Sink or swim: A comparison of below-grade rigid foam insulation moisture performance
Deciphering the results: Below-grade rigid foam moisture performance
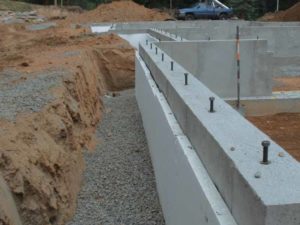
As evidenced throughout this article, virtually no insulation is immune to moisture reducing its thermal performance. However, the level to which an insulation readily absorbs and releases water is key to determining its below-grade efficiency. Since EPS and XPS perform significantly different in terms of moisture, much confusion exists about which one is better for below-grade use. Ultimately, the answer depends on how it is measured.
ASTM C272
Moisture performance of rigid foam insulations, including XPS and EPS, is reported on product data sheets based on ASTM C272, Standard Test Method for Water Absorption of Core Materials for Sandwich Constructions. In this test, the lab submerges insulation samples in water for 24 hours, and then weighs the samples for moisture absorption immediately upon removal.
The ASTM C272 tests reveal, and product manufacturers typically agree, EPS absorbs small amounts of moisture more quickly than XPS does. Fortunately, virtually no building is subjected to 24 hours of continuous submersion, otherwise there are bigger problems at play. Most buildings go through periods of wetting and drying. This allows the insulation to release the moisture and return to efficiently insulating the foundation. Although the explicit results of the test would seem to imply XPS offers superior moisture performance, it is important to understand EPS releases moisture much faster during these wetting and drying cycles. This fact is especially significant when considering how both materials perform in the field.
In-situ testing
Good coaches understand that, even if their team performs well in practice it does not necessarily mean that they will perform well in the game.
To properly prepare for a game, a coach should provide in-game situations before the team takes the ice. In the same way, relying only on the laboratory results of ASTM C272 without testing how a product performs in-situ is like playing for the Stanley Cup without proper preparations.
In one example of a real-world application versus a laboratory test, the Expanded Polystyrene Association of Canada (EPAC) and the National Research Council Canada (NRC) jointly conducted EPS moisture performance testing over a 30-month exposure period in an exterior below-grade application. The testing was conducted in an area of multiple freeze-thaw cycles and monitored using thermocouples attached to the insulation and concrete wall. During heavy rains and thaws, the monitoring detected moisture on the outside surface of the EPS foam, but moisture penetration was not observed on the surface of the structure’s foundation. Further, performance tests confirmed the EPS insulation did not lose any of its thermal insulating R-value after over two years in-situ. Moreover, the moisture content of the samples was less than 0.5 per cent on average by volume.
Additional in-situ testing from the independent lab Stork Twin City Testing evaluated the moisture content of EPS and XPS buried side-by-side for 15 years on a laboratory’s foundation in St. Paul, Minn. At the time the insulations were removed, the EPS was four times drier than the XPS. In fact, the EPS had only 4.8 per cent moisture by volume compared to 18.9 per cent moisture content for the XPS. After 30 days of drying time, the EPS had dried to only 0.7 per cent moisture by volume, while the XPS still contained 15.7 per cent moisture.
The Stork Twin City Testing insulation test also showed the degree to which moisture absorption impacts R-value. The XPS insulation lost 48 per cent of its R-value, compared to only a six per cent decrease for EPS.
Conclusion
While energy-efficient buildings are created by insulating from the bottom up, getting the best possible insulation for the project starts by understanding the product from the inside out. When conducting research of below-grade insulation, it is important to keep in mind laboratory results do not always tell the whole story when it comes to rigid foam insulation moisture performance.
David Stassi is field technical support manager at Insulfoam, a leading manufacturer of expanded polystyrene (EPS) insulation products. A graduate of Colorado State University, Stassi worked as a field sales representative for OMG Roofing Products prior to joining Insulfoam. Stassi can be reached via e-mail at david.stassi@insulfoam.com.