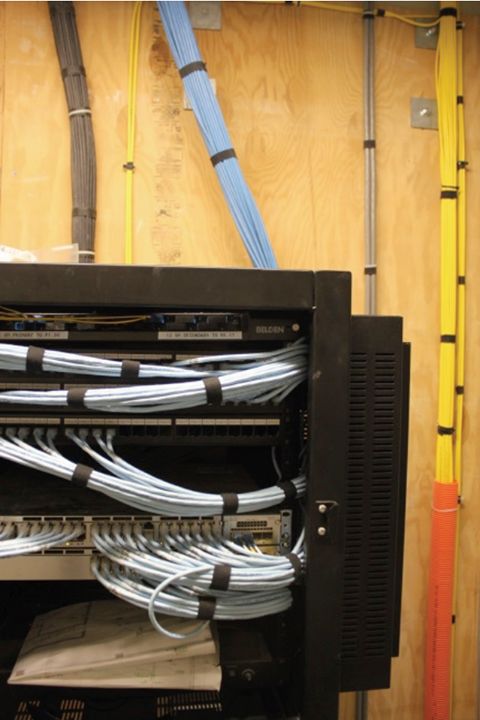
Once all tenders where closed, the design team evaluated each separate system on a standalone basis. Special attention was applied to both capital and operating expenses, along with ease of integration. The selected individual systems were then combined and the total value of expenditures was reviewed with final sign-off following.
With all systems and trades selected, the delivery of a smart building was started. Through the delivery process, special attention was given to having an active PoE network installed and activated early. All IT rooms were required to come on-stream very early in the process so the edge devices for the base building systems (e.g. HVAC, lighting, CCTV, and security) could be powered and then commissioned. The hurdles encountered were not technical, but came in the form of changing traditional process and practice.
For example, all electrical and mechanical consultants and contractors needed to be onsite earlier and have scope completed and commissioned well ahead of traditional construction schedules. Timing and scheduling where adjusted accordingly by the lead general contractor (EllisDon) who ensured its project managers were well-versed in network convergence.
For base building systems, the system that contributed the largest ‘smart’ value came in the form of the HVAC BAS. Delta Controls of Vancouver was selected and its architecture that included PoE (15 watts) for the VAV controls transformed installation, commissioning, and operations. By simplifying installation, programming, and integration, first costs and operating expenses were reduced. Approximately 1800 PoE-powered and communicating controllers/thermostats were supplied and installed.
Structured Cat 6 cable was supplied and installed by Guild Electric’s structured cabling division during the base building’s concrete pour. It was essential mechanical and IT electrical drawings clearly indicated physical locations for all ductwork and terminal units. All cable runs were home-run from the thermostat/controllers distributed on the floor plate back to the centralized IT room, located adjacent to the main electrical and mechanical rooms per floor in the core of the building. The home-run structured network eliminated line-voltage cabling and conduit, which led to quicker and lower-cost installation.
During the construction phase, IT rooms were constructed and powered earlier than traditional projects. IT switches came on-stream much earlier since they provided both power and communication for the primary base building systems. Based on early planning, co-ordination, and scope definition, the base building construction was smooth and seamless. Collaboration between all trades, manufacturers, and consultants delivered a next-generation building designed to be flexible and interactive with the tenants’ needs today and tomorrow.