Sink or swim: A comparison of below-grade rigid foam insulation moisture performance
By David Stassi
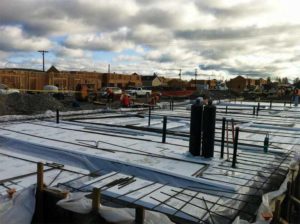
Creating a strong building starts with the foundation. In the same way, designing an energy-efficient building starts with insulating from the foundation up. This is why savvy building professionals insulate below-grade. They include insulation on buried foundation walls and under floor slabs, knowing this is the first step toward maximizing a building’s efficiency. However, creating a building with a Leader in Energy and Environmental Design (LEED)-certified plaque on the wall does not come about by putting just any type of insulation on the foundation and below the floor.
Due to poor moisture performance, not all insulation types are suited for below-grade use. Taking the time to learn about the physical properties of insulation products and how they handle moisture is, therefore, key to ensuring the selected material will perform as intended below grade to help maximize a building’s energy efficiency. In a market flooded with options, making the most informed decision comes from understanding the products inside and out. For the purposes of this article, commonly used below-grade rigid foam insulation products will be examined.
Why below-grade insulation is important
It may seem counter-intuitive to install insulation below grade due to the historically high-moisture content of Canadian soil. After all, damp insulation is much less effective at blocking the flow of heat than dry insulation. However, the Expanded Polystyrene (EPS) Industry Alliance notes, a lack of insulation on below-grade foundations, crawlspaces, and under slabs accounts for up to 25 per cent of a building’s total energy loss (Read Expanded Polystyrene (EPS) Industry Alliance’s Technical Bulletin 103, “15-Year In-situ Research Shows EPS Outperforms XPS in R-value Retention.”). Additionally, uninsulated concrete creates a thermal bridge between a building’s heated interior and the relatively cooler earth surrounding its structure, as well as through any concrete foundation edges exposed to the outside air. Blocking this heat flow is critical to creating a comfortable, energy-efficient building. The dilemma, however, is determining the insulation that will not lose its insulating properties in the damp soil and effectively insulate a building’s below-grade spaces.
Moisture’s effect on insulation
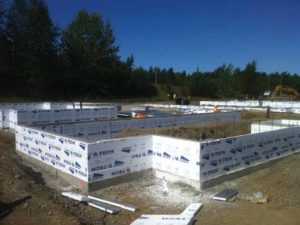
Imagine someone stepping out into the cold Canadian winter air with proper warm, dry clothing. Since their body is well insulated, it does not have to work hard to stay warm. Now, if the clothes get wet, their body would have to work harder to fight off the cold winter air. This is because water conducts heat better than textiles, and damp clothes provide an easier path for heat to escape from skin. These same principles apply to rigid-foam insulation.
When rigid-foam insulation is wet, the moisture causes the material to compress, reducing the space for insulating air trapped between layers. As the insulation continues to uptake moisture, the trapped air is displaced from the space. This reaction causes the compressed and wet insulation to experience a drop in its thermal performance rating (R-value). Insulation that is not well-rated for use below grade will uptake this moisture and not release it.
Additionally, water’s thermal conductivity is nearly 10 times higher than the conductivity of the average thermal insulation (Consult the presentation “Effects of Moisture on Thermal Insulation” by Steve Badger, PhD, at the International District Energy Association (IDEA) 2017 annual conference.). How does this effect insulation performance? According to Professional Service Industries (PSI), a division of construction materials testing firm, Intertek, “Absorption of only 20 per cent moisture can cause up to 55 per cent loss of insulation value.” Installing insulation in a moisture-rich environment below grade presents the risk of losing over half of the insulation’s engineered thermal capabilities. To prevent this from occurring and ensure the insulation resists heat flow from the surrounding earth and the foundation wall or slab, it is crucial to select a product that mitigates moisture’s impact on its thermal properties.