Selecting external stone cladding material
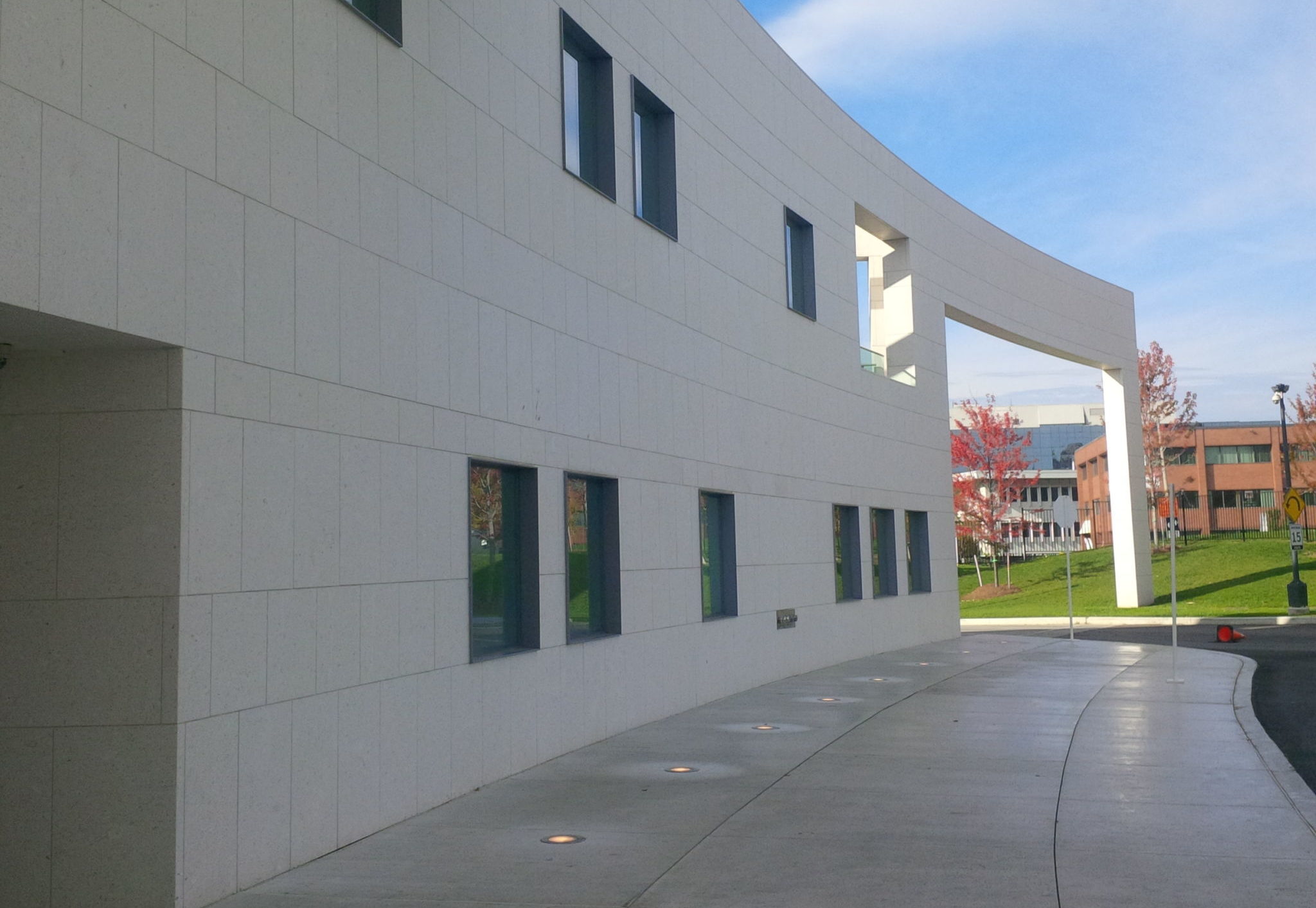
By Bill Wright
The exterior cladding of a building is exposed to some of the most extreme and harsh environmental conditions, including tremendous ranges and rates of change of temperatures. As such, determining what stone is suitable can be a daunting task. When choosing an appropriate stone, it is necessary to consider all the physical characteristics required to satisfy the performance criteria of the building design and location.
Factors in choosing the right material
Several common key factors must be considered when selecting a natural stone.
Water absorption rate
Generally, the lower the water absorption rate, the greater the frost resistance, stain resistance, and breaking strength of the stone. These are all desirable qualities for a cladding material. Stone cladding material should be tested according to ASTM C97/C97M, Test Methods for Absorption and Bulk Specific Gravity of Dimension Stone.
Resistance against frost is a function of water absorption rate. Any stone with an absorption rate of three per cent or lower is generally considered to be frost-resistant. Testing to support the application is strongly advised.
High breaking strength
High breaking strength is determined through use of ASTM C99/C99M, Test Method for Modulus of Rupture of Dimension Stone, and ASTM C170/C170M, Test Method for Compressive Strength of Dimension Stone.
Chemical resistance
The stone must have good chemical resistance to prevent deterioration from acid rain and other airborne pollutants. One must also take into consideration the cleaning and maintenance of the natural stone, as well as other parts of the wall assembly, including windows and exposed metalwork. Certain cleaning chemicals and processes can adversely affect the stone, so post-installation treatment of the materials must be considered during the stone selection phase.
Thermal movement and shock resistance
The stone’s rate of expansion and contraction due to temperature changes must be relatively similar to adjacent cladding materials. Significant differences can lead to
excessive stress. There is a difference between thermal shock and thermal movement. Thermal shock refers to the rate and range of temperature fluctuation within short periods. A façade with a southern or western solar orientation exposed to a sudden cool rainstorm can send the temperature of a cladding material plunging within a matter of minutes. Materials should be tested to ASTM C99/C99M, Test Method for Modulus of Rupture of Dimension Stone, and ASTM C170/C170M, Test Method for Compressive Strength of Dimension Stone.
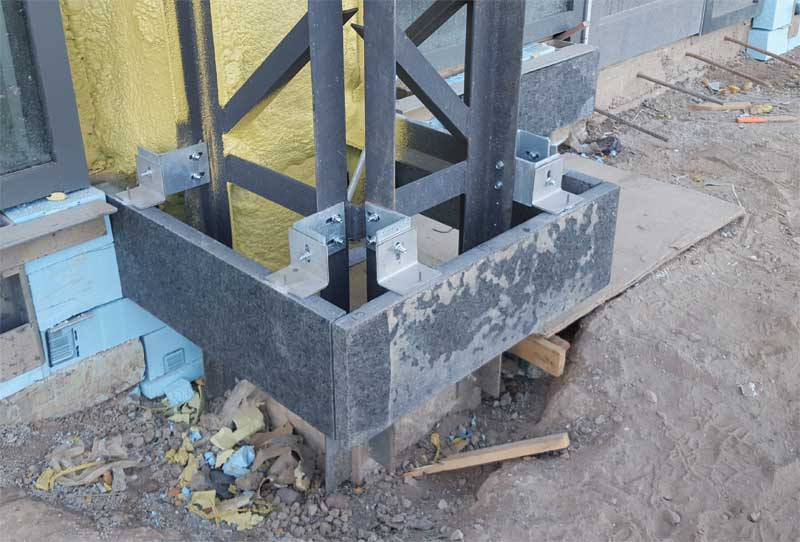
Photos courtesy GEM Capital
Natural stone options
Natural stone is classified geologically in three categories:
- igneous;
- sedimentary; and
- metamorphic.
Igneous
Igneous rocks are solidified from molten state—examples include basalt and granite. The latter has a primary mineral composition of feldspar and quartz. Some varieties of granite contain trace minerals that can cause discoloration or exfoliation after prolonged exposure to the weather. Granite has a distinct crystalline appearance and is extremely hard, dense, and resistant to scratches and acids. It is a very suitable stone for exterior walls, especially because the density and hardness of granite impart stability and high breaking strength resistance. Granites used in building construction, especially exterior walls, should have a maximum absorption rate of 0.40 per cent by weight according to ASTM standards.
While finishes of stone are primarily an esthetic consideration, it should be noted a thermal finish common on granite induces thermal shock damage to the first 3-mm (1/8-in.) depth of the stone face, and should be taken into account by deducting this layer when calculating thickness specifications. Other common finishes for external cladding are polished, honed, sandblasted, and bush-hammered. Commercially, granite can be found in hundreds of varieties, differentiated primarily by colour (a function of the mineral composition) and geographic origin.