Selecting clean doors for pharmaceutical and food operations
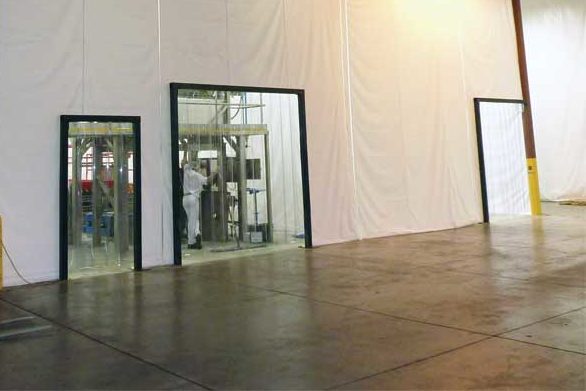
By Jon Schumacher
Regulatory requirements have become increasingly stringent across nearly every industry in North America. Perhaps no sphere has felt the impact of these tightened standards more than pharmaceutical and food manufacturing. While some regulations are created in response to new technology, equipment and processes, these industries have often needed to become more sophisticated to keep up with regulations. A prime example of this can be seen in the ongoing improvements in door and wall products specified for cleanroom and wash-down applications.
Cleanrooms are essential in contamination control for processes in the pharmaceutical and food industries. In fact, planning for these particular spaces has evolved into a specific area of industrial design. The primary challenge for these designers is keeping contaminants generated by people, processes, facilities, and equipment from being suspended in the air. Since prevention is more effective than diminishing an existing problem, one of the best ways to minimize contamination is to stop contaminants from ever entering the room in the first place.
The function of cleanrooms is to create environments that maintain an extremely low level of environmental pollutants such as dust, airborne microbes, aerosol particles, and chemical vapours. Every cleanroom has a controlled level of contamination specified by the number of particles per cubic metre at a specified particle size.
To give perspective, the ambient outside air in a typical city contains 35 million particles per cubic metre in the range of 0.5 μm (0.02 mils) and larger in diameter, corresponding to an ISO 9 cleanroom (per ISO 14644-1, Cleanrooms and Associated Controlled Environments−Part 1: Classification of Air Cleanliness by Particle Concentration), while an ISO 1 cleanroom allows no particles in that size range and only 12 particles per cubic metre of 0.3 μm (0.01 mils) and smaller.
The pharmaceutical industry generally requires ISO 6 to 8. These levels of cleanrooms play a crucial role in the manufacturing of products required to be free from microbial and particulate contamination and protected from moisture. Regulations in the food industry are not quite as stringent as the pharmaceutical industry with respect to the particulates range, but clean areas and wash-down walls are equally important in the prevention of contamination.
In these industries, doors and walls play an essential role in maintaining clean operations and product integrity. High-performance fabric doors (also known as ‘industrial curtains’) fit virtually anywhere and are uniquely designed to address the need for environmental control, productivity, safety, and cleanliness. They are used not only to prevent cross-contamination, but also to aid in maintaining correct room pressures, air circulation rates, and ensuring optimal operating efficiency.
While anti-microbial walls have always been important in segmenting environments, there is a growing use of flexible, industrial fabric walls for applications subject to wash-down protocols. They are quicker, easier, and less expensive to install than traditional construction. The assemblies also offer an additional benefit in that they can be moved or reconfigured to satisfy future changes in the process or floor plan. (For more on these assemblies, see this author’s previous Construction Canada article in the June 2015 issue by visiting www.constructioncanada.net/understanding-high-speed-doors-and-industrial-curtains.)