Shifting gears: A Passive House car dealership in the making
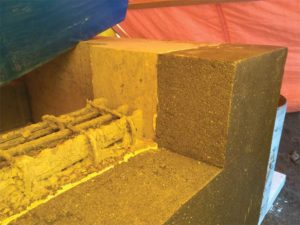
Image © Cover Architecture
Transparent components
A key challenge was mitigating the impact of the 65 per cent glazing (dictated by corporate design guidelines) on the west-facing storefront. Red Deer is nestled between two of the country’s sunniest cities (Calgary and Edmonton), receiving up to 50 per cent more west radiation than Germany. Overhangs also were not permitted, though these would have limited the impact of solar gain by blocking it when the western summer sun is low. The neighbourhood is flat and contains only low-rise buildings, so no natural shading exists. Deciduous tree planting was explored as part of the landscaping, but found to block too much of the solar gains in winter. External blinds were considered, but were not feasible due to the high wind gusts experienced in Red Deer. The owner also objected on esthetic grounds. Electrochromatic glazing where solar heat gain control can be regulated via an electric charge was explored, but a product of suitable characteristics (e.g. U-value and solar heat gain co-efficient [SHGC] range) could not be found for the project.
Ultimately, insulated spandrel panels in the top row of glazing and automated operable internal blinds with manual override were adopted. Unfortunately, these measures were insufficient to mitigate the high cooling load.
Window comfort has been found to be a key challenge on other cold climate projects. Only one Passive House Institute (PHI)-certified window for cold climates is commercially available in North America, but no certified curtain wall system is on the market. To meet the comfort criterion in Red Deer, the installed window U-value must be ≤ 0.61 W/m2/K (R-9.4). The building relies on centrally distributed heat blown down from above the glazing surfaces to ensure comfort requirements
are met.
Overhead doors
Overhead doors were another envelope challenge. The initial design called for seven overhead doors. The Passive House consultants devised an alternative design requiring only two. The client felt this disrupted service too much and eventually agreed to a compromise of four.
The initial concern with the doors was heat loss due to operation. Investigations revealed minimal air exchange
(15 m3 [530 cf]/hr/door opening), with negligible impact on heat loss. The greater concern turned out to be standby air leakage. Despite the reduced quantity, the overhead doors comprised 17 per cent of the total opening area in the wall. Conventional North American doors are not rated for airtightness, so could not be relied on. Therefore, the team had to look to Europe both for the doors and for an independent assessment of their airtightness. For this, the project team reviewed EN 13241-1, Industrial, commercial, and garage doors and gates–Product Standard, which defines airtightness classes. A Class 2 would increase the whole building airtightness to 0.08 air changes per hour [ach] @50Pa, representing a 20 per cent rise in whole-building air leakage (the building target for the project was 0.4 to meet the space heating demand). The author’s team located a product with an equivalent leakage of 0.04 ach@50Pa that increased the whole building leakage by an acceptable 10 per cent. Additionally, careful detailing ensured a durable seal between the door frame and the wall.
The unique uses in the building required a detailed investigation of internal heat gains (IHGs). The project team compiled a list of equipment early in the project to support more accurate Passive House Planning Package (PHPP) modelling from the start. As no data on car repair equipment could be found, the project team worked with the client to develop reasonable assumptions around usage and power ratings. Consideration had to be given to heat transfer between the showroom and other zones due to differing interior temperatures—the repair shop and drop-off zones are kept at 18 C (64 F) for the comfort of the repair personnel. Another key element to look into was the heat generated by the engines operated during repairs. The exhaust can reach 340 C (650 F) and its contribution to IHGs varies substantially based on the engine’s run time. Client input on typical repair procedures was crucial to estimate these gains.